Technology and Applications of sheet metal and fabrication
Sheet metal and fabrication involve the processes of forming, cutting, and assembling thin metal sheets into various products. This technology is integral to numerous industries, including automotive, aerospace, construction, and electronics.
Technology:
1. Cutting: Techniques include laser cutting, plasma cutting, and water jet cutting. Laser cutting is highly precise, making it suitable for intricate designs, while plasma cutting is faster and ideal for thicker materials. Water jet cutting uses high-pressure water to cut through metal without generating heat, preserving material integrity.
2. Forming: Methods such as bending, rolling, and stamping shape the metal. CNC (Computer Numerical Control) machines enhance precision and repeatability in these processes. Bending creates angles and curves, rolling forms cylindrical shapes, and stamping uses dies to imprint patterns or cut shapes.
3. Joining: Techniques like welding, riveting, and adhesive bonding are used to assemble sheet metal components. Welding, including MIG and TIG, is preferred for its strength and durability. Riveting is common in aerospace for its reliability, while adhesive bonding is used where weight savings are crucial.
Applications:
1. Automotive Industry: Sheet metal is used for body panels, chassis components, and exhaust systems. High precision and strength are required to meet safety and performance standards.
2. Aerospace: Lightweight yet strong materials are essential. Sheet metal fabrication produces aircraft skins, wings, and structural components, where precision and quality control are paramount.
3. Construction: Roofing, HVAC systems, and structural elements rely on sheet metal for its durability and formability. Fabrication allows for custom shapes and sizes to meet specific architectural needs.
4. Electronics: Enclosures, brackets, and heat sinks are fabricated from sheet metal to protect and support electronic components. Precision and thermal management are critical factors.
In summary, sheet metal and fabrication technologies are versatile and critical in producing high-quality, durable components across various industries. Advancements in cutting, forming, and joining techniques continue to enhance efficiency and precision in this field.
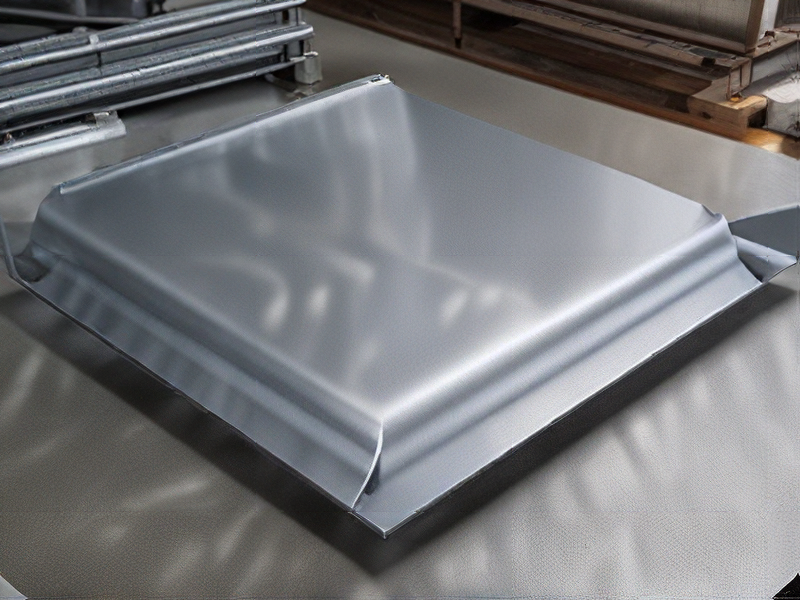
Quality Testing Methods for sheet metal and fabrication and how to control quality
Quality testing methods for sheet metal and fabrication ensure products meet specifications and standards. Key methods include:
1. Visual Inspection: Detects surface defects like scratches, dents, and corrosion. Inspectors use visual aids like magnifying glasses and borescopes.
2. Dimensional Inspection: Verifies dimensions against design specifications using calipers, micrometers, and coordinate measuring machines (CMM).
3. Mechanical Testing:
– Tensile Testing: Measures the material’s strength and ductility by pulling it until it breaks.
– Hardness Testing: Assesses resistance to indentation using Rockwell, Brinell, or Vickers methods.
– Fatigue Testing: Determines the material’s ability to withstand repeated loading.
4. Non-Destructive Testing (NDT):
– Ultrasonic Testing (UT): Uses high-frequency sound waves to detect internal flaws.
– Magnetic Particle Testing (MPT): Identifies surface and near-surface defects in ferromagnetic materials.
– Dye Penetrant Testing (DPT): Reveals surface cracks using a dye that penetrates flaws.
– Radiographic Testing (RT): Uses X-rays or gamma rays to inspect internal structures.
