Technology and Applications of welder laser machine
Laser welding is a highly advanced technique that employs focused laser beams to join materials, offering precision, speed, and versatility unmatched by traditional welding methods. The technology utilizes a concentrated light source, capable of producing heat sufficient to melt and fuse various metals and some polymers without the need for filler materials.
Applications of Laser Welding:
1. Automotive Industry: Utilized for joining lightweight materials such as aluminum and high-strength steel, laser welding enhances vehicle safety and fuel efficiency while reducing weight.
2. Aerospace: Critical for assembling components that require high strength-to-weight ratios, laser welding is perfect for intricate parts in aircraft and spacecraft manufacturing.
3. Medical Devices: Ensures sterile and precise assembly of surgical instruments and implantable devices like pacemakers, where precision is paramount.
4. Electronics: Commonly used for micro-welding in the production of electronic components, including circuit boards and connectors, due to its ability to handle small scale jobs without damaging adjacent areas.
5. Jewelry Making: Allows artisans to create fine details and intricate designs in metalwork, offering a clean finish and minimizing material loss.
Technology Features: Laser welding machines are equipped with advanced features such as automated beam manipulation, computer control systems for precision alignment, and real-time monitoring for quality assurance. Techniques like fiber laser and diode laser systems are popular for their efficiency and flexibility in handling various materials.
Overall, laser welding represents a progressive shift in fabrication technology, offering numerous benefits including reduced thermal distortion, improved joint quality, and enhanced productivity in diverse industrial applications.
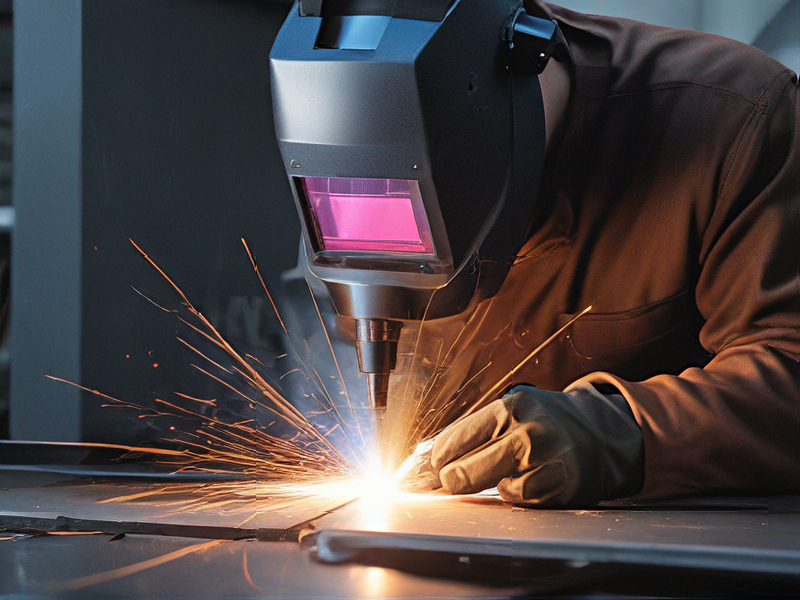
Quality Testing Methods for welder laser machine and how to control quality
Quality testing for a laser welding machine involves several methods to ensure precision, reliability, and performance. Here are key quality testing methods and their controls:
1. Visual Inspection: Regularly examine welds for defects such as cracks, undercuts, or inconsistent bead appearance. Use magnification tools for finer details.
2. Dimensional Accuracy: Use calipers and gauges to measure the dimensions of the welds and ensure they meet specifications. This is crucial for components requiring precise fit.
3. Tensile Testing: Conduct tensile tests on weld specimens to assess strength and ductility. This helps determine if the weld can withstand expected loads.
4. Non-Destructive Testing (NDT): Employ methods like ultrasonic testing, radiography, and dye penetrant testing to detect internal flaws without damaging the parts.
5. Heat Affected Zone (HAZ) Analysis: Analyze the HAZ for metallurgical properties, ensuring that the material’s integrity around the weld is not compromised.
6. Machine Calibration: Regularly calibrate the laser machine settings (power, speed, focus) to maintain consistency in weld quality.
