Technology and Applications of water machining
Water machining, often referred to as water jet machining (WJM), is a cutting technology that utilizes high-pressure water to cut materials. This process can be enhanced with the addition of abrasive materials, resulting in abrasive water jet cutting (AWJ), which enables the machining of a wider variety of materials, including metals, composites, and stone.
Technology:
Water jet machines consist of a high-pressure pump that can generate pressures up to 90,000 psi. The water is propelled through a focusing nozzle, creating a thin, high-velocity stream that can effectively cut through materials. In abrasive water jet systems, garnet or other abrasives are mixed with the water to increase the cutting capability. The technology is computer numerically controlled (CNC), allowing for complex shapes and precise cuts.
Applications:
1. Manufacturing: Used for cutting intricate designs in metals, plastics, and wood without thermal distortion.
2. Aerospace: Effective for trimming composite materials and fabricating lightweight components.
3. Automotive: Ideal for cutting gaskets, seals, and other components where precision is critical.
4. Construction: Useful for stone and concrete cutting, including architectural features and flooring.
5. Medical: Employed in producing medical devices and surgical instruments due to its precision and minimal heat-affected zones.
Advantages:
– Versatility: Capable of cutting a wide range of materials without altering their properties.
– Environmental Impact: Water jet machining generates minimal waste and does not produce harmful gases or fumes.
– Precision: Offers high-quality cuts with tight tolerances, reducing the need for secondary processing.
In conclusion, water machining is a versatile, environmentally-friendly technology with broad applications across various industries, making it a preferred choice for precision cutting tasks.
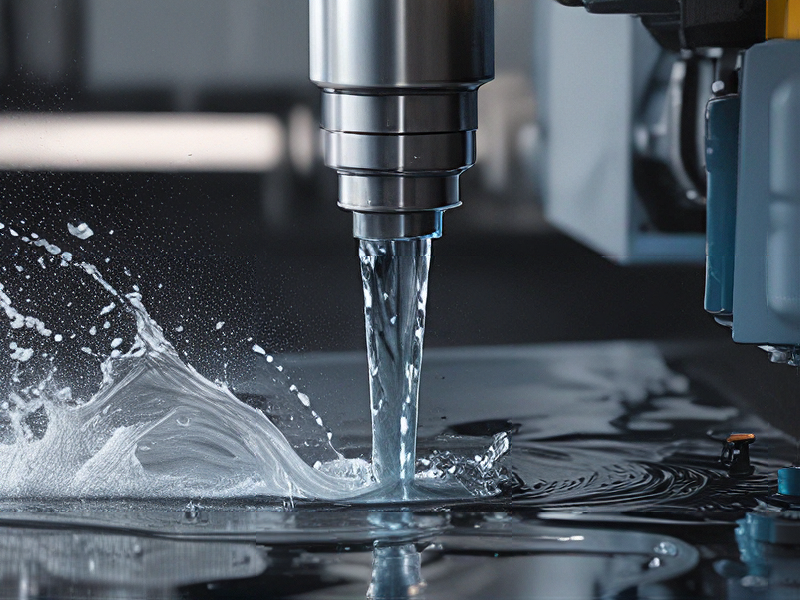
Quality Testing Methods for water machining and how to control quality
Quality testing methods for water machining involve various techniques to ensure that the water used in machining processes meets specific standards. Here are key methods and control strategies:
1. Physical Testing: This includes assessing parameters such as turbidity, temperature, and conductivity. Turbidity can indicate the presence of suspended solids, while conductivity helps in measuring ionic content.
2. Chemical Testing: pH, dissolved oxygen, total dissolved solids (TDS), and specific contaminants (like metals or biological agents) are analyzed using chemical tests. Regular testing ensures the water’s chemical composition remains within acceptable limits.
3. Biological Testing: Assessing microbiological content is crucial. Techniques such as culturing samples on agar plates can detect bacteria, while molecular methods can identify specific pathogens.
4. Filtration Systems: Implementing advanced filtration systems, such as reverse osmosis or ultrafiltration, can significantly enhance water quality by removing impurities and contaminants.
5. Regular Monitoring: Establishing a routine monitoring schedule helps in identifying deviations from quality standards. Automated sensors can continuously track key parameters.
