Technology and Applications of wire discharge machining
Wire Electrical Discharge Machining (EDM) is a precise manufacturing process used to cut intricate shapes in conductive materials using a thin, electrically charged wire. This wire, typically made of brass or copper, is guided by computer numerical control (CNC) to create highly accurate cuts through the material.
The process involves generating electrical discharges (sparks) between the wire and the workpiece submerged in dielectric fluid. These sparks erode the material, creating the desired shape. Wire EDM is particularly valued for its ability to cut complex shapes with tight tolerances, where traditional machining methods are impractical.
Applications of wire EDM span various industries including aerospace, automotive, medical, and toolmaking. It’s used for making dies, molds, and punches, where precision and intricate detailing are critical. Wire EDM can cut hardened materials that are challenging to machine conventionally, such as titanium and hardened steels, without inducing thermal stresses.
Advantages include minimal tool wear due to the absence of direct contact between the wire and the workpiece, which prolongs tool life and reduces maintenance costs. Additionally, it enables high aspect ratio cuts (deep and narrow features) with excellent surface finish.
Challenges include slower cutting speeds compared to some other machining methods, and the need for skilled operators to optimize parameters like wire tension, power settings, and flushing conditions.
In summary, wire EDM is a versatile and precise manufacturing technique ideal for producing intricate shapes in hard materials across various industries, where traditional machining methods fall short.
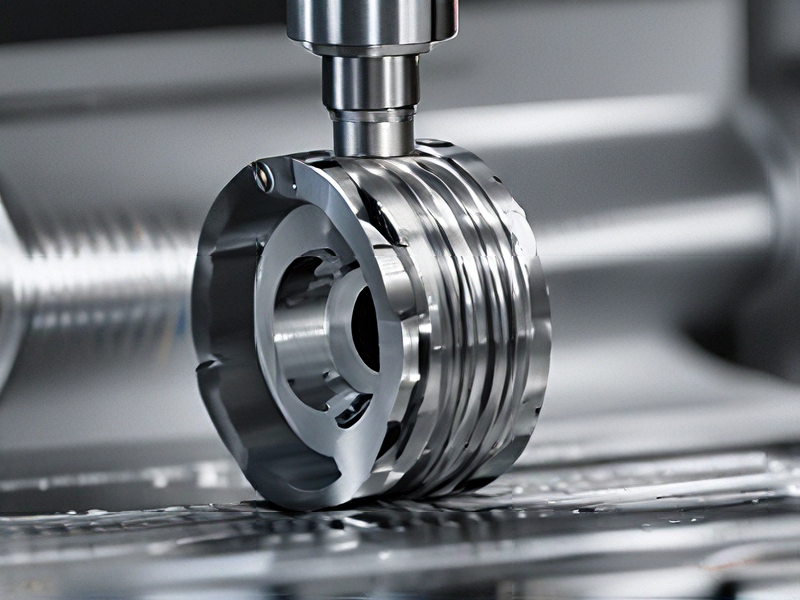
Quality Testing Methods for wire discharge machining and how to control quality
Quality Testing Methods for Wire Discharge Machining (WDM):
1. Dimensional Accuracy: Use coordinate measuring machines (CMM) or optical comparators to ensure the machined parts meet specified dimensions and tolerances.
2. Surface Roughness: Measure surface finish using profilometers. A smooth surface indicates good quality.
3. Material Integrity: Perform non-destructive testing (NDT) methods such as ultrasonic testing and X-ray inspection to detect internal flaws or cracks without damaging the part.
4. Hardness Testing: Use hardness testers (e.g., Rockwell or Vickers) to ensure the material’s hardness has not been adversely affected by the machining process.
5. Cutting Speed and Feed Rate Analysis: Monitor and analyze the cutting speed and feed rates to ensure they are within optimal ranges to maintain consistent quality.
6. Electrical Parameter Monitoring: Track voltage, current, and pulse duration to ensure they are within specified ranges, as these parameters directly affect machining quality.
Quality Control Measures:
1. Calibration: Regularly calibrate all measuring instruments and machinery to maintain accuracy and reliability.
2. Process Standardization: Establish and adhere to standard operating procedures (SOPs) for the WDM process, ensuring consistency in operations.
3. Operator Training: Ensure that operators are well-trained and understand the importance of each parameter and its impact on the final product quality.
4. Real-time Monitoring: Implement real-time monitoring systems for critical parameters such as voltage, current, and cutting speed. Use software to track and alert deviations from the set standards.
