Technology and Applications of routing cnc
Routing CNC (Computer Numerical Control) technology has revolutionized the manufacturing and fabrication industries by allowing for precise and automated cutting, shaping, and engraving of materials. CNC routing machines utilize computer-generated designs to control the movement of cutting tools along multiple axes, resulting in high accuracy and repeatability.
One of the primary applications of CNC routing is in woodworking. It allows for intricate designs and detailed carvings, significantly enhancing the production of furniture, cabinetry, and decorative items. Beyond wood, CNC routers are versatile enough to work with various materials, including plastics, composites, and soft metals, making them invaluable in industries such as signage, aerospace, and automotive.
In addition to traditional manufacturing, CNC routing finds applications in prototyping and custom fabrication. Designers and engineers can quickly turn their digital models into physical products, facilitating rapid iteration and product development. This capability is particularly beneficial in the maker movement, where individuals and small businesses leverage CNC technology for creative projects and small-batch production runs.
Moreover, advancements in CNC routing technology, including improved software for design and simulation, have made it easier for users to optimize their workflows. Features such as toolpath optimization, collision detection, and real-time monitoring enhance productivity and reduce material waste.
Overall, the integration of CNC routing technology into various sectors not only streamlines production processes but also enables greater creativity and customization, making it a cornerstone of modern manufacturing practices. With its expanding capabilities, CNC routing is poised to play an even more significant role in the future of fabrication and design.
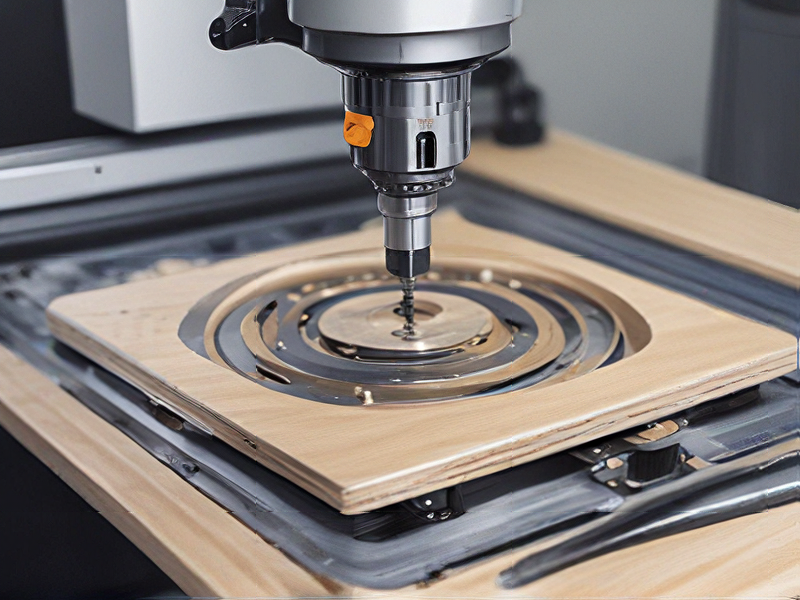
Quality Testing Methods for routing cnc and how to control quality
Quality testing methods for routing CNC (Computer Numerical Control) machining are essential to ensure precision, accuracy, and consistency in the manufactured parts. Here are some key methods and controls:
1. Visual Inspection
– Initially, perform a visual inspection of the machined parts for visible defects such as gaps, burrs, or misalignment.
2. Dimensional Verification
– Use calipers, micrometers, and gauge blocks to measure dimensions against specified tolerances. Ensure that critical features fall within defined limits.
3. Surface Finish Testing
– Employ surface roughness testers to assess the finish quality. Compare the results against the specifications to ensure smoothness and absence of tool marks.
4. CMM (Coordinate Measuring Machine) Inspection
– Utilize CMMs for precise measurements of complex geometries. This ensures that all aspects of the component meet design specifications.
5. Tool Wear Monitoring
– Regularly monitor the condition of cutting tools. Implementing a tool wear management system can prevent degradation in quality caused by dull tools.
6. Process Capability Analysis
– Conduct statistical process control (SPC) to evaluate the capability of machining processes. This helps in identifying variations and maintaining consistent quality.
7. Documentation and Traceability
– Maintain detailed records of all inspections, measurements, and any deviations encountered during production. This will provide a robust framework for quality control and traceability.