6. Data Analysis: Utilizing data from testing to inform process adjustments or maintenance schedules ensures adherence to quality standards. Statistical process control (SPC) can aid in identifying trends and variations.
7. Training and Standard Operating Procedures (SOPs): Ensuring staff are well-trained in quality monitoring techniques and follow SOPs can reduce variations and maintain consistency in water quality.
By employing these quality testing methods and control strategies, water machining processes can operate more efficiently, reduce downtime, and ensure compliance with industry standards, ultimately leading to better product quality and sustainability.
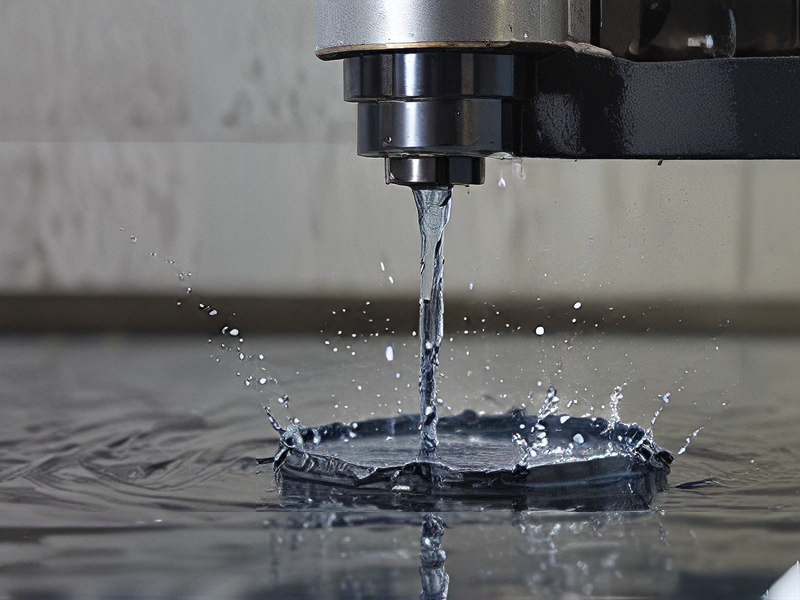
Tips for Procurement and Considerations when Purchasing from water machining
When purchasing water machining equipment, consider the following tips and considerations to ensure a successful procurement process:
1. Assess Your Needs: Clearly define your requirements, including the type of water machining you need (e.g., CNC cutting, water jet cutting) and volume of production. Understanding your specific applications will help in selecting the right machine.
2. Research Vendors: Evaluate potential suppliers based on their reputation, experience in the industry, and customer reviews. Look for vendors that specialize in the type of water machining equipment you’re interested in.
3. Quality and Technology: Investigate the technological advancements in water machining. Opt for machines that use high-quality components and are equipped with the latest technology for efficiency and precision.
4. Cost vs. Value: Compare pricing from different suppliers, but focus on value rather than just cost. Consider factors such as machine longevity, maintenance requirements, and potential for future upgrades.
5. Support and Service: Ensure the vendor offers robust after-sales support, including training, maintenance, and access to replacement parts. A strong support system can significantly reduce downtime.
6. Warranty and Guarantees: Look for machines that come with warranties and guarantees. This can provide peace of mind and protect your investment.
7. Sustainability Considerations: Evaluate the environmental impact of the machine and its efficiency in water usage. Choosing energy-efficient and resource-saving equipment aligns with sustainability goals.
8. Compliance and Safety: Confirm that the machinery complies with local regulations and safety standards to ensure a safe working environment.
By keeping these considerations in mind, you can make a more informed and strategic decision when purchasing water machining equipment.