5. Regular Maintenance: Perform regular maintenance on the WDM equipment to prevent wear and tear from affecting machining accuracy and quality.
6. Statistical Process Control (SPC): Utilize SPC techniques to monitor and control the process variations, enabling early detection of potential quality issues.
7. Feedback Loop: Establish a feedback loop from quality inspection results to process adjustments, ensuring continuous improvement and immediate correction of any identified defects.
By integrating these testing methods and control measures, the quality of wire discharge machining can be effectively managed and maintained.
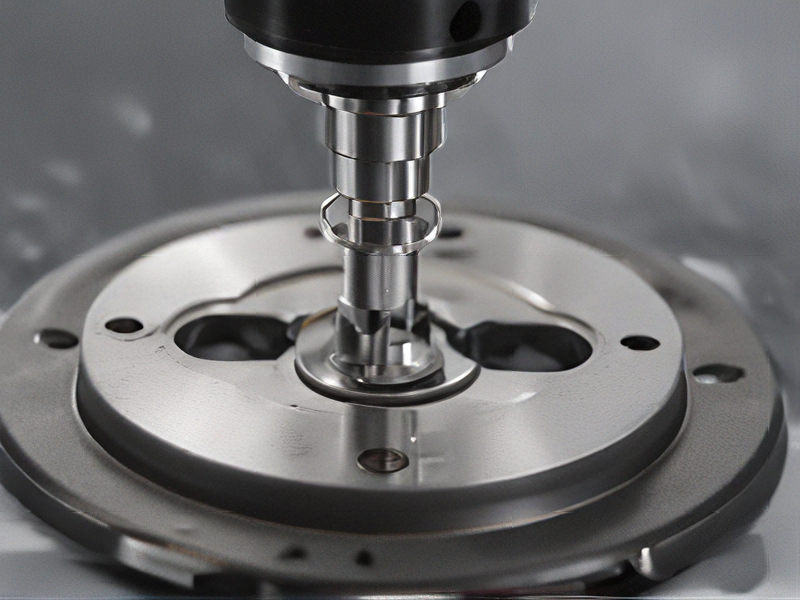
Tips for Procurement and Considerations when Purchasing from wire discharge machining
When procuring wire electrical discharge machining (EDM) services, consider these key tips and factors:
1. Supplier Experience and Reputation: Look for suppliers with a proven track record in wire EDM. Check reviews, testimonials, and past projects to gauge their reliability and quality.
2. Technology and Capabilities: Ensure the supplier uses state-of-the-art EDM equipment capable of handling your specific requirements. Ask about their machine capabilities, tolerances, and material expertise.
3. Quality Assurance: Inquire about their quality control measures. Certifications like ISO 9001 indicate adherence to international standards. Request samples or visit their facility if possible to inspect their processes.
4. Turnaround Time: Evaluate their ability to meet your deadlines. Discuss lead times, production schedules, and any potential delays they foresee.
5. Cost and Pricing Structure: Obtain detailed quotes outlining costs for setup, machining, material, and any additional services. Compare pricing with other suppliers while considering their reputation and quality.
6. Communication and Support: Clear communication is crucial. Ensure they are responsive to inquiries and provide updates throughout the project. A dedicated point of contact enhances collaboration.
7. Flexibility and Customization: Determine if the supplier can accommodate special requests or modifications to standard processes. Flexibility is valuable in meeting unique project requirements.
8. Location and Logistics: Consider proximity to your location to minimize shipping costs and transit times. Evaluate their shipping methods and packaging to ensure the safe delivery of finished parts.
9. Customer Service and After-Sales Support: Assess their commitment to customer satisfaction. Reviews and references can provide insights into their after-sales service and support.
10. Long-Term Partnership Potential: Building a long-term relationship with a reliable supplier can offer benefits like preferential pricing, priority scheduling, and improved service over time.
By carefully evaluating these factors and discussing them with potential suppliers, you can make informed decisions when procuring wire EDM services that align with your project requirements and expectations.