8. Training and Standard Operating Procedures (SOPs)
– Ensure that operators are well-trained and follow standardized procedures to minimize human error in CNC machining processes.
By employing these quality testing methods and controls, manufacturers can enhance the reliability and precision of routing CNC operations, ultimately leading to superior product quality.
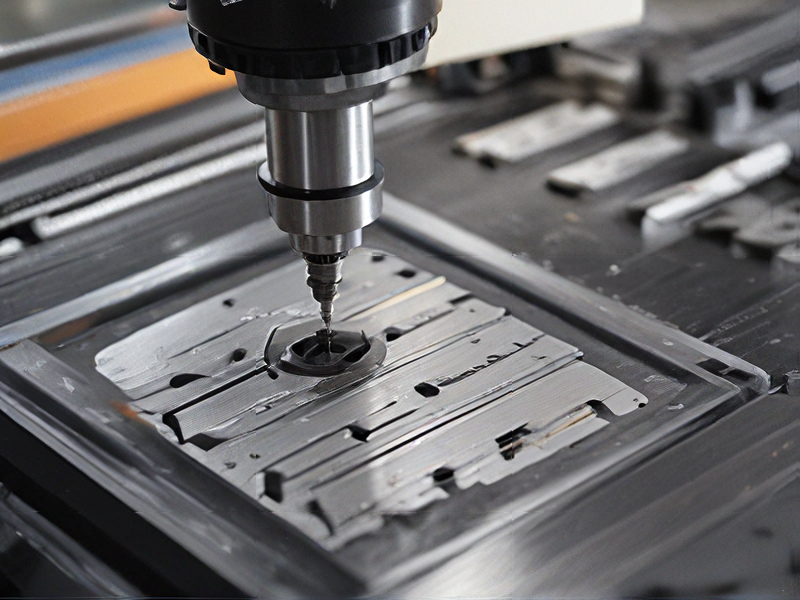
Tips for Procurement and Considerations when Purchasing from routing cnc
When considering procurement from a routing CNC (Computer Numerical Control) machine, it’s essential to evaluate several factors to ensure an optimal purchase. Here are key tips and considerations:
1. Define Your Needs: Clearly outline your project requirements, such as material types, desired accuracy, production volume, and specific features (e.g., spindle speed, tool changes).
2. Assess the Supplier: Research potential suppliers for their reputation, experience, and customer service. Look for reviews or case studies to gauge their reliability.
3. Evaluate Machine Specifications: Ensure that the CNC router meets your specifications, including bed size, maximum cutting thickness, power requirements, and precision. Check if it supports the software you intend to use.
4. Total Cost of Ownership: Beyond the initial purchase price, consider maintenance costs, spare parts availability, energy consumption, and potential downtime.
5. Training and Support: Inquire about training programs for your team and the level of technical support offered. A good supplier will provide comprehensive resources to ensure you can operate the machine efficiently.
6. Warranty and Service Agreements: Understand the warranty terms and any service contracts offered. Reliable after-sales support can save significant downtime costs.
7. Technology Integration: Check if the CNC machine can easily integrate with your existing systems, such as CAD/CAM software, to streamline workflows.
8. Future Upgradability: Consider whether the machine can be updated or expanded in the future to accommodate evolving business needs.
9. Visit the Facility: If possible, visit the supplier’s facility to see the machines in action and gauge the manufacturing quality firsthand.
10. Negotiate Terms: Don’t hesitate to negotiate the price, delivery timelines, and payment terms to optimize your purchase.
By carefully considering these factors, you can make a well-informed decision that aligns with your operational requirements and budget.
