Technology and Applications of stainless steel 304 and 316
Stainless steel 304 and 316 are widely used in various industries due to their excellent corrosion resistance, durability, and versatility. Both belong to the austenitic family of stainless steels, characterized by their high chromium and nickel content.
Stainless Steel 304
Composition: Approximately 18% chromium and 8% nickel.
Applications:
– Food Processing: Used for kitchen equipment, food processing machinery, and storage tanks due to its non-reactive nature.
– Medical Equipment: Surgical instruments and medical devices benefit from its ease of sterilization and resistance to corrosion.
– Construction: Architectural paneling, railings, and trim in buildings.
– Consumer Goods: Cutlery, cookware, and appliances.
Stainless Steel 316
Composition: Contains around 16% chromium, 10% nickel, and 2-3% molybdenum.
Applications:
– Marine Environments: Boat fittings, pumps, and desalination plants utilize 316 for its superior resistance to chloride corrosion.
– Chemical Processing: Suitable for chemical storage and transportation, as well as for heat exchangers.
– Pharmaceuticals: Equipment used in drug manufacturing and processing.
– Medical Implants: Orthopedic implants and surgical instruments due to biocompatibility and resistance to body fluids.
Key Differences
– Corrosion Resistance: 316 is more resistant to chlorides and saline environments due to molybdenum, making it ideal for marine and chloride-exposed applications.
– Cost: 316 is generally more expensive due to the added molybdenum and higher nickel content.
In summary, while both 304 and 316 stainless steels offer excellent corrosion resistance and are used across numerous industries, 316 provides enhanced performance in harsher environments, justifying its higher cost for specific applications.

Quality Testing Methods for stainless steel 304 and 316 and how to control quality
Quality testing methods for stainless steel 304 and 316 ensure they meet performance standards.
Testing Methods:
* Chemical Analysis: Verifies composition (e.g., chromium, nickel) using techniques like spark emission spectroscopy or X-ray fluorescence.
* Tensile Testing: Measures strength, ductility, and hardness.
* Corrosion Resistance Testing: Evaluates susceptibility to corrosion in various environments (e.g., salt spray, acid exposure).
* Macro and Microstructure Analysis: Examines grain size, inclusions, and other structural features under a microscope.
* Surface Finish Testing: Assesses roughness and other surface characteristics.
* Weld Testing: Ensures welds meet specified strength and integrity standards.
Quality Control:
* Incoming Material Inspection: Verify raw material composition and quality.
* Process Control: Tightly control manufacturing parameters like temperature, pressure, and cooling rates.
* In-Process Inspections: Regularly monitor production stages for defects.
* Final Product Inspection: Conduct comprehensive testing on finished products.
* Documentation and Traceability: Maintain detailed records of all testing and production steps.
By implementing these methods and controls, manufacturers can ensure the high quality and reliability of stainless steel 304 and 316.
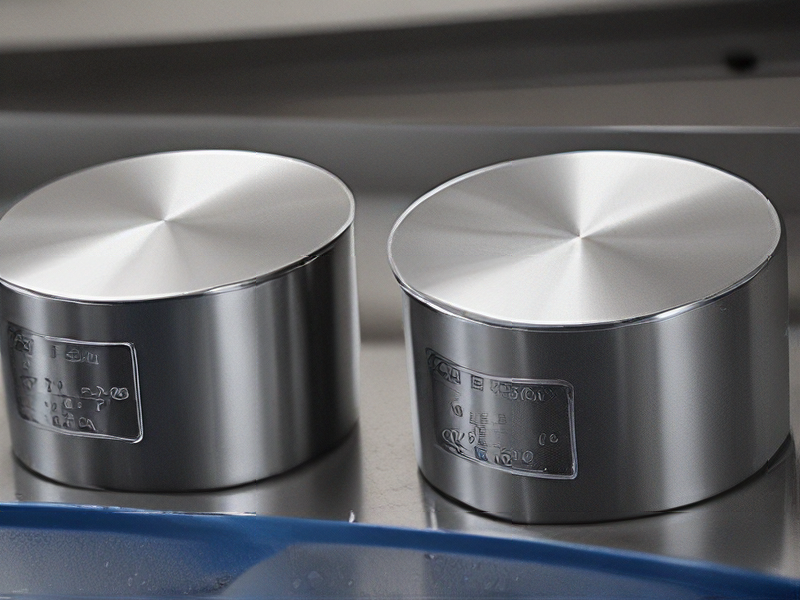
Tips for Procurement and Considerations when Purchasing from stainless steel 304 and 316
When procuring stainless steel 304 and 316, consider these tips:
1. Application:
* 304: Commonly used for its good corrosion resistance, suitability for food contact, and affordability. Ideal for kitchenware, appliances, and architectural elements.
