Technology and Applications of steel sheet fabrication
Steel sheet fabrication is a critical process in manufacturing, involving the transformation of flat steel sheets into desired shapes and structures through various techniques. This technology is essential across numerous industries, including automotive, construction, aerospace, and consumer goods.
Techniques:
1. Cutting: Techniques like laser cutting, plasma cutting, and waterjet cutting are employed to slice sheets into specific dimensions with high precision.
2. Bending: Using press brakes, steel sheets are bent into angles or complex shapes. This process is vital for creating components like brackets and enclosures.
3. Welding: Sheets are fused together using methods like MIG, TIG, and spot welding, forming robust structures.
4. Stamping: This involves pressing sheets into molds to create intricate shapes, commonly used in automotive and appliance industries.
5. Rolling: Sheets are passed through rollers to achieve a uniform thickness, ensuring consistency and strength.
Applications:
1. Automotive Industry: Fabricated steel sheets are used to make body panels, chassis, and other structural components, offering durability and crash resistance.
2. Construction: Steel sheets are integral to building frameworks, roofing, and cladding due to their strength and versatility.
3. Aerospace: Lightweight yet strong steel sheets are fabricated into aircraft components, balancing performance with safety.
4. Consumer Goods: Products like appliances, electronics, and furniture often incorporate fabricated steel for its robustness and aesthetic appeal.
Advancements:
Recent advancements in automation and computer-aided design (CAD) have revolutionized steel sheet fabrication. CNC machines ensure high precision and repeatability, while CAD software allows for complex designs to be executed efficiently. Additionally, developments in material science have led to high-strength, lightweight steel alloys, expanding the range of applications.
In conclusion, steel sheet fabrication is a versatile and evolving technology critical to modern manufacturing, offering a wide array of applications across various industries.

Quality Testing Methods for steel sheet fabrication and how to control quality
Quality Testing Methods for Steel Sheet Fabrication
1. Visual Inspection:
– Purpose: Detects surface defects such as cracks, scratches, and dents.
– Method: Inspected visually or with magnifying tools.
2. Dimensional Inspection:
– Purpose: Ensures adherence to specified dimensions.
– Method: Uses calipers, micrometers, and gauges.
3. Ultrasonic Testing (UT):
– Purpose: Detects internal defects and measures thickness.
– Method: Uses high-frequency sound waves.
4. Magnetic Particle Testing (MPT):
– Purpose: Identifies surface and near-surface discontinuities.
– Method: Applies magnetic field and iron particles to reveal defects.
5. Radiographic Testing (RT):
– Purpose: Finds internal defects using X-rays or gamma rays.
– Method: Captures images on film or digital detectors.
6. Tensile Testing:
– Purpose: Measures material strength and ductility.
– Method: Applies tensile force until failure.
7. Hardness Testing:
– Purpose: Assesses material hardness.
– Method: Uses Rockwell, Brinell, or Vickers hardness testers.
Quality Control Measures
1. Standard Operating Procedures (SOPs):
– Implementation: Document and standardize fabrication processes.
– Purpose: Ensures consistency and compliance with specifications.
2. In-Process Inspections:
– Implementation: Regular checks during production.
– Purpose: Identifies defects early and reduces rework.
3. Training and Certification:
– Implementation: Regular training for workers and inspectors.
– Purpose: Enhances skills and knowledge, ensuring high-quality output.
4. Statistical Process Control (SPC):
– Implementation: Monitors production processes using control charts.
– Purpose: Detects variations and trends, allowing for corrective actions.
5. Corrective and Preventive Actions (CAPA):
– Implementation: System for addressing non-conformities and preventing recurrence.
– Purpose: Continually improves quality by learning from issues.
6. Documentation and Reporting:
– Implementation: Maintain records of inspections, tests, and process parameters.
– Purpose: Provides traceability and accountability.
By integrating these testing methods and quality control measures, manufacturers can ensure the production of high-quality steel sheets.