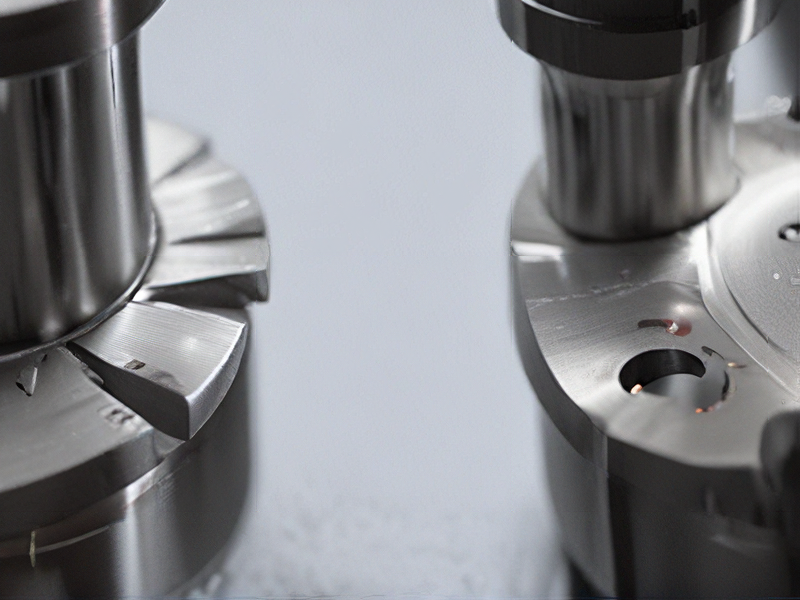
FAQs on Sourcing and Manufacturing from wire discharge machining in China
Certainly! When sourcing and manufacturing via wire discharge machining (WDM) in China, here are some frequently asked questions (FAQs):
1. What is wire discharge machining (WDM)?
Wire discharge machining, also known as wire EDM or WEDM, is a process where a thin, electrically charged wire is used to cut through metal with high precision.
2. Why consider China for WDM?
China offers competitive pricing due to lower labor and production costs, coupled with advanced manufacturing capabilities in WDM technology.
3. How to select a reliable supplier in China?
Look for suppliers with a proven track record in WDM, certifications (like ISO), and positive client testimonials. Conducting factory audits can also ensure compliance with quality standards.
4. What are the typical lead times for WDM in China?
Lead times vary based on complexity and volume but generally range from a few days to several weeks. Communication with suppliers about timelines is crucial for planning.
5. How does quality control work in Chinese WDM facilities?
Established suppliers adhere to strict quality control measures throughout the manufacturing process. Inspections, testing, and adherence to international standards are common practices.
6. Are there intellectual property concerns when manufacturing in China?
It’s important to have clear agreements and enforceable contracts regarding intellectual property rights (IPR) to safeguard designs and innovations.
7. What are the advantages of WDM over other machining methods?
WDM offers high accuracy, intricate detailing capabilities, and the ability to work with hard metals that may be challenging for conventional machining methods.
8. What should be considered for shipping and logistics?
Factor in shipping costs, packaging requirements, and potential import/export regulations to avoid delays and ensure smooth delivery.
Navigating these considerations can help in effectively leveraging wire discharge machining services in China for sourcing and manufacturing needs.
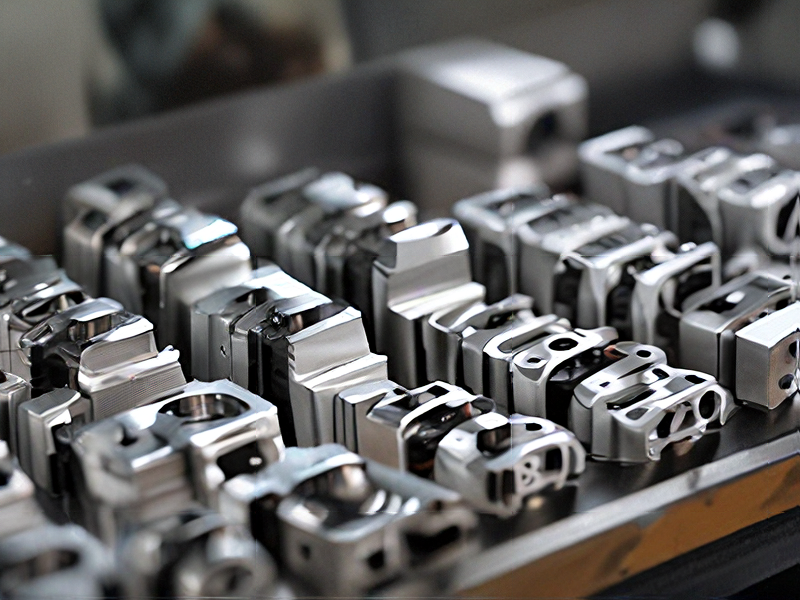