Technology and Applications of sheet metals
Sheet metal is a versatile material widely used in various industries due to its unique properties, such as strength, flexibility, and lightweight nature. It is created by transforming metal into thin, flat pieces, typically ranging from 0.2 mm to several millimeters in thickness. Common metals used include steel, aluminum, copper, and titanium.
Manufacturing Processes
The primary technologies for sheet metal fabrication include cutting, bending, and forming. Techniques such as laser cutting, water jet cutting, and CNC machining allow for precise shaping and size. Bending processes, like die bending and press brake operations, create angles and forms necessary for specific applications. Stamping and deep drawing further enhance the versatility of sheet metals.
Applications
1. Construction: Used for roofing, siding, and structural components due to its durability and resistance to corrosion.
2. Automotive: Essential for body panels, frames, and components, sheet metal contributes to vehicle strength and safety while minimizing weight.
3. Aerospace: Utilized in aircraft components to achieve high strength-to-weight ratios, crucial for performance and fuel efficiency.
4. Electronics: Fabricated into housings and enclosures for devices, providing protection and aesthetic appeal.
5. Manufacturing Equipment: Common in machinery and tools, providing structural integrity and reliability.
Future Trends
Innovations in advanced manufacturing techniques, such as additive manufacturing (3D printing) and smart sheet metal technologies (sensors embedded in metal), are enhancing the capabilities and applications of sheet metal. Sustainability practices, including the recycling of metals and reducing waste, are also critical trends within the industry.
In essence, sheet metal’s adaptability and cost-effectiveness make it an indispensable material across diverse sectors, shaping the future of various technologies and applications.
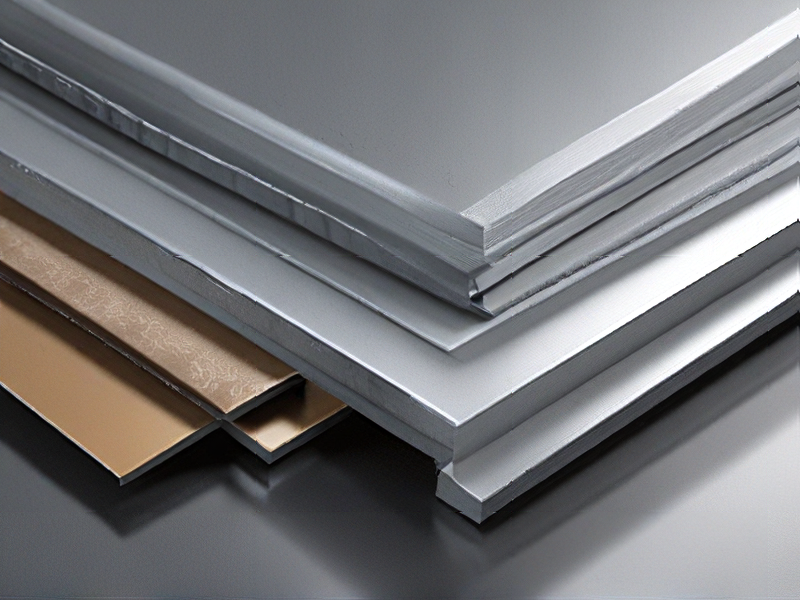
Quality Testing Methods for sheet metals and how to control quality
Quality testing of sheet metals is critical to ensure they meet industry standards and performance requirements. Here are some effective testing methods and quality control measures:
Testing Methods:
1. Visual Inspection: A preliminary assessment that identifies visible defects such as scratches, dents, or surface irregularities.
2. Dimensional Inspection: Utilizing calipers and micrometers to verify that the sheet metal meets specified dimensions and tolerances.
3. Mechanical Testing:
– Tensile Testing: Measures the metal’s strength and ductility by pulling a sample until it breaks.
– Hardness Testing: Determines resistance to deformation using methods like Rockwell or Brinell hardness tests.
4. Chemical Analysis: Verifies the composition of the metal to ensure it meets material specifications. Techniques include X-ray fluorescence (XRF) and optical emission spectroscopy (OES).
5. Non-Destructive Testing (NDT):
– Ultrasonic Testing: Uses sound waves to detect internal flaws without damaging the material.
– Magnetic Particle Inspection: Identifies surface and near-surface flaws in ferromagnetic materials.