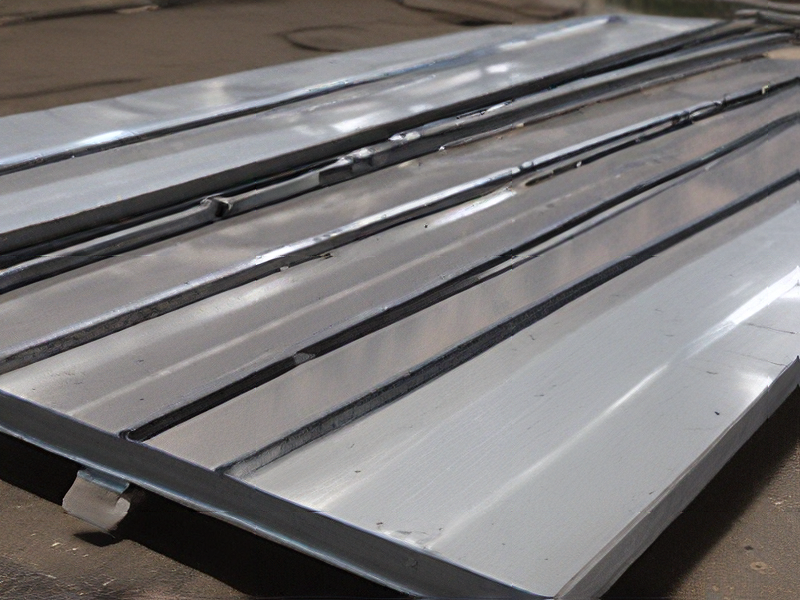
Tips for Procurement and Considerations when Purchasing from steel sheet fabrication
When procuring steel sheet fabrication services, several key considerations and best practices can ensure a successful purchase. Here are some tips to guide you:
1. Understand Your Needs: Clearly define the specifications and requirements of the steel sheets, including thickness, grade, dimensions, and any specific treatments or finishes needed. Detailed requirements help in obtaining accurate quotes and ensuring the supplier can meet your expectations.
2. Supplier Evaluation: Research and evaluate potential suppliers based on their experience, reputation, and capabilities. Look for companies with a proven track record in steel sheet fabrication and those who can provide references or case studies demonstrating their work quality.
3. Quality Standards: Ensure that the supplier adheres to relevant industry standards and certifications, such as ISO 9001 for quality management systems. High-quality standards are crucial for ensuring the durability and performance of the fabricated steel sheets.
4. Capacity and Lead Time: Assess the supplier’s production capacity and lead times to ensure they can meet your project deadlines. Understanding their workflow and capacity will help you plan accordingly and avoid delays.
5. Cost Considerations: Obtain detailed quotes from multiple suppliers to compare costs. Pay attention to what is included in the price, such as material costs, labor, finishing, and delivery. Avoid making decisions based solely on the lowest price; consider the overall value and quality.
6. Technical Support and Collaboration: Choose a supplier that offers strong technical support and is willing to collaborate on design and production processes. Effective communication can help address any issues promptly and improve the final product quality.
7. Sustainability: Consider the supplier’s commitment to sustainability practices. Suppliers who use eco-friendly materials and processes can contribute to your company’s sustainability goals.
8. Contract and Terms: Clearly outline the terms and conditions in the contract, including delivery schedules, payment terms, and penalties for non-compliance. A well-drafted contract helps prevent misunderstandings and protects both parties’ interests.
By following these tips, you can make informed decisions and establish a reliable supply chain for your steel sheet fabrication needs.
