Technology and Applications of sheet metal fabrications
Sheet metal fabrication is a crucial process in manufacturing, involving the cutting, bending, and assembling of thin metal sheets to create various structures and components. This technology is widely used due to its versatility, precision, and cost-effectiveness.
Technology
1. Cutting: Methods include laser cutting, plasma cutting, and water jet cutting. Laser cutting is highly precise and suitable for intricate shapes, while plasma cutting is faster and ideal for thicker metals.
2. Bending: Press brakes and rolling machines are commonly used to bend sheet metal into desired angles and shapes.
3. Assembling: Techniques like welding, riveting, and adhesive bonding are used to join metal parts. Welding is strong and permanent, while riveting is often used for parts that may need to be disassembled.
Applications
1. Automotive Industry: Sheet metal is used in car bodies, chassis, and other components due to its strength and malleability.
2. Aerospace: Precision and lightweight requirements in aerospace make sheet metal fabrication essential for components like fuselages and wings.
3. Construction: Sheet metal is used for roofing, ductwork, and structural elements due to its durability and weather resistance.
4. Electronics: Enclosures and housings for electronic devices are often made from sheet metal to protect components and ensure proper heat dissipation.
5. Consumer Goods: Items like appliances, furniture, and decorative objects frequently use sheet metal for its aesthetic and functional properties.
Advances
Modern advancements include the integration of computer-aided design (CAD) and computer-aided manufacturing (CAM) systems, enhancing precision and reducing production times. Additionally, additive manufacturing techniques are being explored to complement traditional sheet metal fabrication, enabling more complex and lightweight designs.
In summary, sheet metal fabrication is a versatile and essential technology in various industries, driven by advancements in cutting, bending, and assembling techniques, and bolstered by innovations in digital manufacturing.
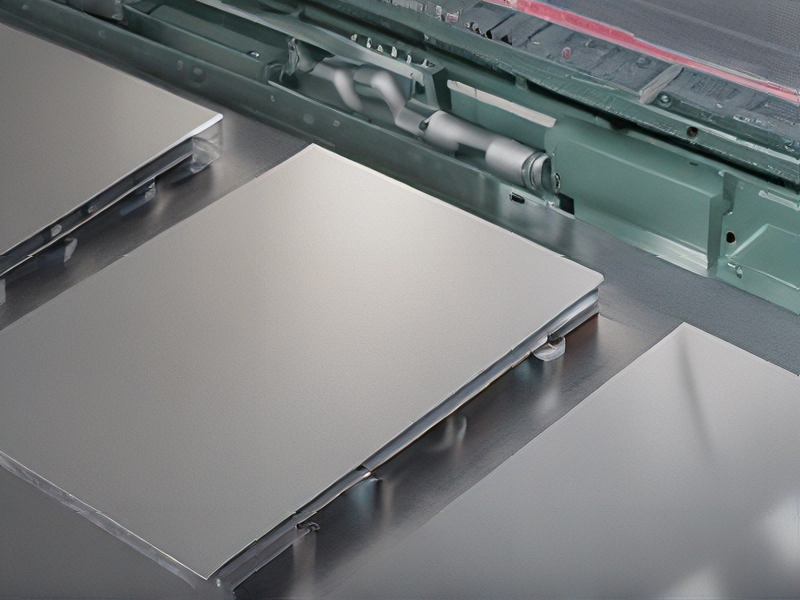
Quality Testing Methods for sheet metal fabrications and how to control quality
Quality testing for sheet metal fabrications ensures the components meet specified standards and perform reliably. Here are key methods and control practices:
Quality Testing Methods
1. Visual Inspection:
– Identifies surface defects such as scratches, dents, and corrosion.
– Quick and non-destructive.
2. Dimensional Inspection:
– Uses tools like calipers, micrometers, and gauges to check dimensions against specifications.
– Ensures parts meet precise size and tolerance requirements.
3. Material Testing:
– Conducts tensile, hardness, and impact tests to verify material properties.
– Ensures the metal meets strength and durability standards.
4. Non-Destructive Testing (NDT):
– Ultrasonic Testing: Detects internal flaws using high-frequency sound waves.
– Magnetic Particle Testing: Reveals surface and near-surface discontinuities in ferromagnetic materials.
– X-ray Inspection: Identifies internal defects using radiographic techniques.
5. Form and Fit Testing:
– Assembles parts to check compatibility and functionality.
– Verifies that components fit together as designed.
6. Surface Finish Testing:
– Measures roughness, waviness, and other surface characteristics.
– Ensures aesthetic and functional surface quality.
Quality Control Practices
1. Standard Operating Procedures (SOPs):
– Develops detailed instructions for each production step.
– Ensures consistency and compliance with standards.
2. In-Process Inspections:
– Conducts inspections at various stages of production.
