Technology and Applications of sheet metal sheet metal
Sheet metal is a versatile material widely used in various industries due to its malleability, strength, and lightweight characteristics. Technology in sheet metal fabrication has advanced significantly, enabling precise shaping and forming through methods such as laser cutting, CNC machining, stamping, and welding. These processes allow for the production of complex designs with high accuracy and repeatability.
Applications of sheet metal span numerous sectors, including automotive, aerospace, construction, and consumer goods. In the automotive industry, sheet metal is essential for manufacturing body panels, frames, and components, contributing to vehicle strength and safety. Aerospace applications rely on lightweight, high-strength sheet metals to enhance fuel efficiency and structural integrity in aircraft design.
In construction, sheet metal is used for roofing, siding, and ductwork, providing durability and weather resistance. Its aesthetic appeal also makes it a popular choice for architectural elements. Consumer goods, such as appliances and electronic housings, often utilize sheet metal for its ease of fabrication and ability to protect internal components.
Innovations in technology, including automation and robotics, have further enhanced sheet metal processing capabilities, leading to reduced costs and shorter production times. Emerging trends also focus on sustainability, with increased use of recyclable materials and energy-efficient manufacturing processes.
In summary, sheet metal technology continues to evolve, driving innovation across multiple industries while addressing modern demands for efficiency, sustainability, and design flexibility. Its wide-ranging applications underscore its significance as a fundamental material in contemporary manufacturing.
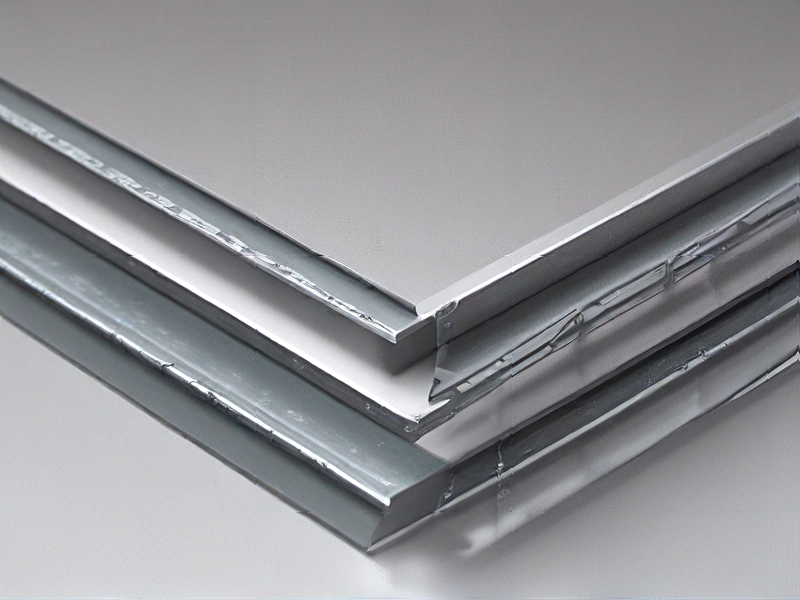
Quality Testing Methods for sheet metal sheet metal and how to control quality
Quality testing of sheet metal is crucial to ensure durability, structural integrity, and performance. Here are some common methods and strategies to control quality:
Testing Methods:
1. Visual Inspection: Conduct a thorough visual examination for surface defects such as scratches, dents, corrosion, or improper cutting. This is the first line of quality assurance.
2. Dimensional Measurement: Use calipers, micrometers, or laser measurement tools to verify the thickness, length, width, and overall dimensions against specifications. Ensuring accurate measurements is critical to fit and assembly.
3. Mechanical Testing:
– Tensile Testing: Assess the material’s yield strength, ultimate tensile strength, and elongation by pulling a specimen until it fails.
– Bend Testing: Evaluate ductility by bending a sample at a specified angle to check for cracking or deformation.
4. Non-Destructive Testing (NDT): Techniques such as ultrasonic testing, magnetic particle inspection, and dye penetrant inspections help identify subsurface flaws without damaging the materials.
5. Coating Thickness Measurement: If coatings are applied, employ methods like magnetic or eddy current testing to confirm the proper thickness and adherence of coatings.
Quality Control Strategies:
– Standard Operating Procedures (SOPs): Establish clear SOPs for all manufacturing processes to ensure consistency and reliability.
