Technology and Applications of types of cnc machining
CNC (Computer Numerical Control) machining is a technology that uses computerized systems to control machine tools for manufacturing processes. It is used for creating precision parts and components in various industries, including automotive, aerospace, and electronics. The key types of CNC machining include:
1. CNC Milling:
– Technology: Involves rotary cutters to remove material from a workpiece, controlled by computer programming.
– Applications: Used for producing complex parts with various shapes and features, such as slots, holes, and threads.
2. CNC Turning:
– Technology: Involves rotating the workpiece while a single-point cutting tool shapes it.
– Applications: Ideal for creating cylindrical parts, such as shafts, bolts, and nuts.
3. CNC Grinding:
– Technology: Uses a rotating abrasive wheel to remove material and achieve a high surface finish.
– Applications: Essential for precision finishing and manufacturing of hardened parts.
4. CNC Laser Cutting:
– Technology: Uses a high-powered laser beam to cut materials with extreme precision.
– Applications: Commonly used for cutting sheet metal, plastics, and other non-metallic materials.
5. CNC Electrical Discharge Machining (EDM):
– Technology: Uses electrical discharges (sparks) to erode material from a workpiece.
– Applications: Suitable for machining hard metals and complex shapes, such as molds and dies.
6. CNC Plasma Cutting:
– Technology: Utilizes a high-velocity jet of ionized gas (plasma) to cut through conductive materials.
– Applications: Widely used in metal fabrication for cutting thick metal plates.
Each type of CNC machining offers unique advantages in terms of precision, efficiency, and the ability to create complex geometries. The integration of CNC technology enhances production capabilities, reduces human error, and ensures consistent quality across various manufacturing sectors.
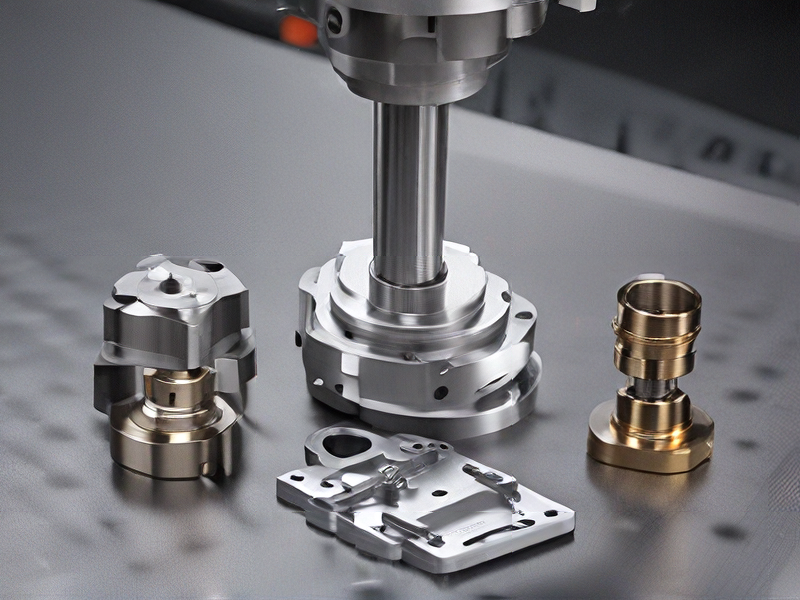
Quality Testing Methods for types of cnc machining and how to control quality
Quality testing methods for CNC machining are crucial to ensure precision, durability, and adherence to specifications. Here are common methods and controls:
1. Visual Inspection: This involves checking parts for surface defects, dimensional inaccuracies, and overall appearance. It is often the first step in quality control.
2. Dimensional Inspection: Using tools like calipers, micrometers, and coordinate measuring machines (CMM), this method checks the part’s dimensions against design specifications. CMMs are particularly useful for complex geometries.
3. Surface Finish Testing: This tests the smoothness of a part’s surface using devices like profilometers. It’s crucial for parts requiring high precision and smooth finishes.
4. Hardness Testing: This method, using tools like Rockwell or Vickers hardness testers, checks the material’s hardness to ensure it meets specified standards.
5. Tensile and Compression Testing: These tests evaluate the material’s strength by applying forces until the part deforms or breaks. They ensure the part can withstand operational stresses.