Quality Control Measures:
1. Standardization: Implementing standardized procedures and specifications ensures consistency in production and testing.
2. Training: Regular training for staff on quality standards and testing methods enhances compliance and reduces errors.
3. Regular Audits: Conducting internal and external audits to assess the quality process adherence and improving areas of deficiency.
4. Control Plans: Developing comprehensive quality control plans that define parameters for acceptable quality levels (AQL) and corrective actions.
5. Feedback Loop: Establishing a feedback mechanism from testing results to production, allowing for continuous improvement in processes.
By integrating these testing methods and quality control strategies, manufacturers can ensure the reliability and durability of sheet metals.
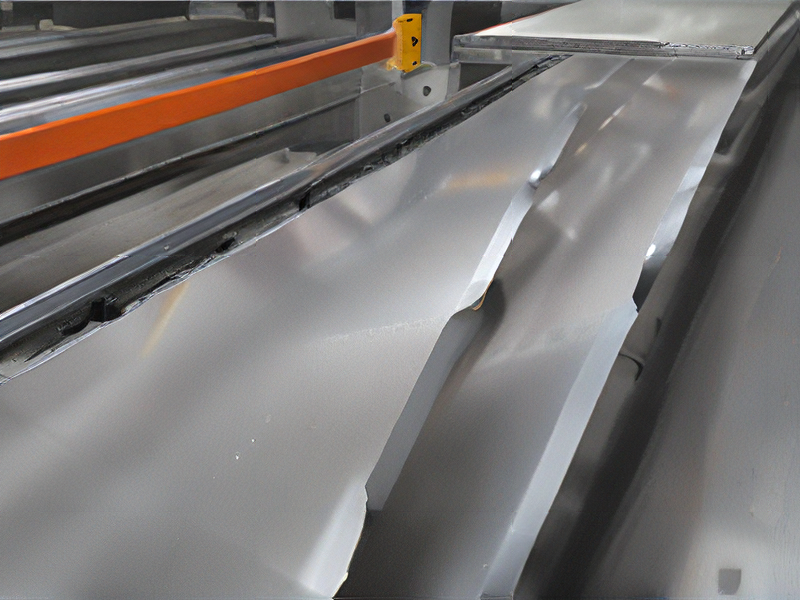
Tips for Procurement and Considerations when Purchasing from sheet metals
When procuring sheet metals, consider the following tips and considerations to ensure a successful purchase:
1. Material Specification: Understand the specific type of sheet metal you need (e.g., aluminum, steel, stainless steel, copper) based on your project requirements. Consider thickness, grade, and alloy composition.
2. Supplier Verification: Choose reputable suppliers. Check for certifications (e.g., ISO, ASTM) that ensure quality standards. Read reviews and ask for references or testimonials.
3. Quantity and Pricing: Calculate the amount of sheet metal required accurately to avoid excess waste. Compare prices from multiple suppliers, including shipping costs, but be wary of choosing suppliers solely based on cost.
4. Lead Times: Ask about lead times for production and delivery. Ensure that the supplier can meet your project’s timeline to avoid delays.
5. Custom Fabrication: If you need specific shapes or sizes, inquire if the supplier offers custom fabrication services. Verify their capabilities and additional costs.
6. Surface Treatments: Consider whether you need any surface treatments (e.g., anodizing, galvanizing) to enhance corrosion resistance or aesthetics. Confirm that the supplier can provide the necessary services.
7. Quality Assurance: Request samples or certifications to ensure the metal meets your quality requirements. Understand the supplier’s return and warranty policies.
8. Logistics: Evaluate logistics for delivery, especially if ordering large quantities. Ensure the supplier can manage transportation safely to prevent damage.
9. Sustainability: Consider eco-friendly suppliers who utilize sustainable practices, such as recycling metal.
By taking these factors into account, you can streamline your procurement process and ensure you receive quality sheet metal that meets your needs.