– Training: Regular training of personnel on quality standards and testing techniques is essential to maintain high quality.
– Statistical Process Control (SPC): Implement SPC to monitor and control manufacturing processes, using data analysis to detect variances and trends.
– Regular Audits: Conduct regular internal and external audits to ensure compliance with quality standards and identify areas for improvement.
By integrating these methods and strategies, manufacturers can ensure quality in sheet metal production, leading to reduced waste and enhanced customer satisfaction.
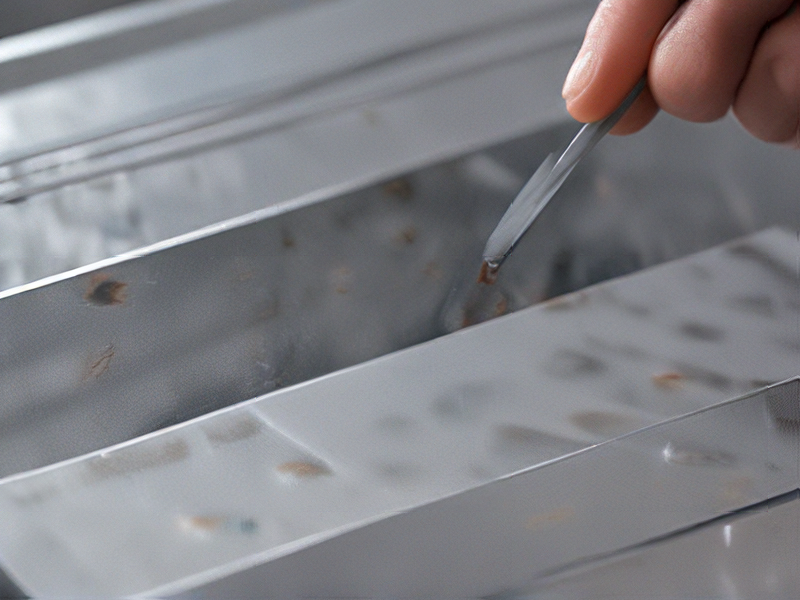
Tips for Procurement and Considerations when Purchasing from sheet metal sheet metal
When procuring sheet metal, careful consideration can enhance efficiency, cost-effectiveness, and quality. Here are essential tips and considerations:
1. Material Selection: Assess the type of sheet metal required (e.g., aluminum, stainless steel, carbon steel) based on your project’s needs, including mechanical properties, corrosion resistance, and weight.
2. Thickness & Size: Determine the appropriate thickness and dimensions essential for your design. Ensure the supplier can provide sheets that meet your specifications without excessive waste.
3. Supplier Credentials: Choose reputable suppliers with a proven track record. Check for certifications (e.g., ISO, ASTM) which ensure quality standards.
4. Cost vs. Quality: While it may be tempting to go for the cheapest option, consider the long-term value. Higher quality materials can reduce maintenance costs and improve durability.
5. Customization Options: If your project requires specific shapes or sizes, inquire about custom fabrication services and lead times.
6. Sustainability: Look for suppliers that offer recycled metals or sustainable practices, which can be beneficial for both the environment and your brand image.
7. Lead Time: Understand the supplier’s lead time and ensure it fits your project timeline. Delays in material procurement can affect overall production schedules.
8. Delivery Logistics: Consider shipping costs and logistics. Local suppliers may offer cost advantages through reduced transportation expenses.
9. After-Sales Support: Ensure the supplier provides robust customer service including handling returns, offering technical support, and addressing quality issues.
By carefully evaluating these factors, you can secure sheet metal that meets your project requirements while optimizing costs and ensuring quality.
