Technology and Applications of stainless steel materials
Stainless steel is a versatile alloy primarily composed of iron, chromium, and small amounts of nickel and other elements that enhance its properties. Renowned for its corrosion resistance, strength, and aesthetic appeal, stainless steel has a wide array of applications across various industries.
In the construction sector, stainless steel is used in structural components, facades, and roofing due to its durability and resistance to environmental elements. Its aesthetic properties make it a popular choice for architectural designs, adding a modern touch while requiring minimal maintenance.
In the food and beverage industry, stainless steel is the material of choice for equipment, including countertops, sinks, and storage containers. Its non-reactive surface ensures food safety and hygiene, while its ease of cleaning meets strict health regulations.
The automotive industry also employs stainless steel for exhaust systems, trim pieces, and structural components, providing lightweight yet robust solutions that enhance vehicle performance and lifespan.
Furthermore, stainless steel is pivotal in the medical field, where it is used in instruments, implants, and surgical tools due to its biocompatibility, sterilizability, and resistance to corrosion from bodily fluids.
In addition to these industries, advancements in technology have led to the development of specialized stainless steel grades tailored for specific applications, such as marine environments and high-temperature applications. Innovations in manufacturing techniques, such as additive manufacturing, are further expanding the possibilities for stainless steel use.
Overall, the unique combination of properties makes stainless steel an essential material in modern technology and applications, ensuring its continued relevance in an evolving industrial landscape.
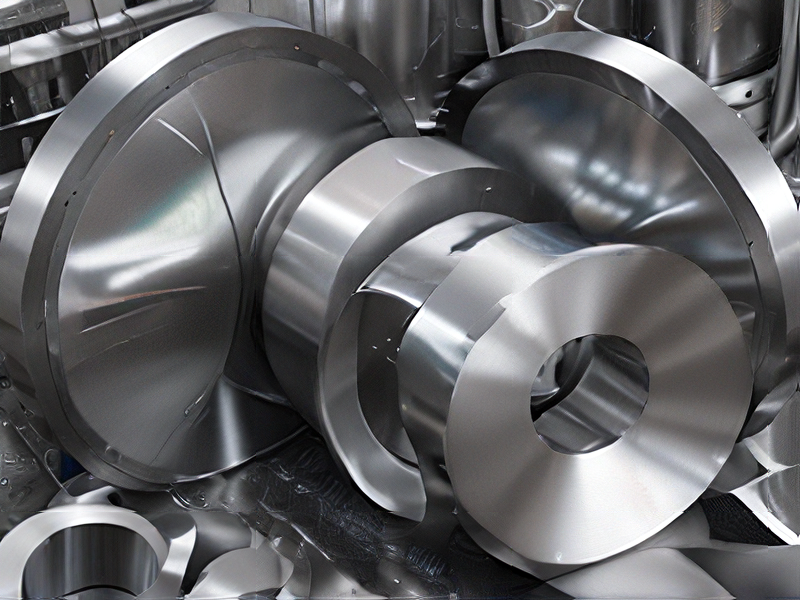
Quality Testing Methods for stainless steel materials and how to control quality
Quality testing of stainless steel materials is essential to ensure durability, corrosion resistance, and overall performance. Here are key methods and controls to ensure quality:
1. Chemical Analysis: Conduct spectrometric tests to verify the chemical composition of stainless steel, ensuring it meets specified grades (e.g., 304, 316). This helps identify elements like chromium, nickel, and molybdenum, critical for corrosion resistance.
2. Mechanical Testing: Perform tensile tests to assess strength, elongation, and reduction of area. Hardness tests, such as Rockwell and Brinell, evaluate resistance to deformation.
3. Non-Destructive Testing (NDT): Employ methods like ultrasonic testing, radiography, and magnetic particle testing to detect internal or surface defects without damaging the material. This ensures structural integrity.
4. Corrosion Testing: Utilize salt spray tests and pH immersion tests to evaluate the material’s resistance to corrosion. These tests simulate aggressive environments to predict lifespan.
5. Visual Inspection: Conduct routine visual inspections for surface defects, pitting, or welding irregularities, employing standards such as ASTM E3094 for guidelines.
6. Documentation and Traceability: Maintain records of all tests conducted and materials used. Implement a Quality Management System (QMS) compliant with ISO 9001 to ensure consistency and traceability throughout the production process.