To control quality, follow these steps:
1. Standardization: Implement standardized procedures and specifications to ensure consistency.
2. Training: Provide regular training for inspectors and operators to maintain high skill levels.
3. Quality Management Systems (QMS): Adopt systems like ISO 9001 to structure quality control processes.
4. Documentation: Maintain detailed records of inspections, tests, and corrective actions.
5. Continuous Improvement: Regularly review processes and implement improvements based on feedback and test results.
6. Supplier Quality Management: Ensure raw materials and components from suppliers meet required standards.
By employing these methods and controls, manufacturers can ensure the high quality of sheet metal and fabricated products, minimizing defects and enhancing performance.
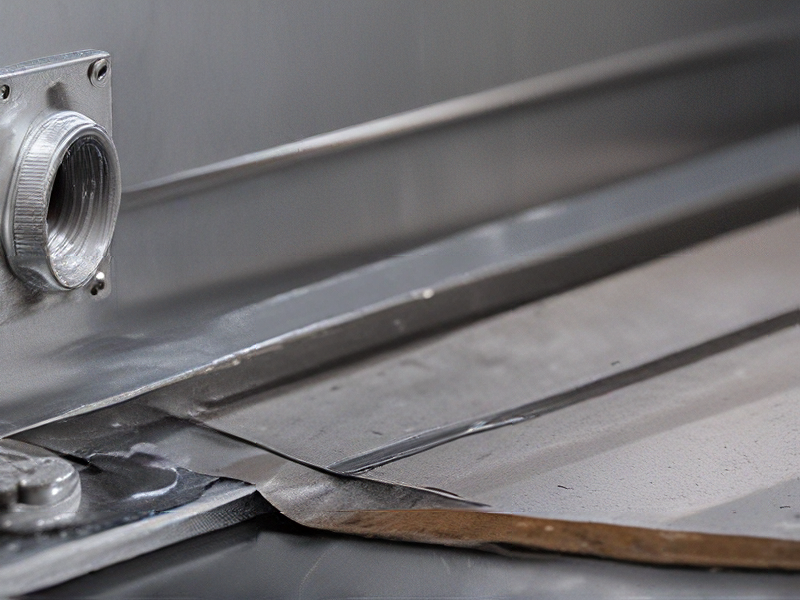
Tips for Procurement and Considerations when Purchasing from sheet metal and fabrication
When procuring sheet metal and fabrication services, consider the following tips and key considerations to ensure quality, cost-effectiveness, and timely delivery:
Tips for Procurement:
1. Define Requirements Clearly: Specify material type, thickness, dimensions, tolerances, and any special finishes or treatments. Detailed requirements help suppliers provide accurate quotes and ensure the final product meets expectations.
2. Supplier Evaluation: Assess potential suppliers based on their capabilities, experience, certifications (such as ISO 9001), and past performance. Site visits and audits can provide insights into their production processes and quality control.
3. Request for Quotations (RFQs): Send detailed RFQs to multiple suppliers to compare pricing, lead times, and terms. Ensure all suppliers are quoting on the same specifications to make valid comparisons.
4. Quality Assurance: Look for suppliers with robust quality assurance processes. Ask about their inspection and testing procedures and how they handle defects and reworks.
5. Capacity and Lead Time: Ensure the supplier can meet your volume requirements and delivery schedule. Discuss contingency plans for potential delays or production issues.
6. Technical Support: Choose suppliers who offer technical support and can assist with design improvements or cost-saving opportunities. Collaborative relationships can lead to better outcomes.
Considerations when Purchasing:
1. Material Selection: Choose the appropriate material (e.g., steel, aluminum, stainless steel) based on the application, considering factors like strength, weight, corrosion resistance, and cost.
2. Fabrication Methods: Understand the different fabrication methods (e.g., cutting, bending, welding) and select the most suitable process for your needs. Each method has its own cost and technical implications.
3. Tolerance and Precision: Specify the required tolerances and precision. Higher precision typically increases costs, so balance accuracy with budget constraints.
4. Surface Finish: Determine if surface treatments like painting, powder coating, or galvanizing are necessary for protection or aesthetic reasons. These can impact cost and lead time.
5. Logistics and Shipping: Consider the logistics of shipping large or heavy metal parts. Factor in transportation costs, packaging requirements, and potential customs or import regulations if sourcing internationally.
6. Total Cost of Ownership (TCO): Evaluate not just the purchase price but the total cost of ownership, including maintenance, lifespan, and potential downtime costs.
By following these tips and considerations, you can make informed decisions that optimize quality, cost, and delivery in sheet metal and fabrication procurement.
