Technology and Applications of stainless steel vs galvanized steel
Stainless steel and galvanized steel are widely used in various applications due to their durability and resistance to corrosion, but they differ significantly in composition and performance.
Stainless Steel
Technology:
Stainless steel is an alloy primarily composed of iron, chromium (at least 10.5%), and other elements like nickel and molybdenum. The chromium provides a self-healing oxide layer that offers superior corrosion resistance.
Applications:
– Construction: Used in structures, cladding, and roofing due to its strength and aesthetic appeal.
– Medical Instruments: Its non-reactive nature makes it ideal for surgical tools and implants.
– Automotive and Aerospace: Used for components that require high strength and resistance to harsh environments.
– Food and Beverage Industry: Its non-corrosive and easy-to-clean nature makes it suitable for kitchen equipment and food processing plants.
Galvanized Steel
Technology:
Galvanized steel is carbon steel coated with a layer of zinc through a hot-dip process. The zinc coating protects the steel from rust by acting as a barrier and providing sacrificial protection.
Applications:
– Construction: Commonly used for roofing, wall panels, and structural beams in buildings.
– Automotive: Utilized for body panels and undercarriage parts to prevent rust.
– Agriculture: Fences, silos, and other structures exposed to the elements benefit from its protective coating.
– HVAC Systems: Ductwork and other components use galvanized steel to prevent corrosion.
Comparison
– Corrosion Resistance: Stainless steel offers superior corrosion resistance compared to galvanized steel.
– Strength and Durability: Stainless steel is generally stronger and more durable.
– Cost: Galvanized steel is usually less expensive than stainless steel.
– Maintenance: Stainless steel requires less maintenance due to its inherent resistance to corrosion, while galvanized steel may need periodic inspections and touch-ups.
In summary, the choice between stainless steel and galvanized steel depends on the specific requirements of the application, including the need for corrosion resistance, strength, and budget considerations.
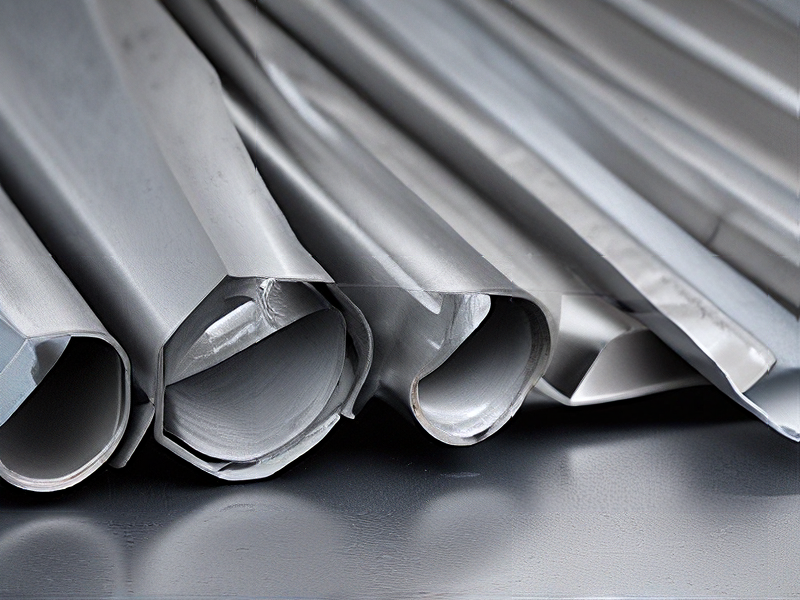
Quality Testing Methods for stainless steel vs galvanized steel and how to control quality
Quality testing methods for stainless steel and galvanized steel focus on ensuring their respective performance and durability:
1. Chemical Composition Analysis: Utilize spectroscopy techniques like X-ray fluorescence (XRF) to verify stainless steel grades (e.g., 304, 316) and galvanized coatings (zinc levels).
2. Mechanical Properties Testing: Conduct tensile tests to measure strength, yield strength, and elongation, ensuring compliance with standards (ASTM A370 for stainless steel, ASTM A123 for galvanized steel).