7. Supplier Quality Assurance: Establish stringent criteria for raw material suppliers. Conduct audits and require certifications to ensure the quality of incoming materials.
8. Regular Training: Train personnel on quality control processes and testing methodologies to enhance awareness and adherence to quality standards.
By integrating these methods, manufacturers can effectively control the quality of stainless steel materials, mitigating defects and ensuring product reliability.
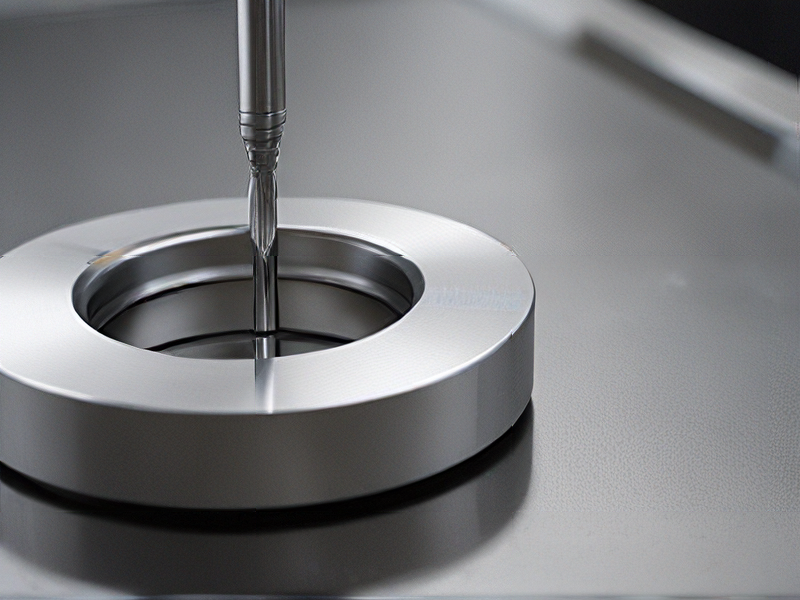
Tips for Procurement and Considerations when Purchasing from stainless steel materials
When procuring stainless steel materials, consider the following key tips and factors:
1. Material Grade: Identify the appropriate grade of stainless steel based on your application. Common grades include 304 for general use, 316 for corrosion resistance in marine environments, and 410 for high-temperature applications. Each grade offers different properties like corrosion resistance, strength, and weldability.
2. Supplier Reliability: Research potential suppliers thoroughly. Check their certifications, production capabilities, and customer reviews. A supplier with a good reputation ensures quality and timely delivery.
3. Specifications and Standards: Ensure the materials meet relevant industry standards (ASTM, ANSI). Clear specifications help to avoid issues related to quality or compliance.
4. Quantity and Pricing: Determine the required quantity, and compare pricing from multiple suppliers. Be cautious about hidden costs, such as shipping or custom duties. Bulk purchasing may offer better rates.
5. Testing and Quality Control: Request material test certificates to verify the properties of the stainless steel. Understand the supplier’s quality control processes to minimize the risk of defects.
6. Lead Times: Account for lead times in your procurement schedule. Delays in delivery can disrupt your operations, so confirm the supplier’s ability to meet timelines.
7. After-Sales Support: Evaluate the supplier’s after-sales service. Good communication and support can aid in troubleshooting and addressing any issues with the supplied materials.
8. Sustainability: Consider the environmental impact of your procurement choices. Opt for suppliers who prioritize sustainable practices and recycling of stainless steel.
By addressing these areas, you can make informed decisions and ensure the successful procurement of stainless steel materials tailored to your needs.