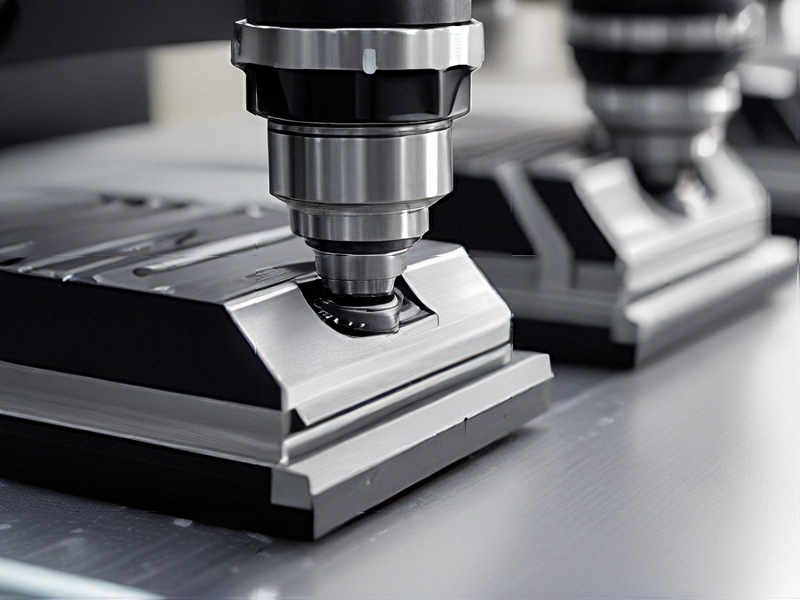
FAQs on Sourcing and Manufacturing from routing cnc in China
FAQs on Sourcing and Manufacturing CNC Components in China
1. What is CNC machining?
CNC (Computer Numerical Control) machining is a manufacturing process that uses programmed computer software to control the movement of factory tools and machinery. This enables high precision in creating complex parts.
2. Why source CNC machining in China?
China offers competitive pricing, a vast supplier network, skilled labor, and advanced manufacturing technologies. Many companies benefit from fast lead times and the ability to scale production.
3. How do I find reliable manufacturers?
Start by researching reputable platforms such as Alibaba, Made-in-China, or Globalsources. Look for suppliers with positive reviews, certifications (like ISO), and experience in your specific sector.
4. What factors should I consider when selecting a supplier?
Consider quality control processes, production capacity, lead times, communication skills, and post-manufacturing support. Request samples to evaluate their work quality.
5. What are common payment terms?
Payment terms vary, but commonly used methods include upfront deposits (30-50%) and full payment before shipping. Secure payment options, like PayPal or Trade Assurance on Alibaba, are recommended.
6. How can I protect my intellectual property?
To protect your designs, use non-disclosure agreements (NDAs) and consider trademark registration. Choose manufacturers with a good reputation for respecting intellectual property rights.
7. What should I be aware of regarding shipping and import tariffs?
Be prepared for shipping costs, potential tariffs, and customs duties based on your country’s import regulations. Work with a reliable freight forwarder to ensure compliance and smooth delivery.
8. How do I manage quality control?
Implement quality inspections during production and before shipment. You can hire third-party QC services or send a representative to oversee processes directly.
For further assistance, consult with industry experts or sourcing agents to streamline your manufacturing journey in China.
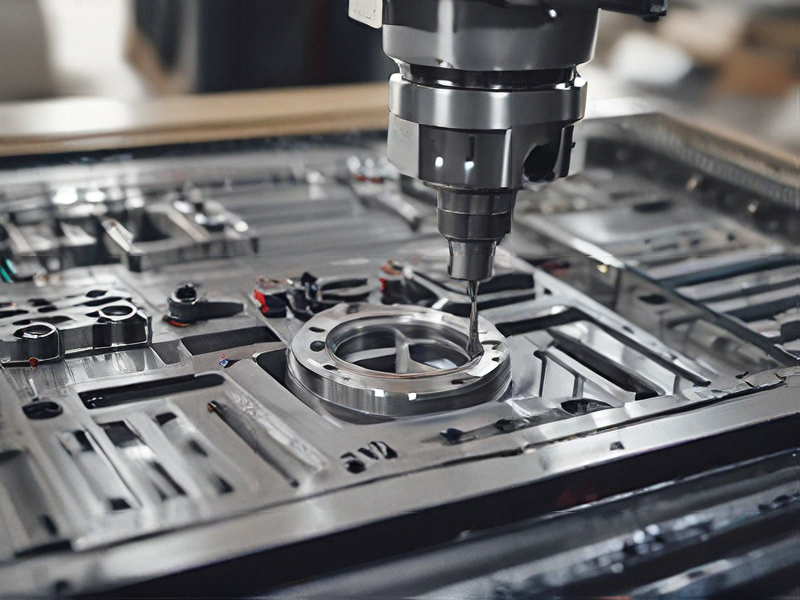