Technology and Applications of sheet metal
Sheet metal is a versatile material widely used in various industries due to its malleability, strength, and lightweight properties. It is typically made from metals like steel, aluminum, copper, and brass, and is manufactured through processes such as rolling, stamping, and cutting.
Technology: Modern sheet metal fabrication employs advanced techniques, including Computer Numerical Control (CNC) machining, laser cutting, and waterjet cutting. These technologies enhance precision and efficiency, allowing for complex shapes and intricate designs. Furthermore, software like CAD (Computer-Aided Design) plays a crucial role in the design and prototyping stages, facilitating rapid iterations and reducing lead times.
Applications: The applications of sheet metal are extensive and varied. In the automotive industry, sheet metal is fundamental in manufacturing body panels, frames, and components, helping to reduce weight and improve fuel efficiency. The aerospace sector utilizes lightweight sheet metal in aircraft structures, contributing to performance and safety.
In the construction industry, sheet metal is used for roofing, siding, and HVAC systems, offering durability and weather resistance. Additionally, consumer electronics often incorporate sheet metal for enclosures, providing protection and aesthetics for devices.
Moreover, sheet metal is integral to the fabrication of furniture, appliances, and industrial equipment, showcasing its adaptability across sectors. The rise of automation and smart manufacturing continues to drive innovation in sheet metal applications, further expanding its potential in the modern economy.
In conclusion, sheet metal technology and its diverse applications underline its significance in contemporary manufacturing, highlighting the balance between functionality, efficiency, and design.
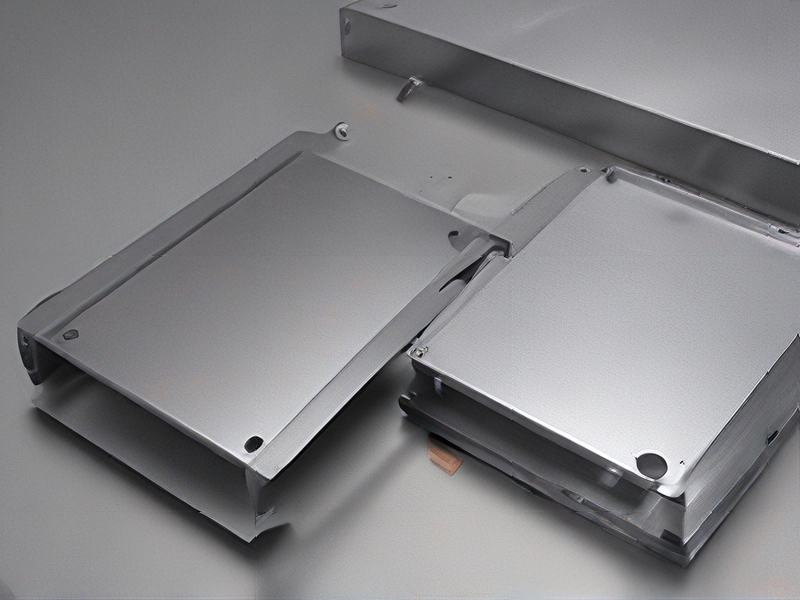
Quality Testing Methods for sheet metal and how to control quality
Quality testing methods for sheet metal are essential to ensure that the final products meet the necessary specifications and standards. Here are some common methods:
1. Visual Inspection: This is a preliminary method where trained personnel check for surface defects such as scratches, dents, or discoloration. It’s quick and helps identify obvious issues.
2. Dimensional Inspection: Using calipers, micrometers, or laser measuring devices, the dimensions of the sheet metal are verified against specified tolerances. This ensures accurate fit and function in assemblies.
3. Hardness Testing: Methods like Brinell, Rockwell, or Vickers hardness tests assess the material’s resistance to deformation. This is crucial for understanding how the metal will perform under stress.
4. Tensile Testing: This method measures the material’s strength, ductility, and elasticity. A specimen is pulled until it breaks, providing insights into the metal’s behavior under load.
5. Surface Roughness Testing: Instruments such as profilometers measure the roughness of the metal surface, which affects aesthetic and functional qualities, especially in applications requiring precision fit.