– Detects and corrects defects early.
3. Statistical Process Control (SPC):
– Monitors production processes using statistical methods.
– Identifies variations and maintains process stability.
4. Corrective and Preventive Actions (CAPA):
– Investigates defects to determine root causes.
– Implements measures to prevent recurrence.
5. Documentation and Traceability:
– Maintains detailed records of inspections, tests, and material certifications.
– Ensures traceability and accountability.
By implementing these methods and practices, sheet metal fabrications maintain high quality, meet specifications, and ensure reliability and performance.
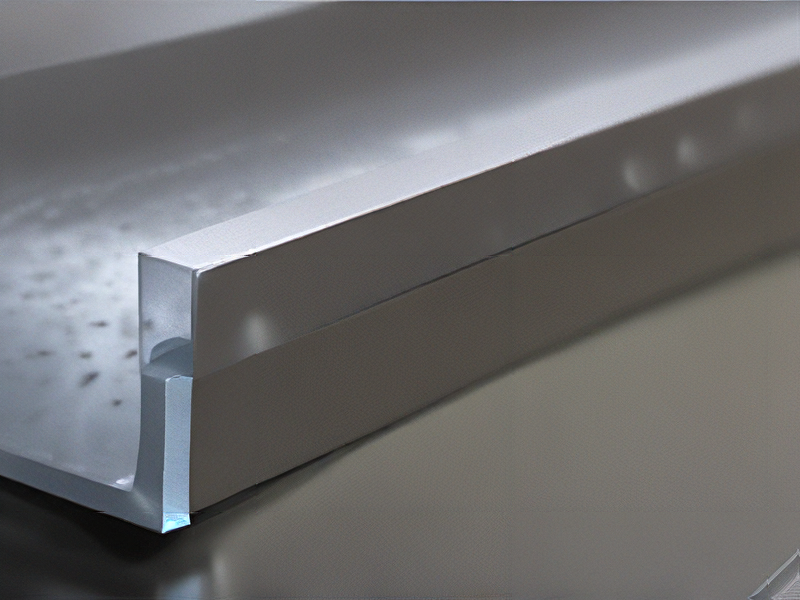
Tips for Procurement and Considerations when Purchasing from sheet metal fabrications
When procuring sheet metal fabrications, several key tips and considerations can help ensure successful purchasing:
1. Material Selection: Choose the appropriate type of metal (e.g., aluminum, steel, stainless steel) based on the application’s requirements for strength, corrosion resistance, and weight.
2. Supplier Evaluation: Assess potential suppliers based on their experience, reputation, and capability. Verify their certifications, quality control processes, and compliance with industry standards.
3. Design and Specifications: Provide detailed drawings and specifications, including dimensions, tolerances, finishes, and any special requirements. This clarity helps avoid misunderstandings and ensures the final product meets expectations.
4. Cost Considerations: While cost is important, it shouldn’t be the sole deciding factor. Evaluate the total cost of ownership, including material costs, fabrication, transportation, and potential maintenance or replacement expenses.
5. Lead Time and Delivery: Understand the supplier’s lead times and ensure they align with your project schedule. Consider the supplier’s location and logistics capabilities for timely delivery.
6. Quality Assurance: Implement stringent quality control measures. Specify the required inspections, testing procedures, and acceptance criteria. Request samples or prototypes before full-scale production.
7. Technological Capabilities: Ensure the supplier uses advanced technology and equipment for precision and efficiency. Modern fabrication techniques like CNC machining, laser cutting, and automated welding can significantly enhance product quality.
8. Scalability and Flexibility: Choose a supplier capable of scaling production up or down based on your demand. Flexibility in production scheduling and order quantities can be crucial for project success.
9. Sustainability: Consider the environmental impact of your procurement. Opt for suppliers who prioritize sustainable practices, such as recycling and waste reduction.
10. Communication and Collaboration: Maintain open lines of communication with the supplier. A collaborative approach can address potential issues promptly and foster a stronger partnership.
By focusing on these key areas, you can optimize your procurement process and ensure high-quality, cost-effective sheet metal fabrications.
