Technology and Applications of sheet metal cost
Sheet metal fabrication is a crucial process across various industries due to its versatility and cost-effectiveness. The cost of sheet metal components is influenced by several factors, including material type, thickness, complexity of design, and production volume. Common materials like steel, aluminum, and stainless steel vary significantly in price and affect overall project costs. Thicker materials require more raw material and longer machining times, increasing expenses.
Technology plays a pivotal role in optimizing sheet metal costs. Computer-aided design (CAD) software allows precise digital modeling, minimizing material waste and ensuring efficient use of resources. Computer-aided manufacturing (CAM) software complements CAD by programming CNC (Computer Numerical Control) machines to cut and shape sheet metal with high accuracy and repeatability, reducing labor costs and enhancing productivity.
Applications of sheet metal are extensive, ranging from automotive and aerospace industries to electronics and construction. In automotive manufacturing, sheet metal forms the basis of vehicle bodies and structural components, balancing strength and weight. In aerospace, sheet metal is used for aircraft fuselages, wings, and internal structural elements, where durability and precision are critical.
In conclusion, the cost-effectiveness of sheet metal fabrication is enhanced through technological advancements in CAD/CAM and efficient material utilization. Its applications span various sectors, leveraging its versatility and economic benefits in manufacturing durable and complex components.
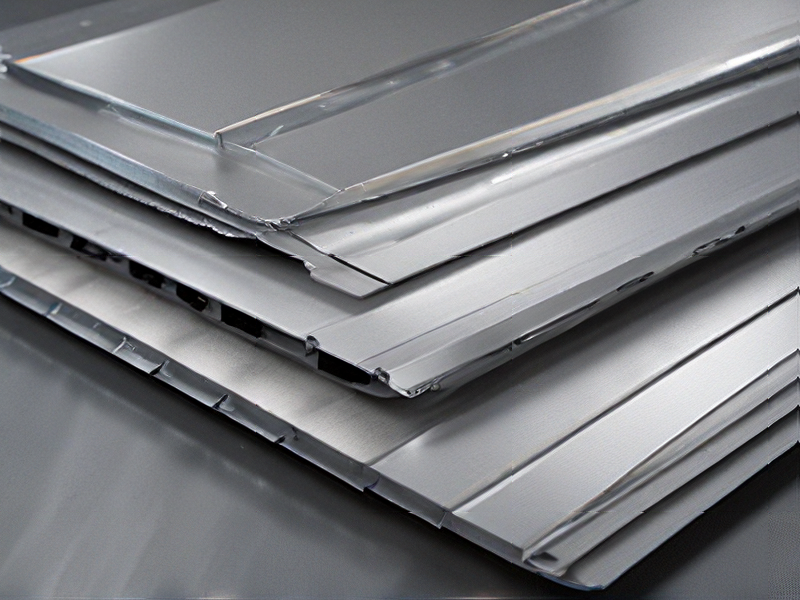
Quality Testing Methods for sheet metal cost and how to control quality
Quality Testing Methods for Sheet Metal Cost
1. Material Inspection:
– Chemical Composition Analysis: Ensures the metal has the correct alloy composition using spectrometry or X-ray fluorescence (XRF).
– Mechanical Properties Testing: Tensile tests, hardness tests, and impact tests to verify material strength, ductility, and toughness.
2. Dimensional Inspection:
– Precision Measurement Tools: Use calipers, micrometers, and coordinate measuring machines (CMM) to check dimensions against specifications.
– Laser Scanning: Provides detailed 3D measurements for complex shapes.
3. Surface Inspection:
– Visual Inspection: Identifies surface defects like scratches, dents, and corrosion.
– Surface Roughness Testing: Measures the smoothness of the sheet metal surface using profilometers.
4. Non-Destructive Testing (NDT):
– Ultrasonic Testing: Detects internal flaws like cracks and voids.
– Magnetic Particle Testing: Identifies surface and near-surface defects in ferromagnetic materials.
– Dye Penetrant Inspection: Reveals surface cracks by applying a dye and developer.
Controlling Quality
1. Supplier Quality Management:
– Supplier Audits: Regular audits to ensure suppliers meet quality standards.