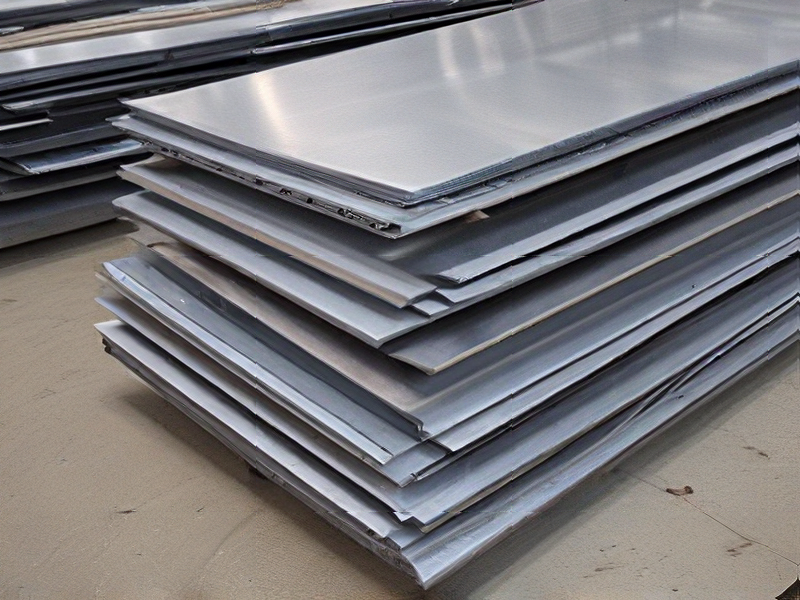
FAQs on Sourcing and Manufacturing from steel sheet fabrication in China
FAQs on Sourcing and Manufacturing from Steel Sheet Fabrication in China
1. Why should I consider sourcing steel sheet fabrication from China?
China offers competitive pricing, a wide range of suppliers, and advanced manufacturing capabilities. This can result in cost savings, high-quality products, and scalability for various projects.
2. How do I find reliable steel sheet fabrication suppliers in China?
Use platforms like Alibaba, Made-in-China, and Global Sources. Verify suppliers through certifications (ISO, CE), factory audits, and third-party inspections.
3. What are the common types of steel sheet fabrication processes available in China?
Chinese manufacturers offer processes like cutting (laser, plasma, waterjet), bending, welding, stamping, and finishing (painting, powder coating, galvanizing).
4. What should I look for in a supplier’s production capabilities?
Ensure they have modern equipment, skilled labor, quality control systems, and the ability to handle your project’s volume and complexity.
5. How can I ensure the quality of the products?
Request samples, conduct factory audits, and use third-party inspection services. Establish clear quality standards and require compliance with international standards.
6. What are the lead times for steel sheet fabrication in China?
Lead times vary based on project complexity and order size but typically range from 2 to 8 weeks. Communicate deadlines clearly with your supplier.
7. How are logistics and shipping handled?
Suppliers usually handle shipping via FOB (Free on Board) terms. Work with experienced freight forwarders and customs brokers to streamline the process.
8. What are the payment terms and methods?
Common payment terms include 30% deposit upfront and 70% before shipment. Payments are typically made via bank transfer (T/T) or letters of credit (L/C).
9. Are there any risks involved?
Risks include quality issues, communication barriers, and potential delays. Mitigate these by thorough supplier vetting, clear contracts, and regular communication.
10. Can I visit the factory?
Yes, visiting the factory can provide insights into their operations, capabilities, and quality control processes. Arrange visits through direct contact or third-party agencies.
11. What are the legal considerations?
Ensure compliance with import/export regulations, intellectual property protection, and have clear contracts detailing terms, conditions, and dispute resolution mechanisms.
12. How can I manage communication effectively?
Use clear, concise communication, preferably in English, and consider hiring local agents or translators to bridge any language gaps. Regular updates and video calls can also enhance clarity and trust.
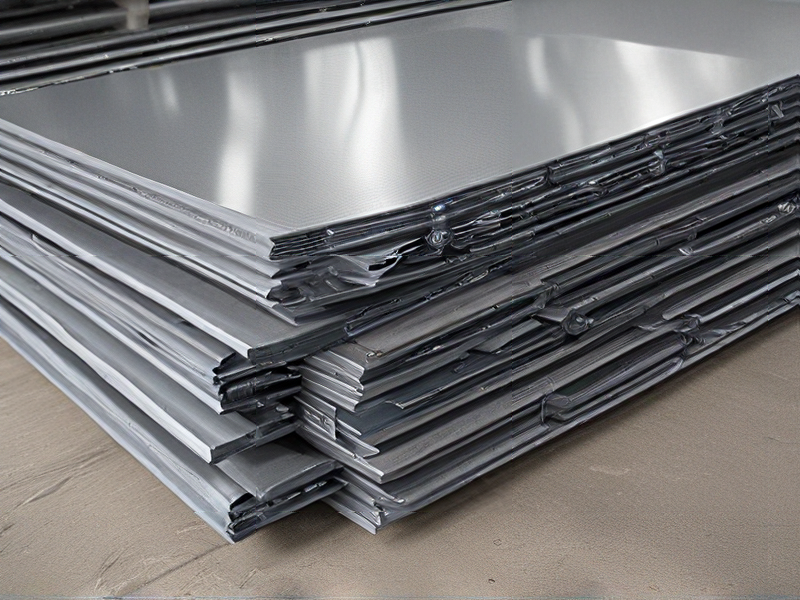