3. Corrosion Resistance: Perform salt spray tests (ASTM B117) to evaluate the corrosion resistance of both stainless steel and galvanized coatings over time.
4. Surface Quality: Use visual inspection, aided by magnification, to detect surface defects, scratches, or imperfections that may affect performance.
5. Adhesion Testing: Assess the bond strength between the zinc coating and the underlying steel substrate for galvanized steel using methods like ASTM D3359.
6. Dimensional Checks: Verify dimensions and tolerances of components to ensure they meet specifications.
To control quality:
– Establish Clear Specifications: Define precise quality standards and performance requirements for each material.
– Regular Testing: Implement periodic sampling and testing throughout production to catch deviations early.
– Supplier Qualification: Ensure suppliers meet quality management system standards (ISO 9001) and conduct audits as needed.
– Training and Awareness: Train personnel on quality standards, testing methods, and the importance of adherence to specifications.
– Documentation and Traceability: Maintain comprehensive records of testing results, raw material certificates, and production processes for traceability and accountability.
By implementing these methods and controls, manufacturers can consistently produce stainless steel and galvanized steel products that meet rigorous quality standards and customer expectations.
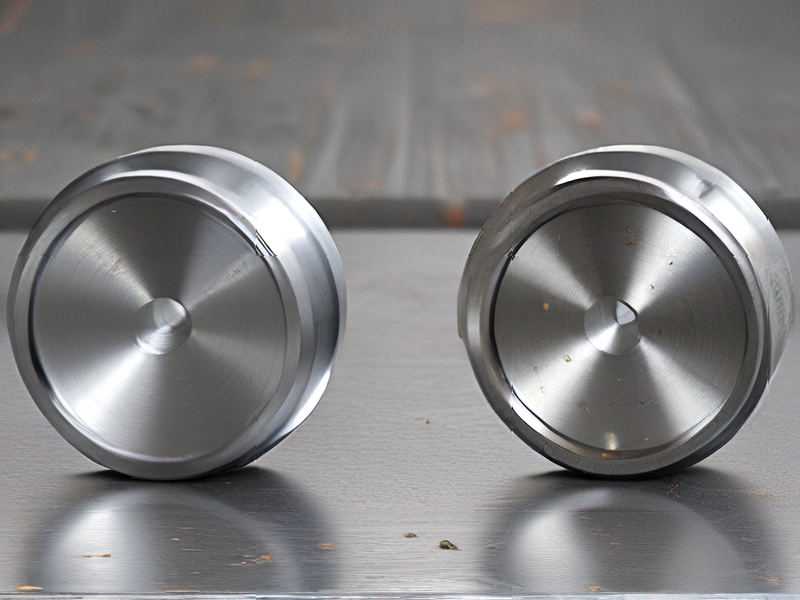
Tips for Procurement and Considerations when Purchasing from stainless steel vs galvanized steel
When deciding between stainless steel and galvanized steel for procurement, consider the following key factors:
1. Corrosion Resistance: Stainless steel offers superior corrosion resistance compared to galvanized steel, especially in harsh environments with exposure to moisture and chemicals. If your application involves outdoor or marine environments, stainless steel is often the preferred choice to avoid rust and degradation over time.
2. Cost Considerations: Galvanized steel is generally more cost-effective initially compared to stainless steel, which can be significantly more expensive. However, stainless steel’s longevity and reduced maintenance costs over its lifespan may justify the higher initial investment, depending on your budget and long-term financial planning.
3. Strength and Durability: Both stainless steel and galvanized steel are durable materials, but stainless steel tends to have higher strength and durability properties. It is often chosen for applications where strength and structural integrity are critical, such as in construction, automotive, or aerospace industries.
4. Aesthetic Appeal: Stainless steel is known for its aesthetic appeal and is often chosen for architectural applications where appearance matters. It can maintain a polished finish and does not require painting, whereas galvanized steel has a more industrial appearance and may require painting for aesthetics.
5. Environmental Impact: Consider the environmental impact of both materials. Galvanized steel requires a coating process involving zinc, which can have environmental implications. Stainless steel is fully recyclable and has a lower environmental footprint over its lifecycle.