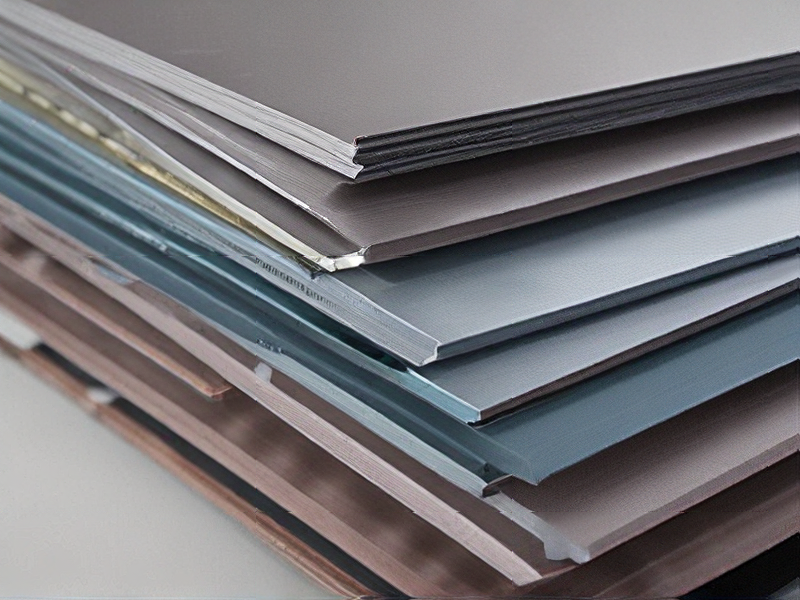
FAQs on Sourcing and Manufacturing from sheet metal and fabrication in China
FAQs on Sourcing and Manufacturing from Sheet Metal and Fabrication in China
1. Why source sheet metal and fabrication from China?
– China offers competitive pricing, a vast selection of materials, advanced technology, and a skilled workforce, making it an attractive destination for sheet metal and fabrication.
2. What types of sheet metal products can be sourced from China?
– Products range from simple parts like brackets and enclosures to complex assemblies such as automotive components, medical devices, and industrial machinery parts.
3. How to ensure quality when sourcing from China?
– Conduct thorough vetting of suppliers, request samples, perform factory audits, and establish clear quality control processes. Third-party inspection services can also be utilized.
4. What are the common materials used in sheet metal fabrication in China?
– Common materials include stainless steel, aluminum, carbon steel, and various alloys. Availability and cost of materials can vary, so it’s crucial to confirm with suppliers.
5. How to find reliable suppliers?
– Use platforms like Alibaba, Made-in-China, and Global Sources. Attending trade shows and seeking recommendations from industry networks can also help.
6. What are the typical lead times for sheet metal fabrication?
– Lead times can vary based on the complexity and volume of the order, typically ranging from 2 to 8 weeks. It’s important to confirm timelines with your supplier.
7. How is shipping and logistics handled?
– Suppliers often handle logistics, offering FOB (Free on Board) terms. It’s vital to discuss shipping options and costs upfront, including potential tariffs and customs duties.
8. What are the payment terms?
– Common payment terms include a deposit (30-50%) with the balance paid before shipment. Letters of credit and escrow services can provide additional security.
9. What are the risks involved?
– Risks include quality issues, communication barriers, intellectual property theft, and logistical challenges. Mitigate risks by having clear contracts, regular communication, and using trusted suppliers.
10. How to handle post-manufacturing support and warranty?
– Clarify warranty terms and support policies with your supplier before placing an order. Having a local representative or third-party service can help manage after-sales support.
By addressing these key points, businesses can effectively navigate the complexities of sourcing and manufacturing sheet metal and fabrication products from China.
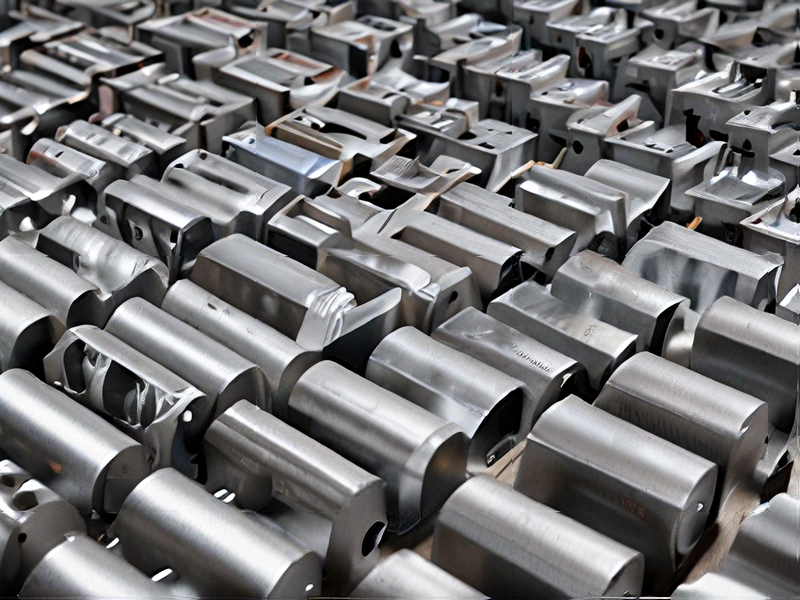