Technology and Applications of sheet metal fabricators
Sheet metal fabrication is a versatile process used in various industries to create structures and components from thin metal sheets. This technology involves several key techniques, including cutting, bending, forming, and assembling metal sheets into desired shapes and sizes.
Cutting: This can be achieved through methods such as shearing, laser cutting, and water jet cutting. Laser cutting, in particular, is favored for its precision and ability to handle complex designs with minimal material waste.
Bending: This process involves deforming the metal along a straight axis to create V-shapes, U-shapes, or channel shapes. Tools such as press brakes are commonly used for this purpose, providing high accuracy and repeatability.
Forming: Techniques like stamping and deep drawing shape the metal by applying force with a die, allowing for the creation of intricate designs and deep, hollow shapes. These processes are essential in automotive and aerospace industries where complex components are required.
Assembling: This stage involves joining metal parts through welding, riveting, or adhesive bonding. Welding, including MIG, TIG, and spot welding, is particularly prevalent due to its strength and durability.
Applications:
1. Automotive Industry: Sheet metal fabrication is used to produce car bodies, chassis, and various components, ensuring durability and lightweight structures.
2. Aerospace: Precision and strength are crucial in aerospace applications, where sheet metal is used for aircraft skins, wings, and fuselage components.
3. Construction: Metal sheets are employed in building facades, roofing, and structural elements due to their strength and aesthetic appeal.
4. Consumer Electronics: Housings and enclosures for devices like computers and appliances are often made from fabricated sheet metal.
5. Medical Devices: Precision and hygiene standards are vital in medical equipment, making sheet metal an ideal material for surgical instruments and hospital fixtures.
Overall, sheet metal fabrication is integral to modern manufacturing, offering flexibility, precision, and cost-effectiveness across diverse applications.
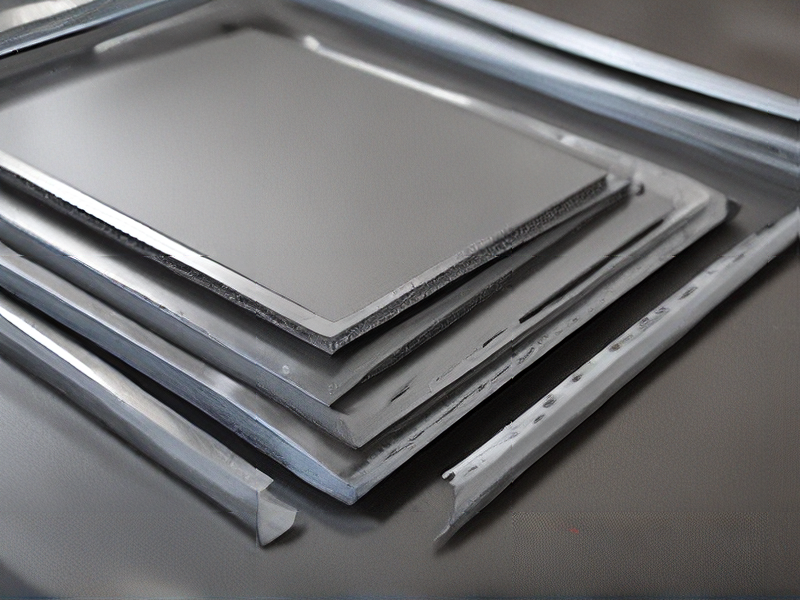
Quality Testing Methods for sheet metal fabricators and how to control quality
Quality testing for sheet metal fabricators involves several methods to ensure the final products meet specified standards and customer requirements. Here are the primary methods and controls:
1. Visual Inspection: This initial check identifies surface defects such as scratches, dents, or incorrect finishes. Inspectors examine the sheet metal for visible issues before more detailed testing.
2. Dimensional Inspection: Using calipers, micrometers, and coordinate measuring machines (CMM), this method ensures the sheet metal components adhere to specified dimensions and tolerances. It’s crucial for maintaining consistency in parts that must fit precisely in assemblies.
3. Non-Destructive Testing (NDT):
– Ultrasonic Testing: Uses high-frequency sound waves to detect internal defects such as cracks or voids.
– Radiographic Testing: Employs X-rays or gamma rays to identify internal flaws.
– Magnetic Particle Testing: Detects surface and near-surface defects in ferromagnetic materials.
4. Destructive Testing:
– Tensile Testing: Measures the material’s strength by pulling it until it breaks.
– Bend Testing: Assesses ductility and the ability to withstand deformation without cracking.
– Hardness Testing: Determines material hardness using methods like Rockwell or Vickers testing.
5. Chemical Analysis: Verifies the composition of the sheet metal, ensuring it meets the required alloy specifications.
Quality Control Measures:
1. Incoming Material Inspection: Checking raw materials against quality standards before they enter production.
2. In-Process Inspection: Regular checks during production to catch defects early. This can include first article inspections and sampling.