6. Non-Destructive Testing (NDT): Methods like ultrasonic testing, radiography, and dye penetrant inspection check for internal defects without damaging the part. NDT is essential for high-stress components.
Quality Control Methods:
1. Statistical Process Control (SPC): This involves using statistical methods to monitor and control the machining process, ensuring consistent product quality. Control charts and capability analysis are common SPC tools.
2. ISO Standards: Adhering to ISO 9001 or AS9100 ensures a systematic approach to quality management, including documentation, process control, and continuous improvement.
3. Tool and Machine Calibration: Regular calibration of CNC machines and tools ensures they operate within specified tolerances, reducing errors and variability.
4. In-Process Monitoring: Using sensors and feedback systems to monitor parameters like tool wear, temperature, and vibration during machining helps maintain quality and prevent defects.
5. Operator Training: Skilled operators can detect potential issues early, ensuring high-quality output. Regular training on new techniques and technologies is essential.
Implementing these methods ensures high-quality CNC machined parts, meeting both industry standards and customer requirements.
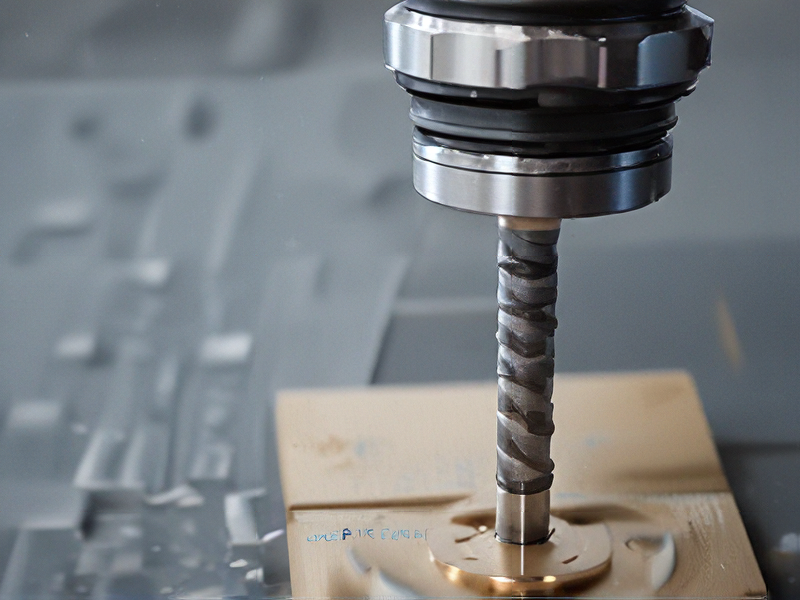
Tips for Procurement and Considerations when Purchasing from types of cnc machining
When procuring CNC machining services, consider the following tips and key considerations to ensure quality and cost-effectiveness:
1. Supplier Evaluation:
– Reputation and Experience: Choose suppliers with a solid track record and extensive experience in CNC machining.
– Certifications: Verify ISO certifications and quality management systems to ensure adherence to industry standards.
2. Capabilities and Technology:
– Machine Types: Understand the types of CNC machines (e.g., lathes, mills, routers) the supplier uses and ensure they match your requirements.
– Technology and Innovation: Opt for suppliers using the latest technology, such as multi-axis machines and automation, for precision and efficiency.
3. Material Expertise:
– Ensure the supplier has experience with the specific materials you need (e.g., metals, plastics) and can advise on material suitability and availability.
4. Quality Assurance:
– Inspection Processes: Check if the supplier has robust inspection processes, including CMM (Coordinate Measuring Machine) verification and in-process checks.
– Tolerance Capabilities: Confirm their ability to achieve the required tolerances and surface finishes for your parts.
5. Cost and Lead Time:
– Quotes and Pricing: Obtain detailed quotes, considering setup costs, unit prices, and potential for bulk discounts.
– Lead Times: Assess the supplier’s capacity to meet your delivery schedules and their flexibility to handle urgent orders.
6. Communication and Support:
– Technical Support: Ensure the supplier offers strong technical support and open lines of communication for project updates and problem-solving.
– Customer Service: Evaluate their responsiveness and willingness to collaborate on design improvements and cost-saving opportunities.
