Technology and Applications of steel and stainless steel
Steel and stainless steel are vital materials in modern technology and applications due to their strength, durability, and versatility.
Steel is an alloy primarily composed of iron and carbon, with varying compositions leading to different types such as carbon steel, alloy steel, and high-strength low-alloy steel. Its applications span numerous industries, including construction (beams, rebar), automotive (frames, chassis), and manufacturing (machinery and tools). The ability to be molded into various shapes and sizes makes steel essential for infrastructure, from skyscrapers to bridges. Advanced manufacturing techniques, such as 3D printing and welding, further enhance its applications.
Stainless steel, an alloy of steel containing at least 10.5% chromium, is renowned for its corrosion resistance and aesthetic appeal. It is extensively used in environments prone to moisture and chemicals, such as in the food and beverage industry (equipment, utensils), pharmaceuticals (storage tanks, processing equipment), and medical devices (surgical instruments). Its hygienic properties make it invaluable in healthcare settings, while its ability to maintain appearance over time makes it popular in architectural applications.
Both materials are also integral in the development of renewable energy technologies, such as wind turbine structures and solar panel frames. The automotive and aerospace industries increasingly employ high-strength variants to reduce weight and enhance fuel efficiency.
Innovations in coatings and heat treatments continue to expand the boundaries of steel and stainless steel applications, making them vital to future technological advancements. As industries seek sustainability and longevity, these materials remain pivotal in evolving applications across sectors.
Quality Testing Methods for steel and stainless steel and how to control quality
Quality testing of steel and stainless steel involves several methods to ensure material integrity, performance, and safety. Key methods include:
1. Visual Inspection: This initial step identifies surface defects such as cracks, corrosion, and improper finish.
2. Non-Destructive Testing (NDT): Techniques like Ultrasonic Testing (UT), Magnetic Particle Testing (MPT), and Radiographic Testing (RT) assess internal and surface flaws without damaging the material.
3. Chemical Composition Analysis: Spectrometry or chemical analysis verifies that the alloy’s chemical composition meets specified standards for desired properties.
4. Mechanical Testing: Tests such as tensile strength, hardness (Brinell, Rockwell), and impact tests determine the material’s mechanical properties under stress.
5. Corrosion Testing: For stainless steels, accelerated corrosion tests like salt spray (fog) testing help assess resistance to corrosion under specific environmental conditions.
Quality Control Measures:
1. Standard Compliance: Adhere to international standards (e.g., ASTM, ISO) for material specifications and testing procedures.
2. Process Control: Implement control charts and statistical process control (SPC) to monitor manufacturing processes to ensure consistency and prevent defects.
3. Inspection and Documentation: Establish regular inspection schedules and maintain records of testing results, inspections, and certifications for traceability.
4. Supplier Quality Management: Assess and monitor suppliers to ensure they meet quality standards.
5. Employee Training: Invest in training for personnel on quality assurance practices and the importance of testing methods to ensure compliance and awareness.
By employing these testing methods and quality control strategies, manufacturers can ensure the reliability and durability of steel and stainless steel products.
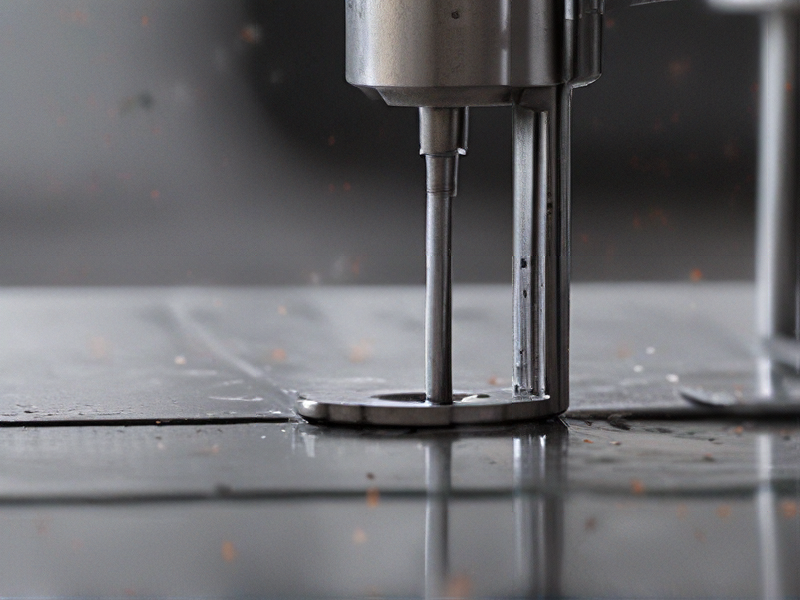
Tips for Procurement and Considerations when Purchasing from steel and stainless steel
When purchasing steel and stainless steel, consider the following tips to ensure a successful procurement process:
1. Define Requirements: Clearly outline specifications such as type (e.g., carbon steel, stainless steel grades), dimensions, tolerances, and surface finishes. This helps in accurately assessing supplier offerings.
2. Supplier Evaluation: Research and evaluate suppliers based on their reputation, reliability, and financial stability. Look for certifications (e.g., ISO 9001) that ensure quality standards.
3. Material Properties: Understand the properties of different steel types. For instance, stainless steel is more corrosion-resistant but typically more expensive than carbon steel. Choose materials that align with your application needs.
4. Quantity and Lead Time: Determine the quantity required and discuss lead times with suppliers. Ensure they can meet your schedule, as delays can affect project timelines.