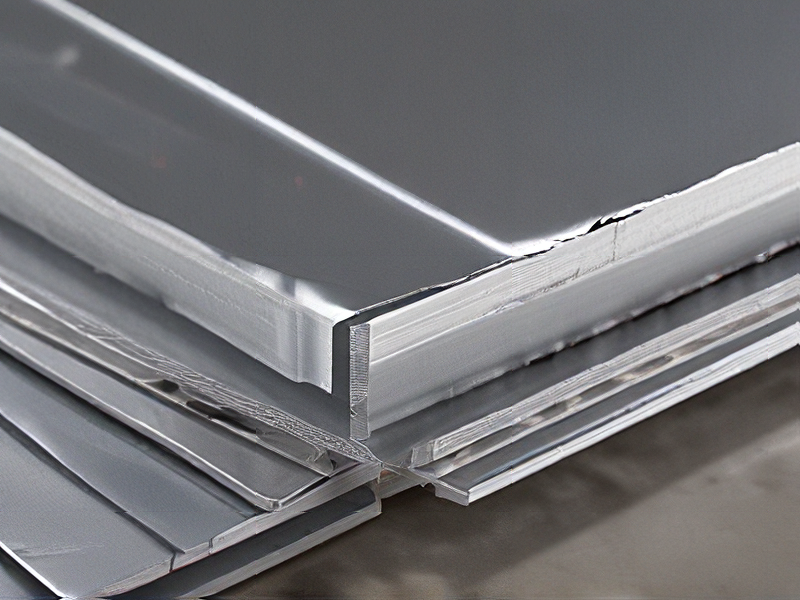
FAQs on Sourcing and Manufacturing from sheet metals in China
FAQs on Sourcing and Manufacturing Sheet Metals in China
Q1: Why source sheet metal products from China?
A1: China offers competitive pricing, an extensive supplier network, advanced manufacturing capabilities, and a wide range of materials and finishes. This makes it a popular choice for businesses looking to reduce costs while maintaining quality.
Q2: How do I find reliable suppliers?
A2: Utilize platforms like Alibaba, Made-in-China, or Global Sources to identify manufacturers. Check for certifications (ISO, CE), read customer reviews, and request samples to evaluate quality. Attending trade shows or exhibitions can also help.
Q3: What should I consider regarding quality control?
A3: Establish a quality control plan prior to production. Consider hiring third-party inspection services that conduct pre-production, in-process, and final inspections to ensure compliance with your specifications.
Q4: What are the common materials used in sheet metal fabrication?
A4: Common materials include stainless steel, aluminum, copper, and carbon steel. The choice depends on the application, desired strength, weight, and corrosion resistance.
Q5: What are the typical lead times for manufacturing?
A5: Lead times can vary widely based on the complexity of the project and supplier workload. Generally, expect 2-6 weeks for production, plus shipping time.
Q6: What are the shipping options?
A6: Shipping options include sea freight (cost-effective for large orders), air freight (faster but more expensive), and express courier services for smaller quantities. Choose based on your budget and urgency.
Q7: Are there any regulatory considerations?
A7: Be aware of import regulations, tariffs, and compliance standards specific to your industry. Ensure that your products meet local requirements before shipping.
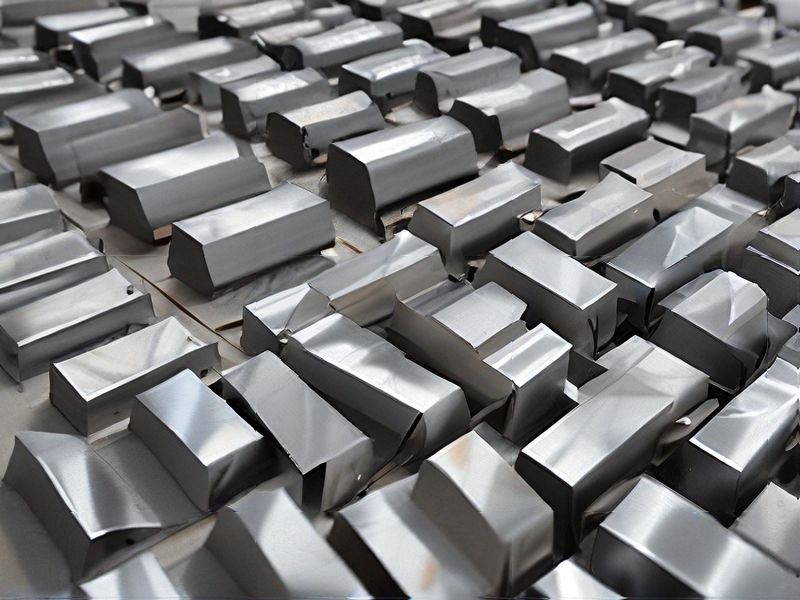