7. Logistics and Location:
– Geographical Proximity: Consider suppliers close to your location to reduce shipping costs and lead times.
– Supply Chain Reliability: Check their logistics capabilities and ability to manage inventory and supply chain disruptions.
By focusing on these areas, you can select a CNC machining supplier that aligns with your quality, budget, and timeline requirements.
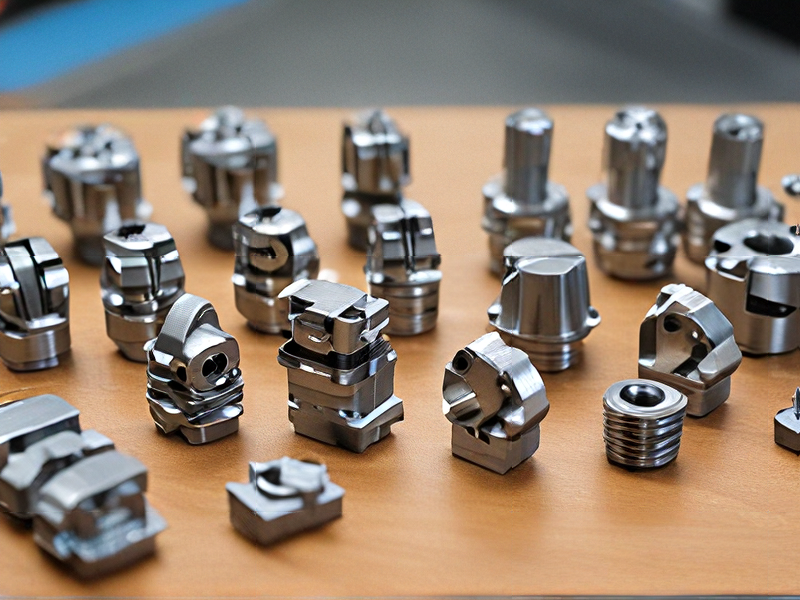
FAQs on Sourcing and Manufacturing from types of cnc machining in China
FAQs on Sourcing and Manufacturing CNC Machining in China
#### What are the types of CNC machining available in China?
China offers a wide range of CNC machining services, including milling, turning, drilling, grinding, and multi-axis machining. These services are capable of producing parts from various materials such as metals, plastics, and composites.
#### Why source CNC machining from China?
China is a leading destination for CNC machining due to its cost-effective manufacturing, advanced technology, and skilled labor. The country has a vast network of suppliers capable of producing high-quality components at competitive prices.
#### How to find reliable CNC machining suppliers in China?
To find reliable suppliers, use online platforms like Alibaba, Made-in-China, and Global Sources. Verify suppliers by checking their certifications (ISO, RoHS), customer reviews, and conducting factory audits. It’s also beneficial to work with sourcing agents who have local knowledge.
#### What should I consider when choosing a CNC machining supplier?
Consider the supplier’s experience, equipment, quality control processes, production capacity, and ability to handle your specific material and design requirements. Communication and responsiveness are also key factors.
#### What are the common materials used in CNC machining in China?
Common materials include aluminum, stainless steel, brass, titanium, and various plastics like ABS, PEEK, and polycarbonate. The choice of material depends on the application, required properties, and budget.
#### How does the quality control process work?
Quality control typically involves initial material inspection, in-process checks, and final product inspection. Many suppliers use Coordinate Measuring Machines (CMM) and other advanced inspection tools to ensure precision and compliance with specifications.
#### What is the typical lead time for CNC machined parts?
Lead times can vary depending on the complexity and quantity of parts. Generally, it ranges from 2 to 6 weeks. It’s essential to confirm lead times with the supplier to meet your project deadlines.
#### How do shipping and logistics work for CNC machined parts from China?
Shipping can be done via air or sea freight. Air freight is faster but more expensive, while sea freight is cost-effective for larger shipments. Ensure your supplier handles proper packaging to prevent damage during transit.
#### Are there any import duties or tariffs to consider?
Import duties and tariffs depend on your country’s regulations. It’s crucial to be aware of these costs and factor them into your overall budget. Consulting with a customs broker can help navigate these complexities.
By addressing these FAQs, you can better navigate the process of sourcing and manufacturing CNC machined parts from China, ensuring quality, cost-efficiency, and timely delivery.