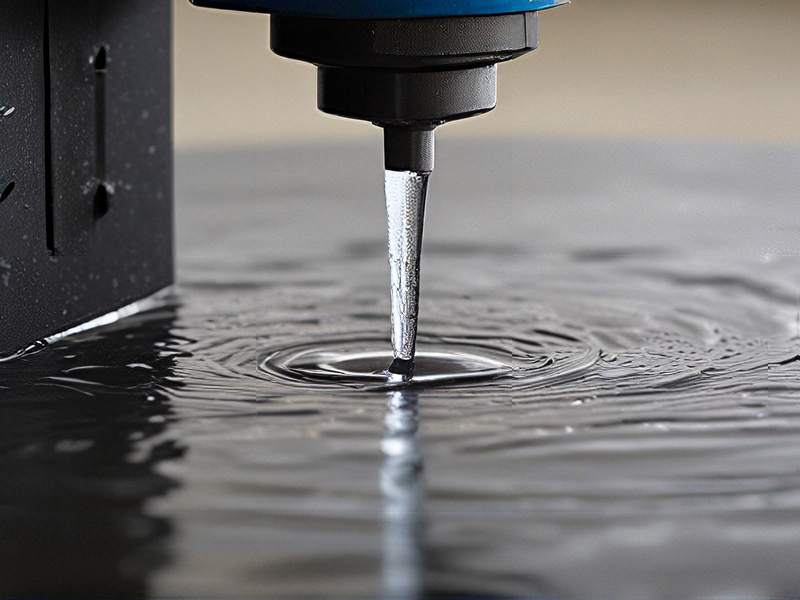
FAQs on Sourcing and Manufacturing from water machining in China
FAQs on Sourcing and Manufacturing Water Machining in China
1. What is water machining?
Water machining, also known as water jet cutting, is a manufacturing process that utilizes high-pressure water streams, often mixed with abrasives, to cut through various materials. It’s known for its precision and ability to handle complex shapes.
2. Why source water machining services in China?
China offers competitive pricing, advanced technology, and a robust manufacturing infrastructure. Many manufacturers specialize in water machining, providing access to innovative techniques and materials.
3. How do I find a reliable manufacturer?
Research potential manufacturers through platforms like Alibaba or Globalsources. Verify credentials, check reviews, and request samples. Attend trade shows in China, if possible, to meet manufacturers in person.
4. What are the quality control measures?
Reputable manufacturers implement rigorous quality control processes, including inspections at various stages of production, detailed documentation, and adherence to international standards (e.g., ISO 9001).
5. What are the typical lead times?
Lead times can vary but typically range from 2 to 6 weeks. Factors influencing this include order size, complexity, and backlog at the manufacturing facility.
6. How does shipping work?
Shipping options include sea freight and air freight, with sea freight being more cost-effective for large orders. Ensure to understand customs regulations and shipping costs to calculate total expenses accurately.
7. What payment terms are standard?
Payment terms can include a small advance payment (30-50%) with the balance due before shipping. Always negotiate terms and consider using escrow services to protect your investment.
8. Are there language barriers?
While many Chinese manufacturers speak basic English, it’s beneficial to have a translator or use clear, simple language to avoid miscommunication.
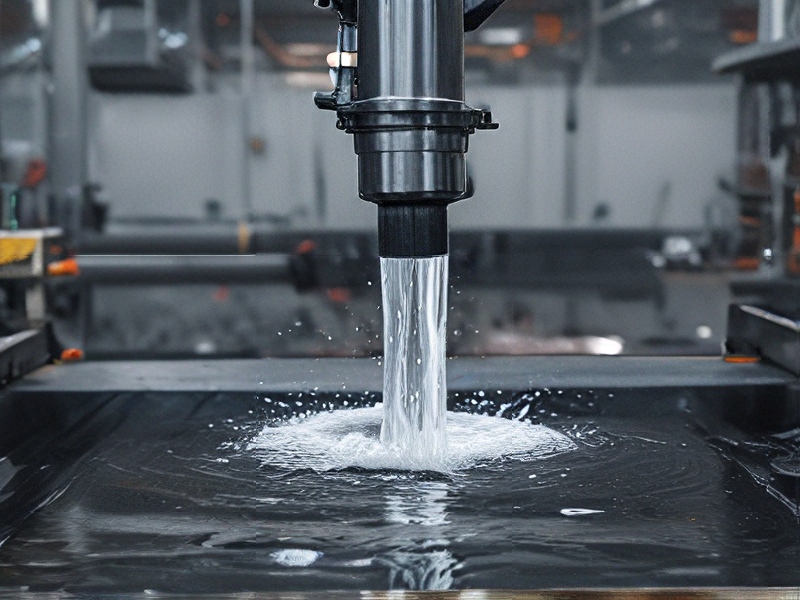