– Material Certification: Require suppliers to provide material test reports and certifications.
2. In-Process Quality Control:
– Process Monitoring: Use statistical process control (SPC) to monitor and control the manufacturing process.
– First Article Inspection (FAI): Verify that the first piece produced meets all specifications before mass production.
3. Final Product Inspection:
– Batch Sampling: Inspect random samples from each batch to ensure consistency.
– End-of-Line Testing: Conduct functional tests on the final product to ensure it meets performance requirements.
4. Continuous Improvement:
– Root Cause Analysis: Investigate defects to determine their root cause and implement corrective actions.
– Training and Development: Regularly train employees on quality standards and procedures.
Implementing these testing methods and control measures ensures high-quality sheet metal products while optimizing costs.
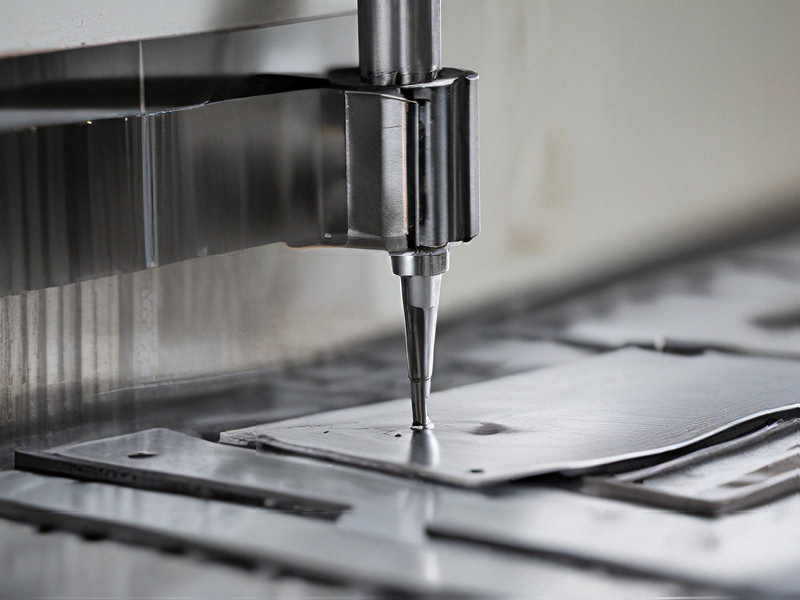
Tips for Procurement and Considerations when Purchasing from sheet metal cost
When procuring sheet metal, several considerations can optimize costs and ensure quality:
1. Material Selection: Choose the appropriate type of sheet metal (e.g., stainless steel, aluminum) based on your project’s requirements for strength, corrosion resistance, and aesthetics.
2. Supplier Evaluation: Assess suppliers based on their track record, certifications (ISO standards), and ability to meet deadlines. Request samples and references to gauge quality.
3. Cost Analysis: Compare quotes from multiple suppliers. Consider total costs including shipping, handling, and potential tariffs or taxes. Volume discounts may apply for larger orders.
4. Quality Assurance: Specify quality standards and inspect samples or prototypes before full production. Quality control processes ensure consistency and reduce defects.
5. Lead Times: Balance cost savings with lead times. Expedited manufacturing may increase costs but reduce downtime and improve project timelines.
6. Design Optimization: Work closely with suppliers to optimize designs for manufacturability, minimizing material waste and production costs.
7. Packaging and Logistics: Factor in packaging requirements to prevent damage during transit. Optimize logistics to reduce transportation costs and environmental impact.
8. Long-term Relationships: Establishing long-term partnerships with reliable suppliers can lead to better pricing, priority service, and improved product consistency over time.
By prioritizing these considerations, you can streamline procurement processes, reduce costs, and ensure high-quality sheet metal products for your projects.