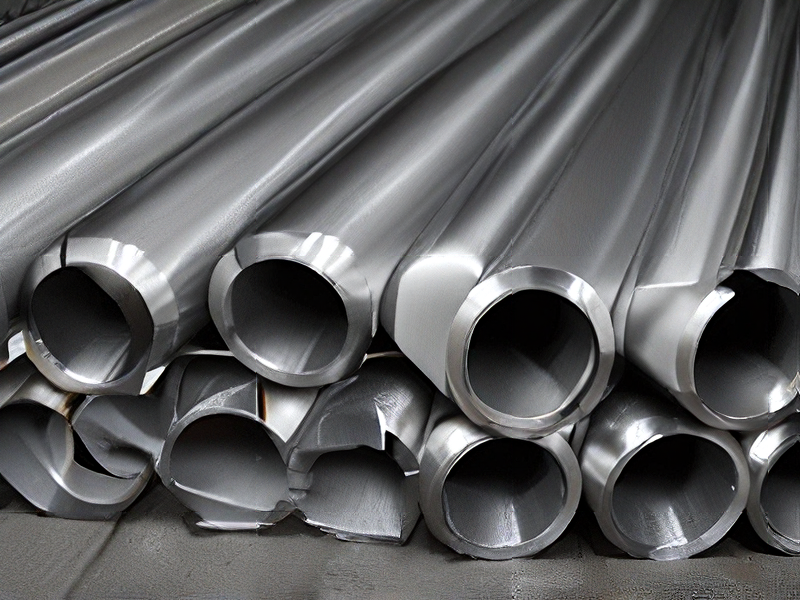
FAQs on Sourcing and Manufacturing from stainless steel materials in China
FAQs on Sourcing and Manufacturing Stainless Steel in China
1. Why source stainless steel products from China?
China is a leading manufacturer of stainless steel due to its advanced production techniques, cost-effective labor, and vast supplier base. This allows for competitive pricing and large-scale productions.
2. What types of stainless steel products can I manufacture in China?
You can source a wide range of products, including kitchenware, industrial components, medical equipment, and construction materials. Custom designs are also common.
3. How do I ensure quality in stainless steel sourcing?
Request certifications (e.g., ISO 9001) from manufacturers and conduct factory audits. Consider hiring third-party inspection services to verify product quality before shipment.
4. What are the common grades of stainless steel?
Common grades include 304, 316, and 430, each suitable for different applications. 304 offers excellent corrosion resistance, while 316 is preferred for marine applications.
5. What should I consider when selecting a supplier?
Evaluate their experience, production capacity, quality control processes, and customer reviews. It’s advisable to request samples before committing to large orders.
6. What are the shipping options for stainless steel products?
Freight options include air, sea, and rail. Sea freight is generally more cost-effective for bulk orders, while air freight offers quicker delivery for smaller shipments.
7. Are there any regulatory compliance issues?
Ensure that the products comply with international standards and regulations in your target market, such as ASTM or FDA for food-grade items.
8. What are the payment terms typically used?
Common payment methods include T/T (Telegraphic Transfer), L/C (Letter of Credit), and PayPal. Terms may vary, so clarify with the supplier before proceeding.
9. What are the lead times for stainless steel manufacturing?
Lead times vary based on complexity and order size but typically range from 4-12 weeks.
For tailored solutions, always communicate clearly with your chosen manufacturer.
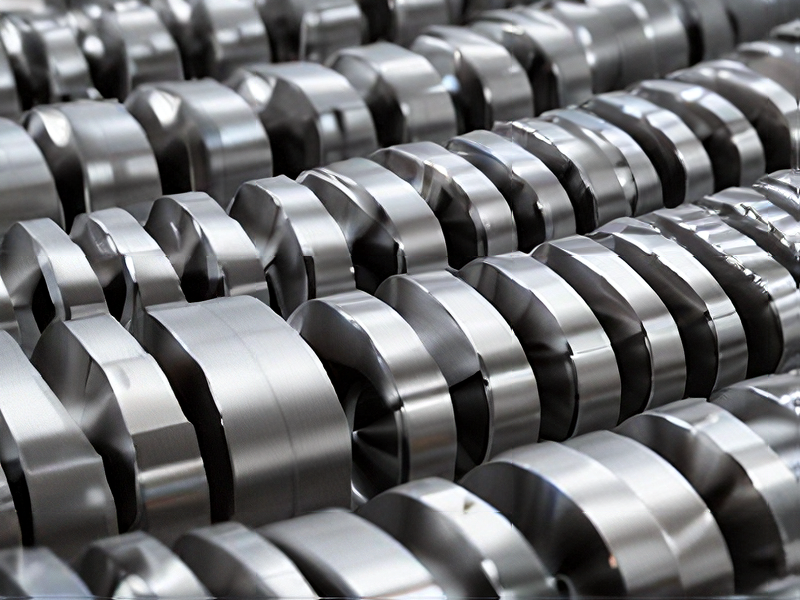