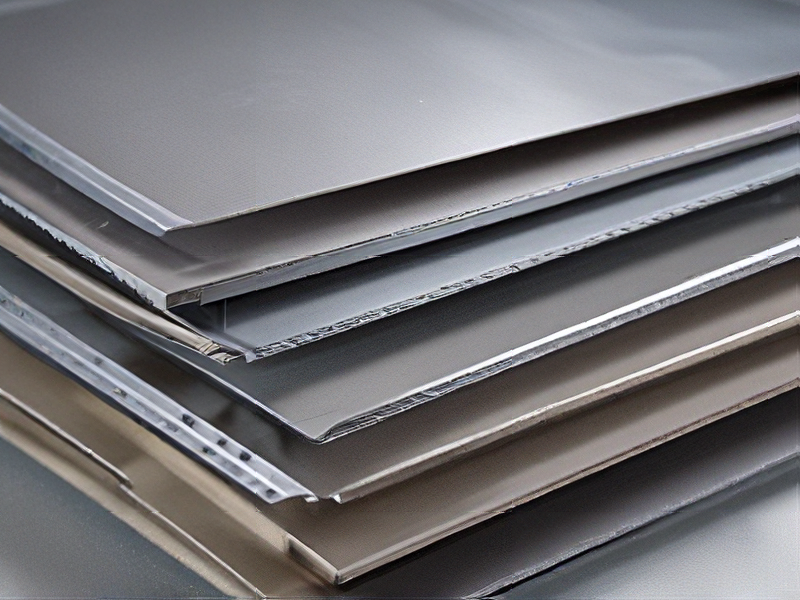
FAQs on Sourcing and Manufacturing from sheet metal fabrications in China
FAQs on Sourcing and Manufacturing Sheet Metal Fabrications in China
1. Why source sheet metal fabrications from China?
– Cost Efficiency: Lower labor and production costs.
– Advanced Technology: Access to advanced manufacturing technologies.
– Capacity: Ability to handle large-scale production efficiently.
2. What types of sheet metal fabrications can be sourced?
– Materials: Aluminum, stainless steel, carbon steel, and more.
– Processes: Cutting, bending, welding, stamping, and assembly.
3. How to ensure quality control?
– Standards: Ensure the manufacturer adheres to international quality standards (ISO, CE).
– Inspections: Conduct pre-shipment inspections and regular audits.
– Samples: Request and evaluate production samples.
4. What are the lead times for production and delivery?
– Production Time: Typically ranges from 2 to 6 weeks, depending on complexity.
– Shipping: Sea freight usually takes 20-30 days, while air freight is faster but more expensive.
5. How to select a reliable manufacturer?
– Reputation: Look for manufacturers with a strong track record and positive reviews.
– Certifications: Check for relevant certifications and compliance with industry standards.
– Communication: Ensure clear and efficient communication.
6. What are the potential challenges?
– Quality Issues: Variability in product quality.
– Cultural Differences: Navigating language and business practice differences.
– Logistics: Managing shipping, customs, and potential delays.
7. How to handle intellectual property (IP) protection?
– Agreements: Use Non-Disclosure Agreements (NDAs) and contracts to protect IP.
– Trademarks: Register trademarks and patents in China.
8. What are the payment terms?
– Common Terms: 30% deposit before production, 70% balance before shipment.
– Methods: Wire transfer (T/T), Letters of Credit (L/C).
9. Can I get custom designs made?
– Customization: Most manufacturers offer custom design services based on specifications.
10. How to handle shipping and logistics?
– Freight Forwarders: Use experienced freight forwarders for handling shipping and customs clearance.
– Incoterms: Understand terms like FOB (Free on Board) and CIF (Cost, Insurance, and Freight).
By considering these FAQs, businesses can better navigate the complexities of sourcing and manufacturing sheet metal fabrications in China.
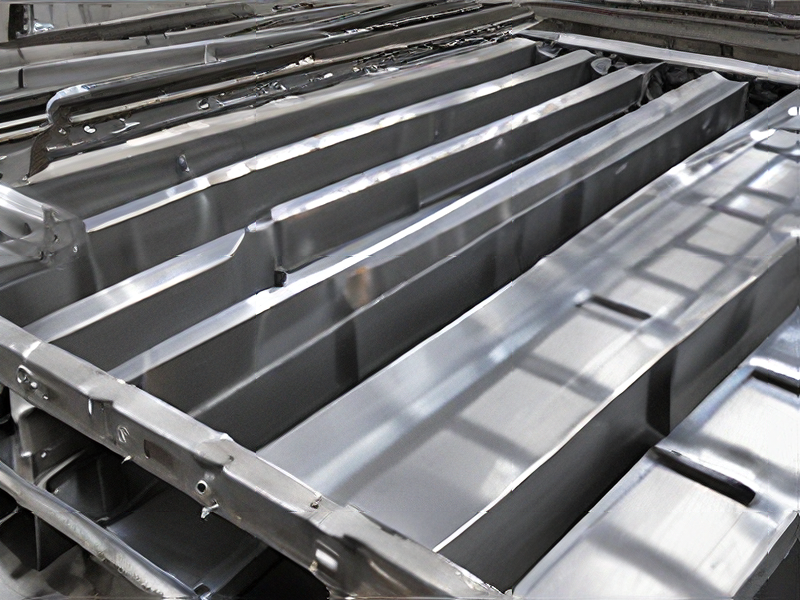