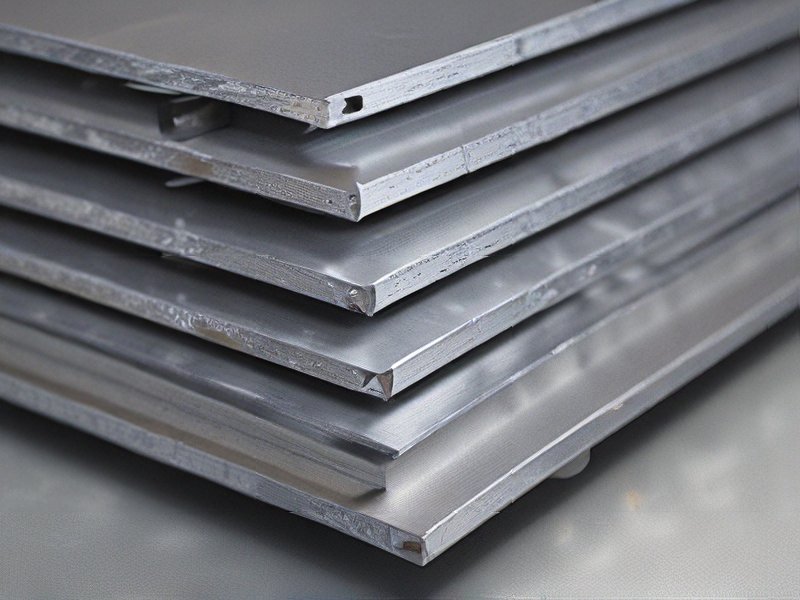
FAQs on Sourcing and Manufacturing from sheet metal sheet metal in China
FAQs on Sourcing and Manufacturing Sheet Metal in China
1. What types of sheet metal products can be manufactured in China?
China can produce a wide range of sheet metal products, including brackets, enclosures, chassis, and custom components for various industries like automotive, aerospace, electronics, and home appliances.
2. How do I find a reliable manufacturer?
Research potential suppliers through platforms like Alibaba, Global Sources, or industry trade shows. Verify their credentials, request references, and assess their past work through samples or visiting their facilities if possible.
3. What materials are commonly used in sheet metal fabrication?
Common materials include stainless steel, aluminum, carbon steel, and galvanized steel. The choice of material depends on the product’s application, durability requirements, and cost considerations.
4. What is the typical lead time for manufacturing?
Lead times can vary depending on the complexity and volume of the order. However, a typical timeframe ranges from 4 to 12 weeks, including production, quality control, and shipping.
5. How can I ensure quality control?
Establish clear quality standards and procedures. Conduct pre-production meetings, require inspections at various stages of the manufacturing process, and consider third-party quality control services.
6. What are the shipping options from China?
Shipping methods include air freight for fast delivery and sea freight for cost-effective solutions. Choose based on urgency and budget considerations.
7. Are there hidden costs I should be aware of?
Be mindful of potential hidden costs such as tariffs, customs duties, shipping insurance, and quality control inspections, which can impact your overall budget.
8. What are payment terms typically offered?
Payment terms often include a deposit upfront (usually 30%) with the balance due upon completion or before shipping. Always negotiate terms that best suit your financial situation.
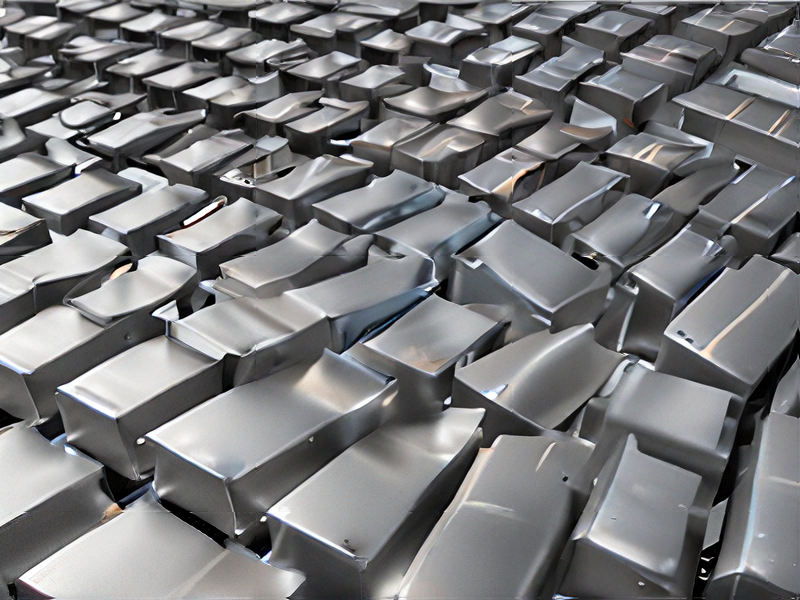