7. Process Monitoring: Implement real-time monitoring systems for parameters such as laser power, travel speed, and cooling rates. This allows for immediate adjustments if deviations occur.
8. Standard Operating Procedures (SOPs): Establish and follow SOPs for laser welding. Continuous training of operators enhances quality consistency.
9. Documentation and Reporting: Maintain thorough records of all tests and inspections. Analyzing this data can identify trends and areas for improvement.
By integrating these methods into a comprehensive quality control program, you can ensure high-quality welds and improve the reliability of laser welding operations.
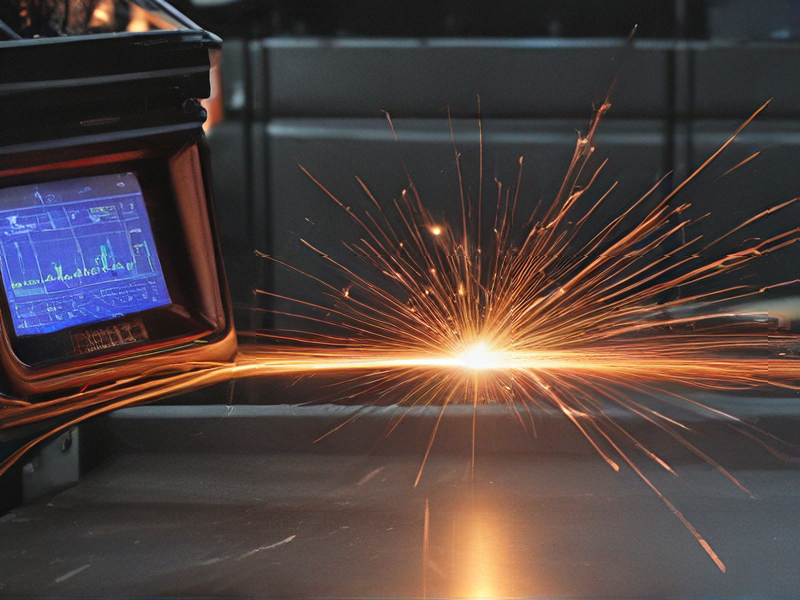
Tips for Procurement and Considerations when Purchasing from welder laser machine
When purchasing a welder laser machine, consider the following tips and considerations to ensure you make an informed decision:
1. Determine Your Needs: Assess the specific projects you’ll be using the laser welder for. Consider the materials you’ll be welding, the thickness, and the required precision.
2. Research Technology: Familiarize yourself with the types of laser welding technologies available, such as fiber lasers or CO2 lasers. Fiber lasers are often preferred for their efficiency and versatility.
3. Evaluate Power and Speed: Look for machines with adequate wattage for your applications. Higher power can increase speed, but it’s important to match wattage to your material and thickness requirements.
4. Check Quality Standards: Ensure the machine complies with industry standards and certifications. This can impact the quality of the welds and the machine’s longevity.
5. Read Reviews and Testimonials: Research the manufacturers and models through customer reviews, case studies, and testimonials to gauge performance and reliability.
6. Consider Ergonomics and Ease of Use: Look for machines with user-friendly interfaces and ergonomic designs to enhance productivity and reduce operator fatigue.
7. Evaluate Support and Service: Consider the manufacturer’s reputation for customer support, including availability of spare parts, technical assistance, and warranty options.
8. Total Cost of Ownership: Beyond the initial purchase price, factor in maintenance costs, operational costs (energy consumption), and potential downtimes.
9. Training and Implementation: Determine what training is necessary for operators and how the machine will be integrated into your existing operations.
10. Future-Proofing: Consider models that allow for upgrades or expansion to adapt to future technological advancements or changes in production needs.
By carefully considering these factors, you can make a sound investment in a laser welder that meets your business requirements.