To control quality, implement a robust Quality Management System (QMS) that includes:
– Standard Operating Procedures (SOPs): Establish clear guidelines for all processes to minimize variability.
– Training Programs: Regular training ensures that staff are well-informed about quality standards and inspection methods.
– Regular Audits: Conduct internal and external audits to verify compliance with quality standards.
– Statistical Process Control (SPC): Use statistical methods to monitor and control manufacturing processes.
By integrating these testing methods and quality control measures, manufacturers can ensure the reliability and performance of their sheet metal products.
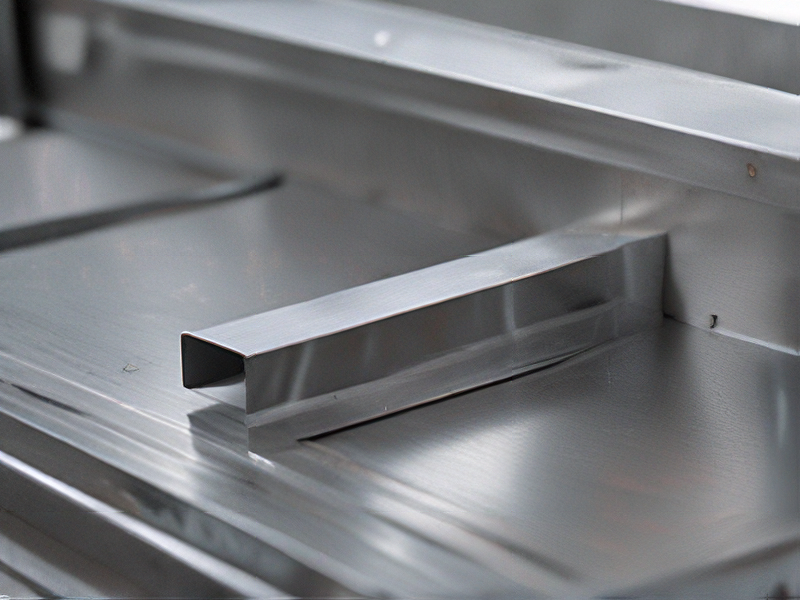
Tips for Procurement and Considerations when Purchasing from sheet metal
When procuring sheet metal, consider the following tips and factors to ensure optimal purchasing decisions:
1. Material Specifications: Clearly define the type of sheet metal needed (e.g., aluminum, stainless steel, galvanized steel). Consider thickness, alloy composition, and temper as these affect strength and corrosion resistance.
2. Supplier Evaluation: Research potential suppliers for their reputation, reliability, and quality. Look for certifications (e.g., ISO) and customer reviews to gauge their performance and consistency.
3. Quantity and Pricing: Determine your required quantity and seek bulk pricing discounts. Obtain quotes from multiple suppliers to compare prices, but remember to consider the total cost of ownership, including shipping and handling.
4. Lead Times: Inquire about lead times and ensure they align with your project schedules. Delays can lead to increased costs and project setbacks.
5. Customization Options: If you require specific dimensions or finishes, check if the supplier offers customization services. Ensure they can meet your needs without compromising quality.
6. Quality Control: Ask about the supplier’s quality control processes to ensure the sheet metal meets specifications. Request samples if possible.
7. Sustainability Practices: Consider suppliers that emphasize sustainable practices, such as recycling and minimizing waste, which can reflect positively on your company’s values.
8. Post-purchase Support: Evaluate the post-purchase support, including return policies and customer service. Establish a good line of communication for any future concerns.
By following these considerations, you can make informed decisions that satisfy both quality and budgetary requirements in your sheet metal procurement process.