3. Final Inspection: Comprehensive checks of finished products before delivery to ensure they meet all specifications.
4. Process Control: Implementing standardized procedures and training to maintain consistency. Statistical process control (SPC) tools monitor production processes to detect and address variations.
5. Documentation and Traceability: Keeping detailed records of inspections, tests, and material certificates to trace issues back to their source.
By combining these testing methods and control measures, sheet metal fabricators can ensure high-quality, reliable products.
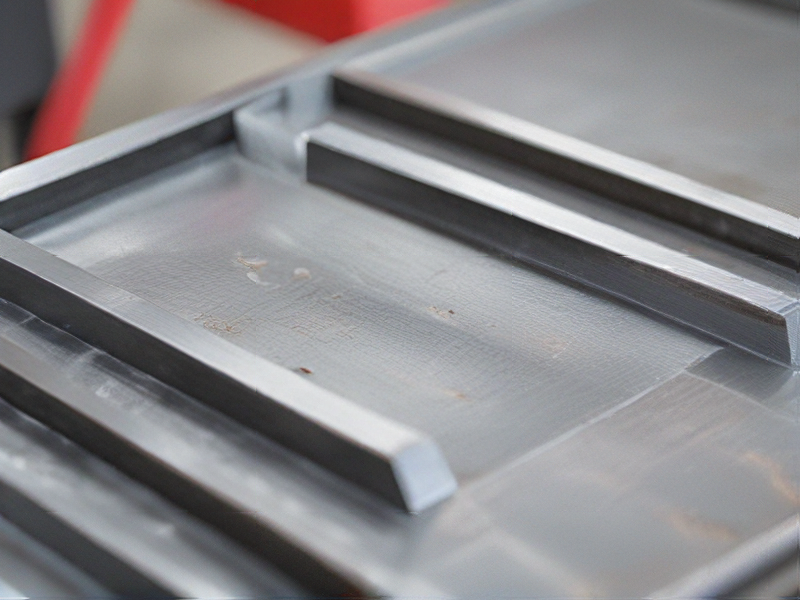
Tips for Procurement and Considerations when Purchasing from sheet metal fabricators
When procuring from sheet metal fabricators, it’s essential to follow specific tips and considerations to ensure quality, cost-effectiveness, and timely delivery. Here are key points to keep in mind:
Tips for Procurement:
1. Define Specifications Clearly:
– Detail the material type, thickness, dimensions, tolerances, and any special finishes required.
– Provide precise engineering drawings and CAD files to avoid misunderstandings.
2. Supplier Evaluation:
– Assess the fabricator’s experience, capabilities, and quality control processes.
– Verify certifications like ISO 9001, which indicate a commitment to quality.
3. Request for Quotes (RFQ):
– Obtain multiple quotes to compare pricing, lead times, and services.
– Ensure the quotes are detailed, covering all aspects of production, including setup, tooling, and delivery.
4. Prototype and Sampling:
– Request prototypes or samples to evaluate the quality and adherence to specifications.
– Use this phase to make any necessary adjustments before full-scale production.
5. Quality Assurance:
– Establish quality checkpoints and inspection protocols.
– Consider third-party inspections for critical projects.
6. Communication:
– Maintain clear and regular communication with the supplier to address any issues promptly.
– Use a single point of contact to streamline communication.
Considerations:
1. Cost Factors:
– Be aware of the total cost, including material, labor, tooling, and transportation.
– Consider the cost-benefit of domestic vs. international suppliers.
2. Lead Time and Flexibility:
– Understand the supplier’s lead times and their capacity to handle urgent orders.
– Assess their flexibility in accommodating design changes or volume fluctuations.
3. Technical Capability:
– Ensure the fabricator has the necessary machinery and technology for your specific requirements, such as laser cutting, CNC machining, or welding.
4. Sustainability and Compliance:
– Check for compliance with environmental regulations and sustainability practices.
– Evaluate their waste management and recycling processes.
5. Supply Chain Stability:
– Investigate the stability of the supplier’s supply chain to mitigate risks of material shortages or delays.
By following these tips and considerations, you can effectively manage the procurement process, ensuring high-quality, cost-effective, and timely deliveries from sheet metal fabricators.