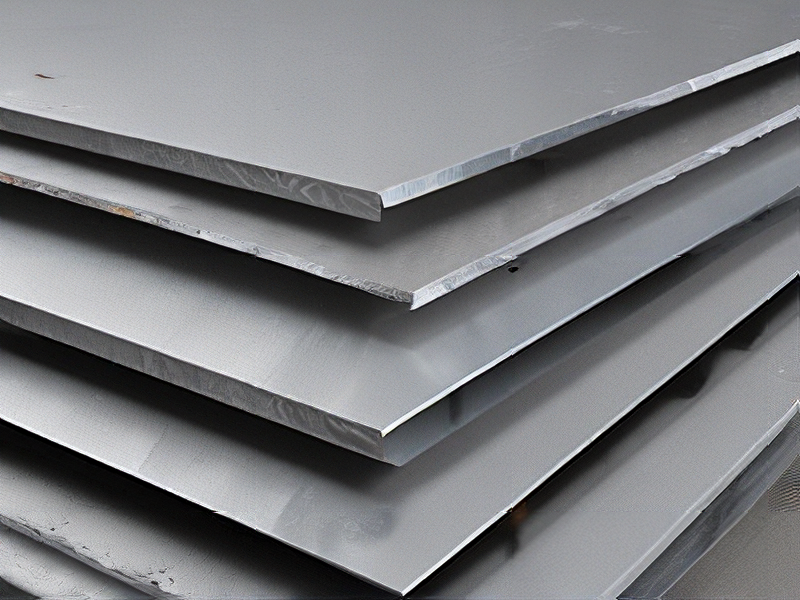
FAQs on Sourcing and Manufacturing from sheet metal cost in China
Certainly! When sourcing and manufacturing sheet metal components in China, it’s essential to consider several key factors:
1. Cost Efficiency: China offers competitive pricing due to lower labor costs and economies of scale in manufacturing. However, prices can vary widely based on material quality, complexity of design, and order volume.
2. Supplier Selection: Conduct thorough research to find reputable suppliers with experience in sheet metal fabrication. Look for certifications (ISO, CE) and customer reviews to assess reliability and quality standards.
3. Quality Control: Implement stringent quality control measures throughout the production process. This may involve regular inspections, testing prototypes, and establishing clear specifications to ensure the final product meets your standards.
4. Communication: Effective communication is crucial to avoid misunderstandings or delays. Clear specifications, detailed drawings, and regular updates help maintain transparency and alignment with your expectations.
5. Logistics and Shipping: Factor in logistics costs, shipping times, and import/export duties when planning your budget and timeline. Choose reliable shipping methods and consider potential delays during peak seasons or unforeseen circumstances.
6. Intellectual Property Protection: Protect your designs and intellectual property by working with suppliers who respect confidentiality agreements and have systems in place to safeguard your information.
By carefully navigating these considerations, you can optimize your sourcing and manufacturing process for sheet metal components in China, balancing cost-effectiveness with quality and reliability.
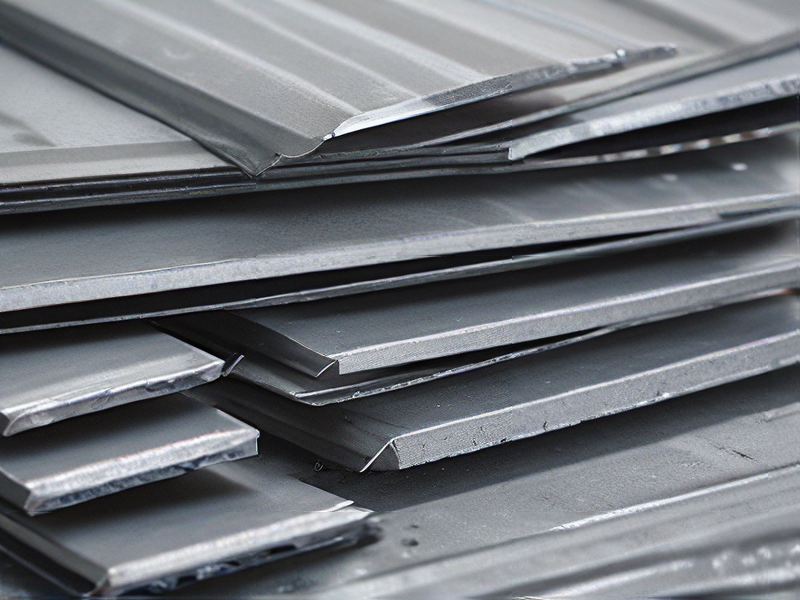