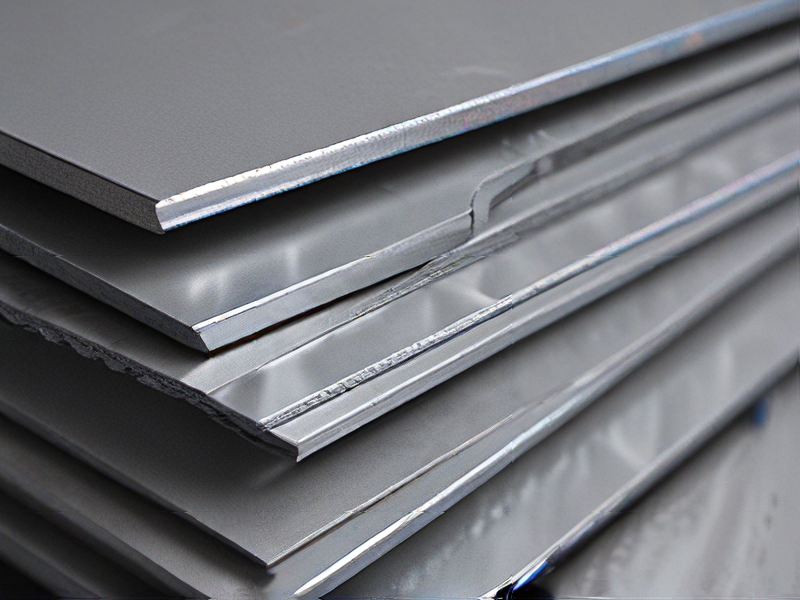
FAQs on Sourcing and Manufacturing from sheet metal in China
FAQs on Sourcing and Manufacturing Sheet Metal in China
1. What types of sheet metal products can I source from China?
China manufactures a wide range of sheet metal products, including brackets, enclosures, panels, and custom parts. Industries served include automotive, aerospace, electronics, and construction.
2. How do I find reliable manufacturers?
To find reputable manufacturers, consider using platforms like Alibaba, Global Sources, or sourcing agents. Look for verified suppliers with good reviews, certifications, and a substantial track record.
3. What certifications should manufacturers have?
Ensure your manufacturer holds relevant quality certifications such as ISO 9001, ISO 14001, and specific industry-related certifications (e.g., RoHS for electronics). This indicates adherence to international quality standards.
4. What is the average lead time for production?
Lead times vary based on order size and complexity but typically range from 2 to 6 weeks. It’s essential to discuss timelines upfront.
5. How can I ensure product quality?
Implement quality control measures throughout the production process. This may include initial samples, in-factory inspections, and third-party quality checks before shipment.
6. What are common payment terms?
Typically, manufacturers request a 30-50% deposit upfront, with the balance due before shipment. It’s advisable to use secure payment methods such as Trade Assurance on Alibaba.
7. Are there import duties and tariffs?
Yes, importing sheet metal products into your country may incur duties and tariffs. Check with your local customs authority to understand the specific charges applicable to your goods.
8. How can I manage language barriers?
Consider hiring a sourcing agent fluent in both English and Chinese. This can facilitate smoother communication and help navigate any cultural nuances in business practices.
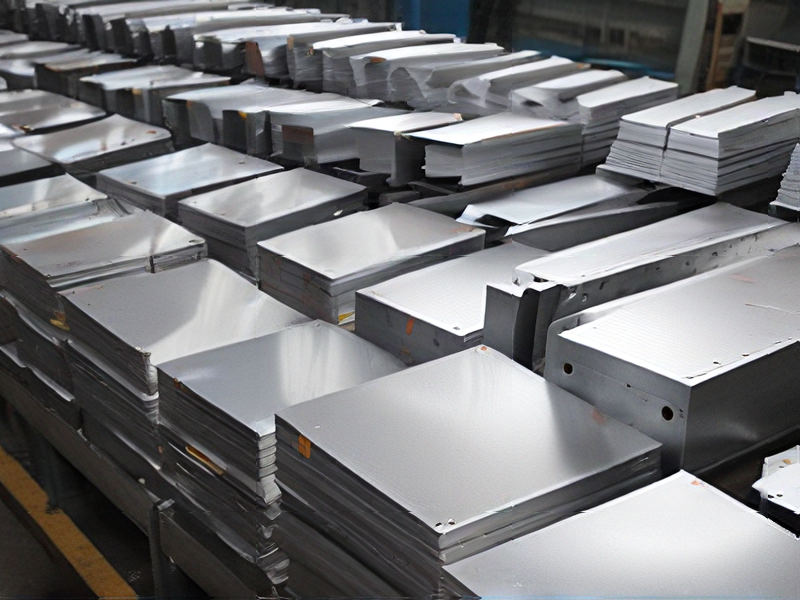