5. Price vs. Quality: Obtain multiple quotes but prioritize quality over price. The cheapest option may not provide the durability or performance required.
6. Total Cost of Ownership: Consider not only the purchase price but also associated costs such as transportation, handling, and long-term maintenance.
7. Sustainability: Evaluate the sustainability practices of suppliers, especially if sourcing from companies that prioritize recycled materials or environmentally friendly processes.
8. Testing and Compliance: Ensure that the steel meets relevant standards (e.g., ASTM, EN) and, if necessary, request material test reports (MTRs) to verify quality.
9. Communication: Maintain open lines of communication with suppliers to address any issues promptly and ensure specifications are met throughout the order process.
By carefully considering these factors, you can effectively navigate the procurement process and select the right steel or stainless steel for your needs.
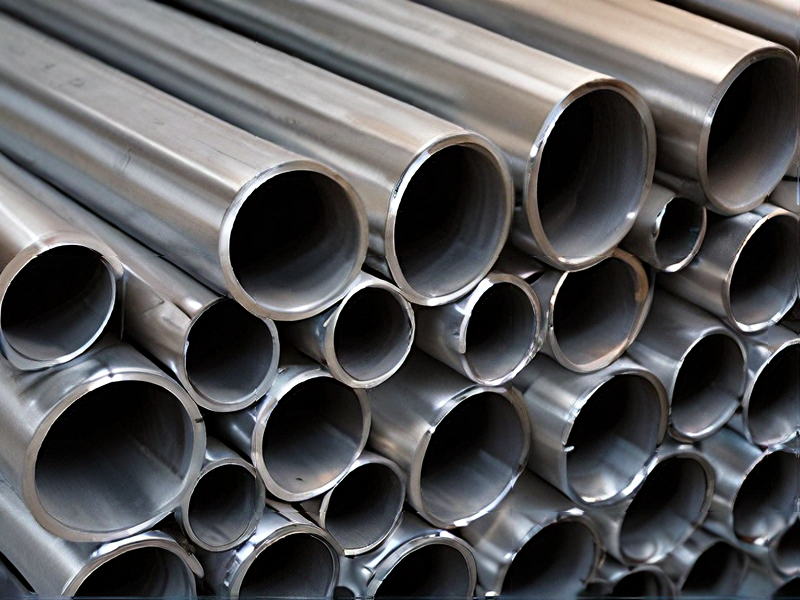
FAQs on Sourcing and Manufacturing from steel and stainless steel in China
FAQs on Sourcing and Manufacturing Steel and Stainless Steel in China
1. Why source steel or stainless steel from China?
China is one of the world’s largest producers of steel, offering competitive prices, a wide variety of products, and advanced manufacturing technologies. The country also benefits from a well-established supply chain and experienced labor force.
2. What certifications should I look for?
Ensure the supplier has relevant certifications, such as ISO 9001 for quality management, and specific product certifications like ASTM or EN for compliance with international standards.
3. How do I assess the quality of materials?
Request material samples and certifications. It’s also helpful to perform factory audits or hire third-party inspection services before finalizing orders.
4. What is the typical lead time for production?
Lead times can vary but generally range from 30 to 90 days, depending on the order size and complexity. Always confirm timelines with your supplier.
5. What are the payment terms?
Common payment terms include a deposit (usually 30%) and the balance upon shipment. Discuss payment methods such as wire transfer, L/C, or escrow through platforms such as Alibaba.
6. Are there risks involved in sourcing from China?
Risks include quality issues, communication barriers, and cultural differences. Mitigate these by researching suppliers, conducting inspections, and establishing clear contracts.
7. How do I handle shipping and customs?
Work with a reliable freight forwarder familiar with shipping from China. They will assist with logistics, documentation, and customs clearance to minimize delays.
8. What if I encounter issues post-purchase?
Communicate directly with your supplier for resolutions. Having a solid contract that outlines terms for defects or delays can help protect your interests.
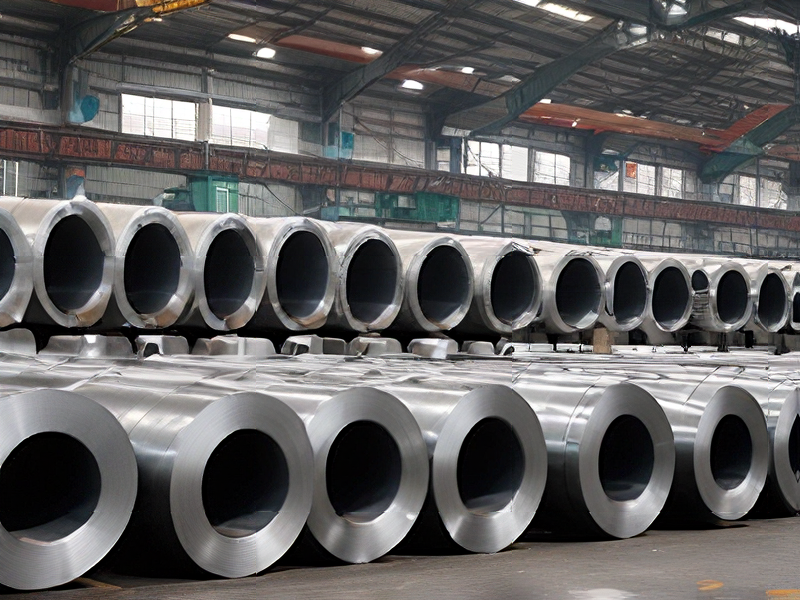