Technology and Applications of stainless steel a metal
Stainless steel is an alloy primarily composed of iron, chromium, and, in many cases, nickel. Its unique properties arise from the addition of chromium, which forms a passive oxide layer that resists corrosion and staining, making stainless steel highly durable and appealing for various applications.
Technology: The production of stainless steel involves techniques like electric arc furnace melting, casting, and rolling. Advanced metallurgical processes enable the creation of various grades tailored for specific uses, including austenitic, ferritic, and martensitic stainless steels. Innovations in manufacturing methods, such as 3D printing and laser cutting, allow for intricate designs and components in industries like aerospace and automotive.
Applications: Stainless steel is utilized across diverse sectors due to its strength, aesthetic appeal, and resistance to heat and chemicals. In the culinary world, it is favored for cookware, cutlery, and food processing equipment due to its non-reactive nature. In construction, stainless steel is employed in façade systems, handrails, and structural components for its longevity and minimal maintenance requirements. The medical field benefits from its usability in surgical instruments and implants, where sterility and corrosion resistance are critical.
Moreover, stainless steel is vital in the chemical and petrochemical industries for piping systems and storage tanks that must withstand harsh environments. Its recyclability enhances its sustainability profile, making it a preferred material in modern manufacturing. Overall, the combination of technological advancements and versatile applications solidifies stainless steel’s role as a cornerstone material in contemporary industry.
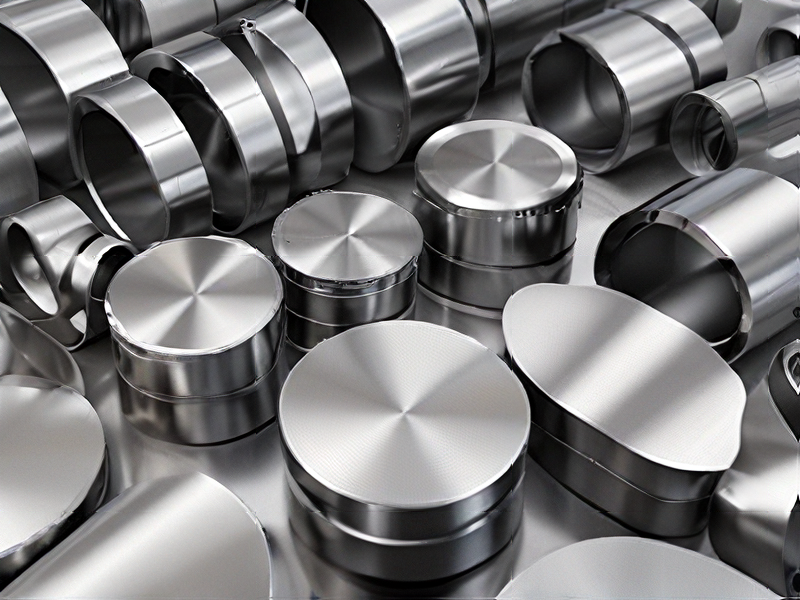
Quality Testing Methods for stainless steel a metal and how to control quality
Quality testing of stainless steel is crucial to ensure its performance and longevity in various applications. Key methods for testing include:
1. Visual Inspection: This initial assessment checks for surface defects such as cracks, pits, or discoloration. A clean, smooth surface indicates better quality.
2. Chemical Composition Analysis: Using techniques like Optical Emission Spectrometry (OES) or X-Ray Fluorescence (XRF), the alloy’s chemical makeup is verified to ensure compliance with specified standards (e.g., ASTM, ISO).
3. Mechanical Testing: Tests such as tensile strength, hardness (using Rockwell or Brinell methods), and impact tests are performed to evaluate the material’s strength and ductility.
4. Corrosion Resistance Testing: Methods like salt spray testing or immersion tests assess the stainless steel’s resistance to rust and corrosion, which is crucial for its longevity in harsh environments.
5. Non-Destructive Testing (NDT): Techniques like ultrasonic testing (UT) or eddy current testing help detect internal flaws without damaging the material.
To control quality, manufacturers should implement:
1. Standardized Processes: Adopting established quality standards and procedures throughout manufacturing processes ensures consistency.
