Technology and Applications of tooling steel
Tool steel is a type of carbon and alloy steel that is well-suited to be made into tools due to its hardness, resistance to abrasion, ability to hold a cutting edge, and stability in heat treatment. The key technologies and applications of tool steel include:
1. Composition and Types: Tool steels are classified based on their composition and properties. The main categories are:
– Water-hardening (W-series): Low cost and high hardness but low heat resistance.
– Cold-work (O-series, A-series, D-series): Suitable for low-temperature applications such as cutting, punching, and shearing.
– Hot-work (H-series): Can withstand high temperatures and is used in forging, die-casting, and extrusion processes.
– High-speed (M-series, T-series): Maintains hardness at high temperatures, ideal for cutting tools like drills and end mills.
– Shock-resisting (S-series): Designed to absorb shock loads, used in tools like chisels and hammers.
2. Manufacturing and Heat Treatment: The production of tool steel involves precise alloying and controlled manufacturing processes. Heat treatment is critical, involving annealing, quenching, and tempering to achieve the desired mechanical properties.
3. Applications:
– Cutting and Machining: Used to manufacture cutting tools like drills, saw blades, and milling cutters. High-speed tool steels (HSS) are particularly notable for their application in machining processes due to their ability to retain hardness at elevated temperatures.
– Forming and Shaping: Employed in the creation of dies and molds for stamping, forging, and die-casting, where durability and resistance to deformation are crucial.
– Impact Tools: Used for tools subjected to shock loading such as hammers, chisels, and punches, leveraging the toughness of shock-resisting tool steels.
– Plastic Molding: Used in injection molding and extrusion dies for plastics, requiring smooth finishes and resistance to wear.
In summary, tool steel is integral to various industrial applications due to its unique properties and the ability to be tailored through composition and heat treatment. Its use spans from high-precision cutting tools to robust forming and impact tools, playing a crucial role in manufacturing and production technologies.
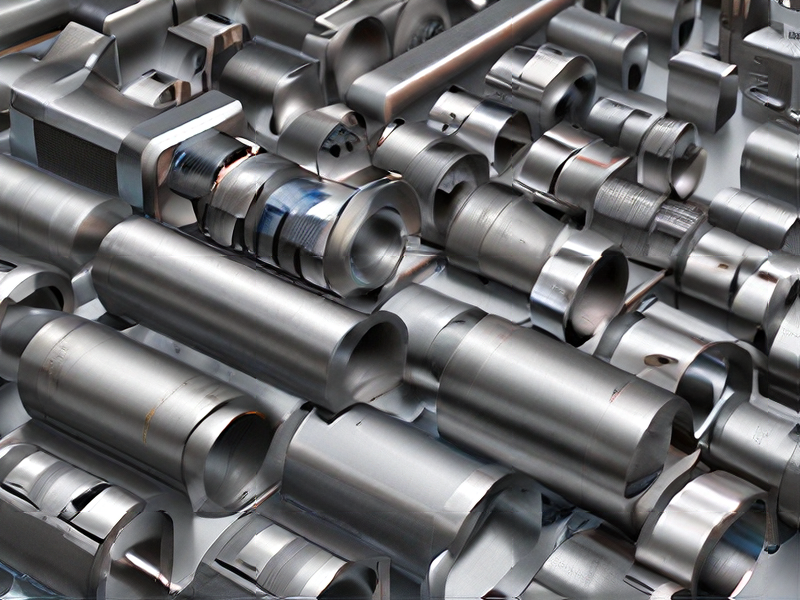
Quality Testing Methods for tooling steel and how to control quality
Quality testing methods for tooling steel typically involve a combination of mechanical and metallurgical tests to ensure its suitability for various industrial applications. Here are key methods commonly used:
1. Hardness Testing: Measures the resistance of tooling steel to indentation, often using Rockwell or Brinell scales. Higher hardness indicates better wear resistance and durability.
2. Tensile Testing: Evaluates the strength and ductility of the steel under tension. This test helps determine the maximum load a material can withstand before breaking.
3. Impact Testing: Assesses the toughness and resistance to brittle fracture by subjecting samples to sudden impact. Charpy and Izod tests are common methods used.
4. Microstructure Examination: Involves metallographic analysis to study the grain size, distribution of phases, and any defects present. This helps ensure the steel’s internal integrity.
5. Chemical Analysis: Determines the composition of the steel, verifying that it meets specified standards for elements like carbon, chromium, and vanadium, which influence its mechanical properties.
6. Dimensional Inspection: Ensures tooling steel components meet precise dimensional requirements using tools like calipers, micrometers, and CMM (Coordinate Measuring Machines).
To control quality effectively:
– Establish Clear Specifications: Define precise quality standards and requirements for tooling steel based on its intended application.
– Implement Regular Testing: Conduct routine quality checks at various stages of production to identify deviations early.
– Utilize Statistical Process Control (SPC): Monitor production processes using statistical techniques to ensure consistency and predictability.
– Train Personnel: Provide training to employees involved in manufacturing and quality control to enhance their understanding of quality standards and testing methods.
– Continuous Improvement: Foster a culture of continuous improvement to address any quality issues promptly and optimize manufacturing processes.
By integrating these methods and controls, manufacturers can ensure that tooling steel meets the required performance criteria and reliability for demanding industrial applications.