* 316: Offers superior corrosion resistance, particularly against chloride environments. Suitable for marine applications, chemical processing, and medical equipment.
2. Form and Finish:
* Determine the required form (sheets, plates, pipes, tubing) and finish (polished, brushed, etc.).
3. Grades and Standards:
* Specify the exact grade (e.g., 304L, 316L) and relevant industry standards (ASTM, ASME, EN) to ensure quality and consistency.
4. Supplier Selection:
* Choose reputable suppliers with experience in stainless steel and excellent quality control processes.
5. Quality Inspection:
* Inspect materials upon arrival for dimensional accuracy, surface finish, and compliance with specifications.
6. Cost Considerations:
* 316 stainless steel is generally more expensive than 304 due to its superior properties.
7. Sustainability:
* Inquire about the supplier’s environmental practices and consider recycled or sustainably sourced materials.
Remember to prioritize the specific requirements of your application when making your selection.

FAQs on Sourcing and Manufacturing from stainless steel 304 and 316 in China
Sourcing and manufacturing stainless steel 304 and 316 in China can be beneficial due to the country’s vast production capacity and competitive pricing.
Sourcing:
* Established Suppliers: Numerous reputable stainless steel manufacturers and distributors operate in China. Online platforms like Alibaba and Made-in-China provide access to a wide range of suppliers.
* Certifications: Look for suppliers with certifications like ISO 9001, ensuring quality standards are met.
Manufacturing:
* Processing Capabilities: Chinese manufacturers offer comprehensive processing services, including cutting, bending, welding, and polishing.
* Customization: Many manufacturers can customize orders to specific dimensions and specifications.
Considerations:
* Quality Control: Verify supplier credentials and request samples to assess material quality.
* Communication: Clear communication is crucial. Ensure both parties understand technical requirements and delivery timelines.
* Pricing: While pricing is generally competitive, factor in potential tariffs and shipping costs.
Remember to thoroughly research potential suppliers, negotiate contracts, and establish clear communication channels for a successful experience.
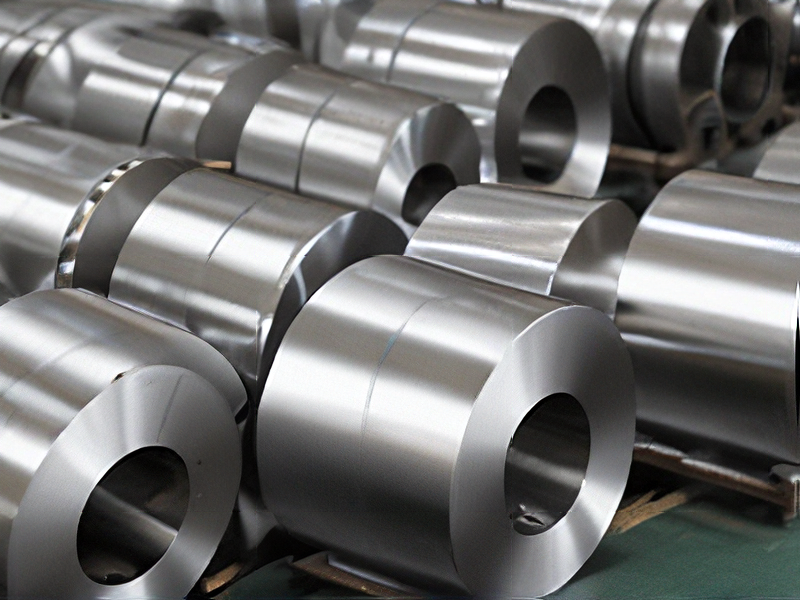