2. Regular Audits: Conducting routine inspections and audits helps identify non-compliance and areas for improvement.
3. Training and Certification: Ensuring that employees are well-trained and certified in handling materials and equipment minimizes errors.
4. Supplier Quality Control: Establishing strict criteria for raw material suppliers ensures only high-quality raw materials are used.
5. Documentation and Traceability: Maintaining records of inspections, tests, and material origins aids in accountability and facilitates corrective actions if issues arise.
These measures can collectively enhance the quality and reliability of stainless steel products.
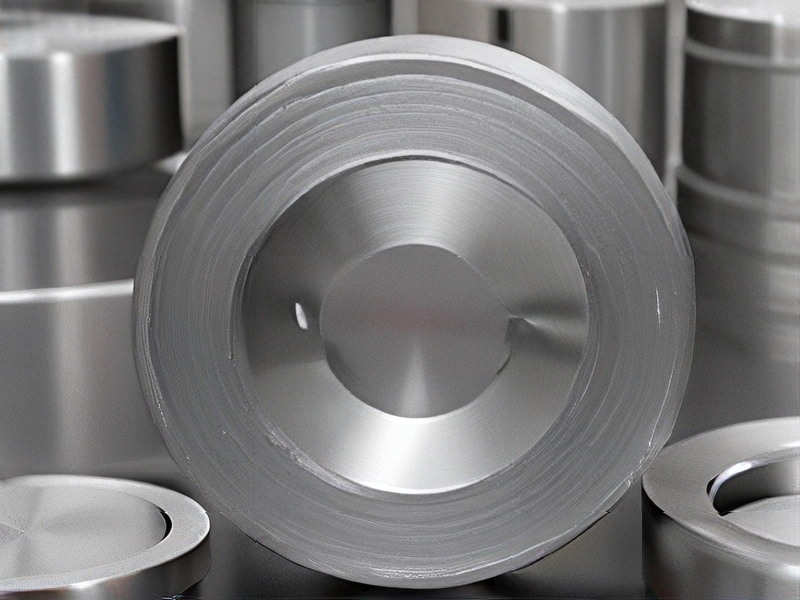
Tips for Procurement and Considerations when Purchasing from stainless steel a metal
When procuring stainless steel, several key considerations can help ensure you make an informed purchase that meets your project requirements:
1. Grade Selection: Stainless steel comes in various grades, each with distinct properties. Common grades include 304 (general use) and 316 (corrosion-resistant). Determine the environmental conditions and application to select the appropriate grade.
2. Specifications and Standards: Familiarize yourself with industry standards such as ASTM, ISO, or EN. Confirm that the supplier meets these specifications for quality assurance.
3. Supplier Reputation: Select a reputable supplier with a proven track record. Check reviews, ask for references, and consider their certification (e.g., ISO 9001).
4. Cost Analysis: While price is important, consider the total cost of ownership. Factors such as longevity, maintenance, and potential downtime due to failures can impact overall costs.
5. Material Origin: Ensure that the stainless steel is sourced ethically and complies with regulations. This might include certifications regarding recycled content or environmental impact.
6. Testing and Quality Control: Inquire about the supplier’s quality control measures. Request documentation for traceability, including certificates of compliance and material test reports.
7. Delivery and Logistics: Assess lead times and shipping options. Ensure that the supplier can meet your project schedule to avoid delays.
8. Support and Service: Consider the level of technical support the supplier offers. Having access to expertise can aid in material selection and troubleshooting.
9. Customization: If specific machining or finishing processes are needed, confirm that the supplier can accommodate these requirements.
By considering these factors, you can enhance the quality of your procurement process for stainless steel, ensuring optimal performance and value.