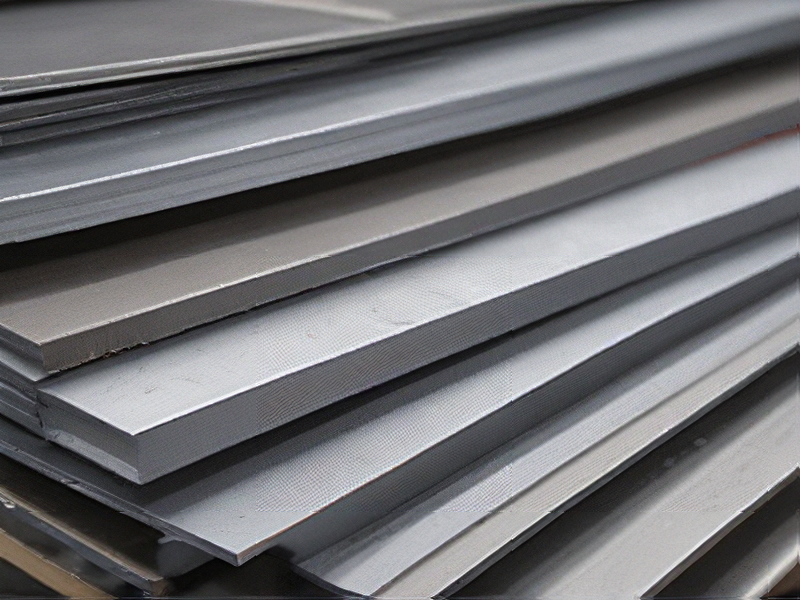
FAQs on Sourcing and Manufacturing from sheet metal fabricators in China
FAQs on Sourcing and Manufacturing from Sheet Metal Fabricators in China
#### 1. Why should I consider sourcing sheet metal fabrication from China?
China offers competitive pricing, advanced manufacturing technology, and high production capacity. Many Chinese fabricators adhere to international quality standards and offer customization options.
#### 2. How can I ensure the quality of the products?
Request samples before placing large orders, visit the factories if possible, and use third-party inspection services. Look for certifications such as ISO 9001.
#### 3. What is the typical lead time for manufacturing?
Lead times vary based on order size, complexity, and the specific fabricator. Generally, it ranges from 2 to 8 weeks. Confirm timelines with your supplier.
#### 4. How do I handle communication barriers?
Many Chinese fabricators employ English-speaking staff. Use clear, concise language, and consider using professional translation services for complex negotiations.
#### 5. What payment terms are common?
Common terms include a 30% deposit upfront with the balance paid before shipment. Some suppliers might offer more flexible terms after establishing a reliable business relationship.
#### 6. What are the shipping options and costs?
Options include air freight for small, urgent orders and sea freight for larger, less time-sensitive shipments. Costs depend on the size, weight, and destination. Incoterms like FOB (Free on Board) and CIF (Cost, Insurance, and Freight) determine who pays for shipping and when ownership transfers.
#### 7. How can I protect my intellectual property (IP)?
Use non-disclosure agreements (NDAs), register your IP in China, and work with reputable suppliers known for respecting IP rights. Legal action in China can be challenging but is an option if necessary.
#### 8. What should I consider when selecting a fabricator?
Evaluate their experience, production capabilities, quality control processes, and client feedback. Visiting the factory and seeing their operations firsthand can be very insightful.
#### 9. Are there any hidden costs I should be aware of?
Consider import duties, tariffs, VAT, and logistics costs. Clarify all potential costs with your supplier before finalizing the order.
#### 10. How do I handle disputes or issues with orders?
Clearly outline terms in your contract, including quality standards, delivery times, and penalties for non-compliance. Maintain open communication and seek mediation if needed.
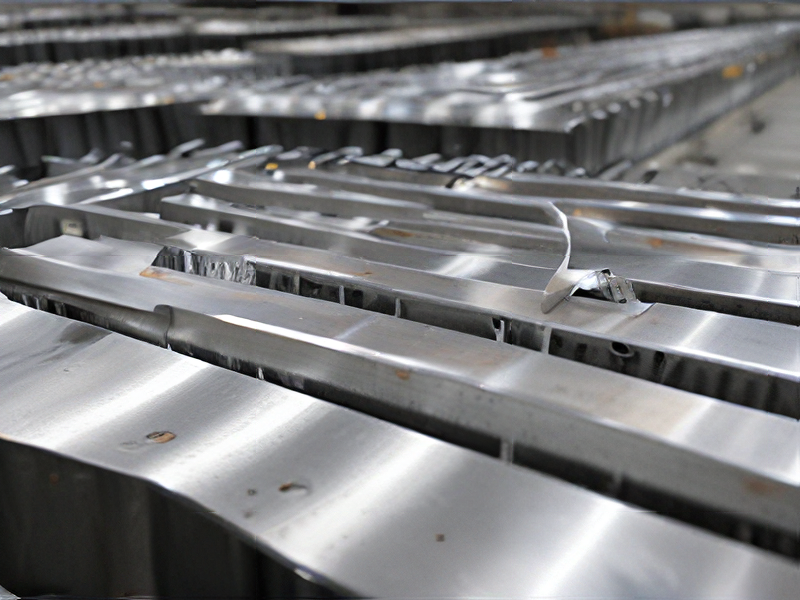