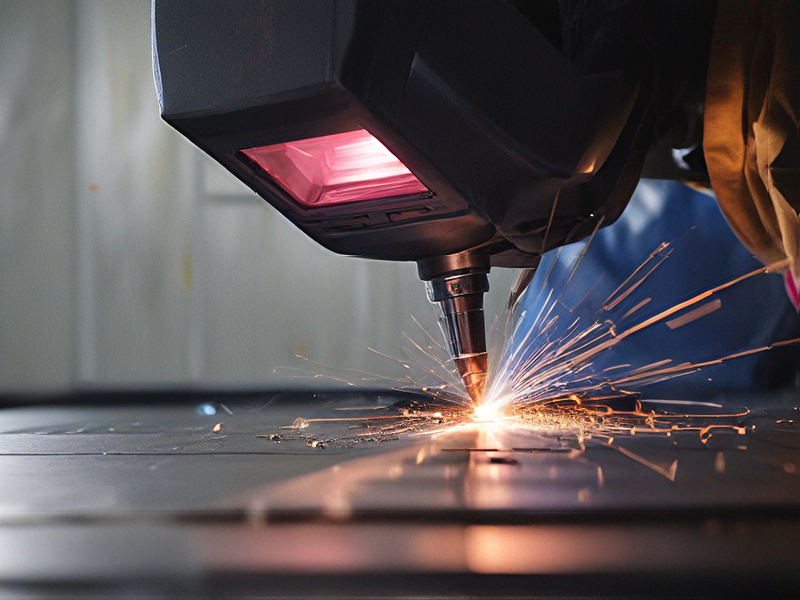
FAQs on Sourcing and Manufacturing from welder laser machine in China
FAQs on Sourcing and Manufacturing Welder Laser Machines in China
1. Why source laser welding machines from China?
China is known for its manufacturing capabilities, competitive pricing, and a wide variety of suppliers. The country has invested heavily in advanced technology, making it a leader in producing high-quality laser welding machines.
2. What should I consider when choosing a supplier?
Evaluate the supplier’s experience, reputation, and certifications (like ISO). Request references from past clients and assess their ability to provide after-sales support and warranty services.
3. How can I ensure product quality?
Request samples and consider conducting a factory audit. It’s also wise to use quality control services or third-party inspectors to verify that products meet your specifications before shipping.
4. What are the common payment terms?
Payment terms can vary, but a typical arrangement is a 30% deposit upfront and 70% before shipment. Some suppliers may offer different terms depending on the relationship and order size.
5. How do I handle shipping and logistics?
Most suppliers can assist with shipping logistics. Consider the Incoterms (like FOB, CIF) that define who is responsible for costs and risks at different stages of shipping.
6. What are the lead times for manufacturing?
Lead times can vary based on the complexity and volume of the order. Generally, expect anywhere from 30 to 90 days. Always confirm timelines with the supplier before placing an order.
7. Are there export duties or tariffs?
Yes, there may be duties or tariffs imposed by your country when importing laser welding machines from China. It’s essential to research and comply with local import regulations before sourcing.
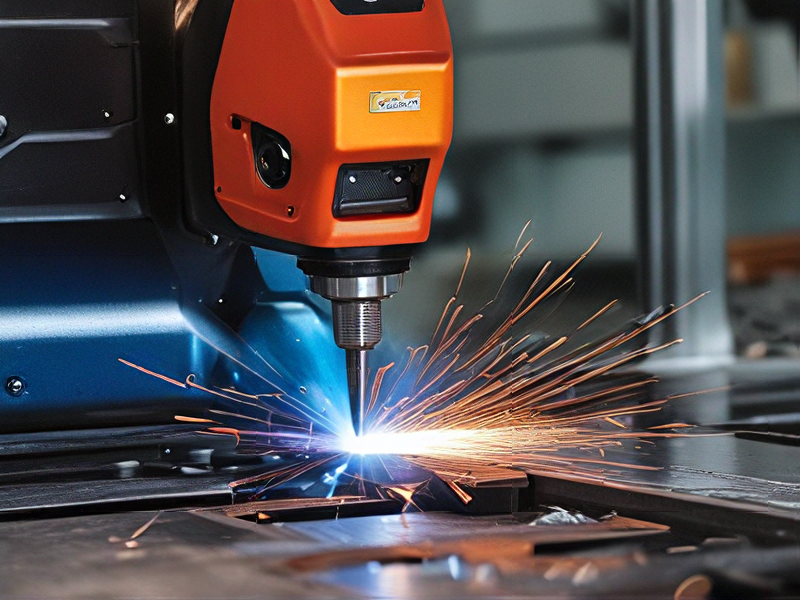