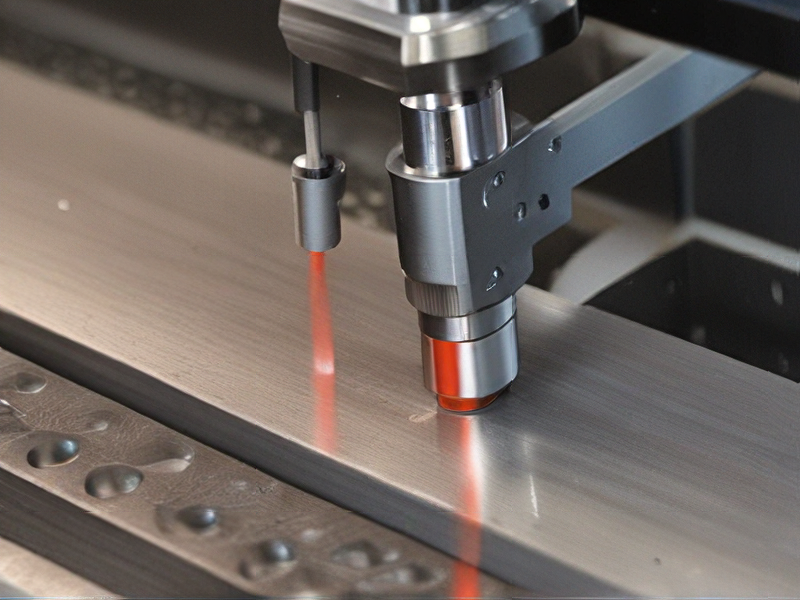
Tips for Procurement and Considerations when Purchasing from tooling steel
Purchasing tooling steel requires careful consideration beyond just price.
Key factors include:
* Steel Type: Different tooling steels have unique properties like hardness, wear resistance, and toughness. Match the steel to your specific application’s demands.
* Grade and Composition: Within each steel type, various grades exist with differing chemical compositions. Understanding the nuances of each grade is crucial for optimal performance.
* Heat Treatment: Tooling steel often requires specific heat treatments for desired hardness and properties. Ensure the supplier offers appropriate heat treatment options.
* Form and Finish: Tooling steel comes in various forms (bar, plate, wire) and finishes (ground, polished). Select the form and finish that best suits your machining and application needs.
* Supplier Reliability: Choose a reputable supplier with experience in tooling steel. They can provide technical expertise, quality assurance, and timely delivery.
* Cost vs. Value: While cost is important, prioritize the steel’s performance and durability to ensure tool longevity and minimize overall expenses.
Remember, investing in high-quality tooling steel can significantly impact your tooling life, productivity, and final product quality.

FAQs on Sourcing and Manufacturing from tooling steel in China
FAQs on Sourcing and Manufacturing Tooling Steel in China
1. Why source tooling steel from China?
China offers competitive pricing, a wide range of steel grades, and advanced manufacturing capabilities, making it a popular choice for tooling steel sourcing.
2. What types of tooling steel are available?
China produces various types of tooling steel, including high-speed steel (HSS), cold work tool steel, hot work tool steel, and plastic mold steel.
3. How do I ensure the quality of tooling steel from China?
Ensure quality by selecting reputable suppliers, requesting material certifications, and conducting third-party inspections and tests to verify the steel’s properties.
4. What certifications should I look for?
Look for certifications such as ISO 9001 for quality management, ISO 14001 for environmental management, and specific industry standards like ASTM, DIN, or JIS.
5. How do I find reliable suppliers?
Utilize online directories, trade shows, and industry networks. Verify suppliers through customer reviews, past performance, and third-party audits.
6. What is the typical lead time for tooling steel?
Lead times can vary but generally range from 30 to 60 days, depending on the steel grade, order size, and customization requirements.
7. What are the common payment terms?
Common payment terms include 30% advance payment with the balance paid before shipment or via a letter of credit.
8. How are logistics and shipping handled?
Most suppliers offer FOB (Free On Board) terms, where the buyer is responsible for shipping. Consider partnering with a logistics company to manage shipping and customs clearance.
9. Are there any trade regulations to be aware of?
Stay updated on trade tariffs, import duties, and compliance with international trade agreements to avoid unexpected costs.
10. What are the common challenges in sourcing from China?
Challenges include language barriers, time zone differences, and ensuring consistent quality. Mitigate these by maintaining clear communication, regular visits, and establishing strong relationships with suppliers.
These FAQs provide a foundational understanding for sourcing and manufacturing tooling steel in China, helping ensure a smooth and efficient process.
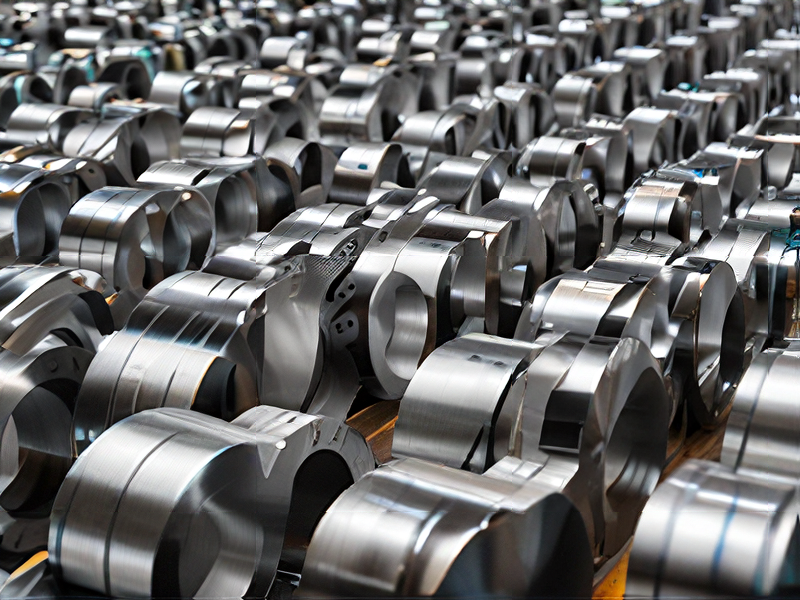