6. Application Specifics: Finally, choose based on the specific requirements of your application. If you need a material that can withstand high temperatures, corrosive environments, or stringent hygiene standards (such as in food processing), stainless steel is typically the preferred choice.
In conclusion, while galvanized steel may be more cost-effective initially, stainless steel offers superior corrosion resistance, durability, and aesthetic appeal, making it a worthwhile investment for many applications despite the higher upfront cost. Always assess your project’s specific needs and consult with suppliers or engineers to determine the best material choice for your procurement needs.

FAQs on Sourcing and Manufacturing from stainless steel vs galvanized steel in China
When sourcing and manufacturing stainless steel versus galvanized steel in China, it’s essential to consider several key factors:
1. Material Properties and Suitability:
– Stainless Steel: Known for its corrosion resistance, durability, and aesthetic appeal. Ideal for products requiring long-term reliability in various environments, such as outdoor or marine applications.
– Galvanized Steel: Coated with zinc to prevent rusting. It offers good protection against corrosion but may not be as durable or aesthetically pleasing as stainless steel.
2. Cost Considerations:
– Stainless Steel: Generally more expensive due to its higher material cost and manufacturing requirements. However, its longevity and reduced maintenance costs can justify the initial investment.
– Galvanized Steel: Typically cheaper due to lower material costs and simpler manufacturing processes. It can be cost-effective for applications where corrosion resistance is needed but not at the level of stainless steel.
3. Manufacturing Processes:
– Stainless Steel: Requires specialized equipment and skills for fabrication due to its hardness and properties. Skilled labor is often needed, which can affect manufacturing costs.
– Galvanized Steel: Easier to fabricate and weld compared to stainless steel. Manufacturing processes are generally simpler, leading to lower production costs.
4. Environmental and Regulatory Compliance:
– Both materials have environmental considerations, especially in terms of production emissions and waste management.
– Compliance with international standards and regulations for quality and safety is crucial for exports from China, particularly in sectors like construction and automotive.
5. Supplier Capabilities and Quality Assurance:
– Choosing reputable suppliers in China is critical. Ensure they have the necessary certifications (e.g., ISO standards) and a track record of producing high-quality materials.
– Conducting factory audits and quality inspections can help mitigate risks associated with product quality and consistency.
In summary, while galvanized steel offers cost advantages and sufficient corrosion resistance for many applications, stainless steel provides superior durability and aesthetics, albeit at a higher cost. Choosing between them should be based on specific project requirements, budget constraints, and the intended lifespan and environmental conditions of the end product.
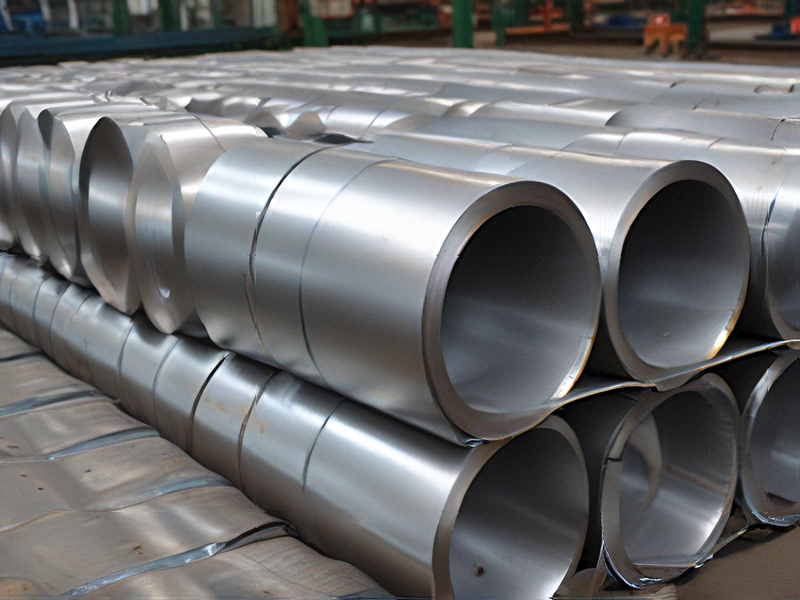