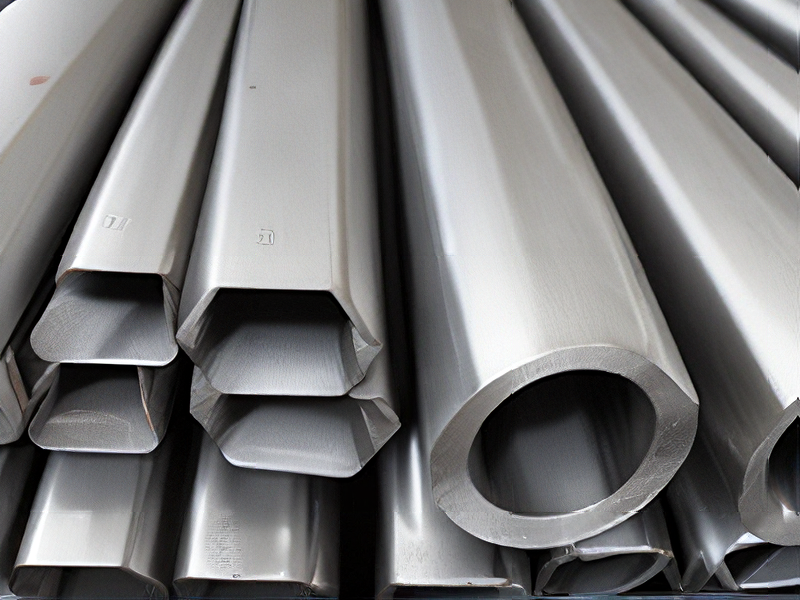
FAQs on Sourcing and Manufacturing from stainless steel a metal in China
FAQs on Sourcing and Manufacturing Stainless Steel in China
1. Why choose China for stainless steel sourcing and manufacturing?
China is a leading manufacturer with advanced production technologies, cost-effective labor, and diverse suppliers. Its vast network enables businesses to source high-quality stainless steel at competitive prices.
2. What types of stainless steel products can be sourced?
You can source a variety of products, including sheets, coils, tubes, fittings, and custom components for industries like construction, automotive, and food processing.
3. How do I ensure product quality?
To ensure quality, select reputable suppliers with ISO certifications, request samples, and conduct factory audits. Reliable third-party inspection services can also help maintain standards before shipment.
4. What are the common grades of stainless steel available?
Common grades include 304 and 316, with 304 being versatile and corrosion-resistant, while 316 offers enhanced corrosion resistance, particularly in marine environments.
5. What are the lead times for stainless steel manufacturing?
Lead times typically range from 4 to 12 weeks, depending on the complexity of the order and the supplier’s capacity. It’s essential to communicate your timelines clearly.
6. How do I handle payment and transactions?
Trustworthy suppliers often accept LC (Letter of Credit), T/T (Telegraphic Transfer), or other secure payment methods. Always negotiate payment terms upfront.
7. Are there regulatory considerations?
Ensure compliance with local regulations and international standards. This includes understanding tariffs, customs duties, and import/export licenses that may impact costs.
8. What if issues arise during sourcing?
Address any issues promptly with your supplier. Consider having a clear contract that outlines quality expectations, delivery timelines, and remedies for potential disputes.
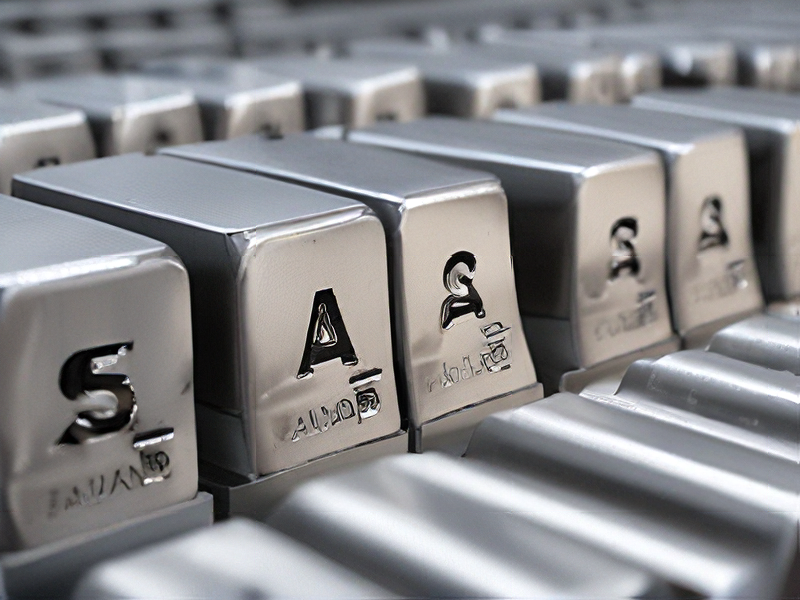