Technology and Applications of wire edm machine
Wire Electrical Discharge Machining (EDM) is a specialized manufacturing process used for shaping conductive materials using electrical discharges. This technology is particularly valued for its ability to cut intricate shapes with high precision, even in materials that are typically difficult to machine with conventional methods.
In wire EDM, a thin, electrically charged wire is used as an electrode, and a controlled electrical spark discharge erodes the material to create the desired shape. The wire is guided along a programmed path, usually controlled by CNC (Computer Numerical Control), ensuring accuracy down to micrometer levels. This method is highly advantageous for producing complex shapes, fine details, and sharp corners in materials such as hardened steel, titanium, and exotic alloys.
Applications of wire EDM span various industries including aerospace, automotive, medical device manufacturing, and electronics. It is commonly used for producing molds, dies, and tooling where precision and surface finish are critical. The process is also favored for creating prototypes and small production runs where traditional machining techniques may be impractical or time-consuming.
Key benefits of wire EDM include minimal mechanical stress on the workpiece, which helps preserve material integrity, and the ability to cut intricate contours without the need for additional tooling changes. However, the process can be relatively slow compared to conventional machining, particularly for thicker materials, and requires skilled operators to optimize cutting parameters for each application.
In conclusion, wire EDM technology continues to be indispensable in industries requiring high precision and intricate machining capabilities. Its ability to work with a wide range of materials and produce complex shapes makes it a cornerstone in modern manufacturing processes.
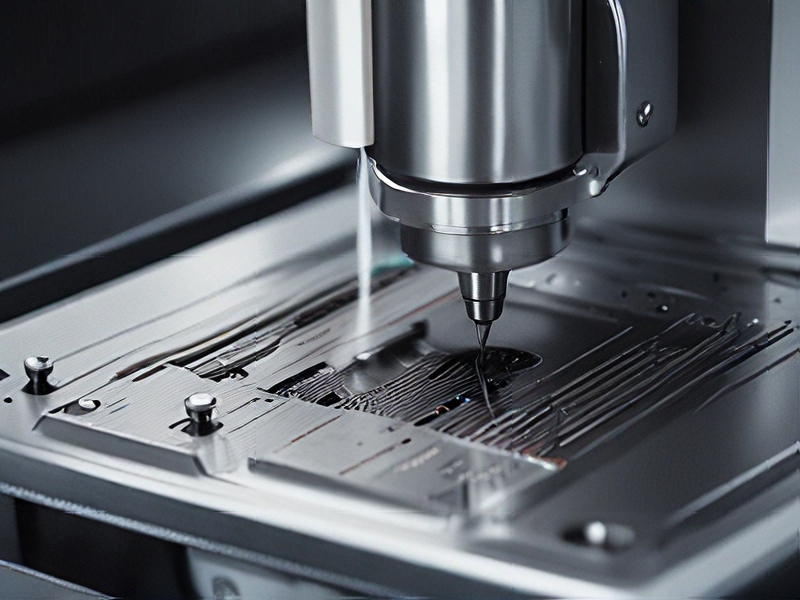
Quality Testing Methods for wire edm machine and how to control quality
Quality testing methods for Wire EDM (Electrical Discharge Machining) machines typically involve the following approaches to ensure precise control and maintenance of quality:
1. Dimensional Accuracy: Use precision measuring instruments like micrometers, calipers, and coordinate measuring machines (CMM) to verify the accuracy of machined dimensions against design specifications.
2. Surface Finish: Employ surface roughness testers to assess the quality of surface finishes achieved by the EDM process. This ensures that the specified surface texture requirements are met.
3. Wire Tension and Alignment: Regularly check and adjust wire tension and alignment to ensure consistent cutting performance and dimensional accuracy.
4. Electrical Discharge Monitoring: Monitor the electrical discharge parameters such as current, voltage, and pulse duration to maintain stable machining conditions and prevent defects.
5. Edge Integrity: Inspect machined edges for burrs, cracks, or other imperfections using visual inspection or magnification techniques.
To control quality effectively:
– Establish Standard Operating Procedures (SOPs): Define and document procedures for machine setup, operation, and maintenance to ensure consistency and repeatability.
– Training and Skills Development: Train operators on proper machine operation, maintenance practices, and quality inspection techniques.
– Regular Maintenance: Implement a preventive maintenance schedule to keep the machine in optimal condition and minimize downtime.
– Quality Assurance Checks: Conduct periodic audits and inspections to verify adherence to quality standards and identify areas for improvement.
– Feedback Loop: Establish a feedback mechanism to capture and address issues promptly, improving overall quality control.
By integrating these testing methods and quality control measures, manufacturers can maintain high standards of precision and reliability in Wire EDM machining processes.
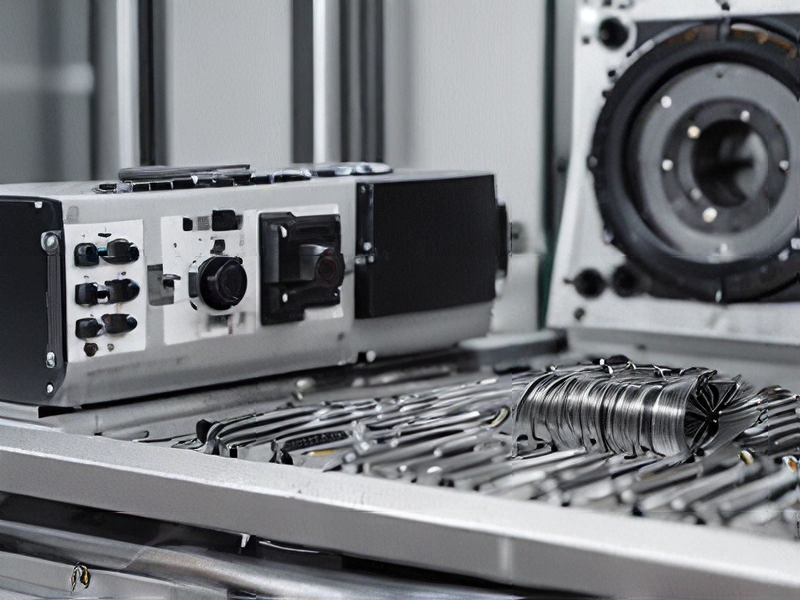
Tips for Procurement and Considerations when Purchasing from wire edm machine
When procuring a wire EDM (Electrical Discharge Machining) machine, several key considerations can ensure you make an informed decision:
1. Machine Specifications: Evaluate the machine’s specifications such as cutting speed, accuracy, and tolerance levels. Consider your specific manufacturing needs and ensure the machine can handle the materials and thicknesses you work with.
2. Technology and Features: Look for advanced features like automatic wire threading, CNC controls, and software compatibility for efficient operation and ease of use. Compatibility with CAD/CAM software can streamline your workflow.
3. Reliability and Durability: Assess the reputation of the manufacturer and the reliability of the machine. Read reviews, ask for references, and inquire about maintenance requirements and service support.
4. Cost and ROI: Compare prices from different suppliers, but also consider the long-term return on investment (ROI). A slightly higher upfront cost may be justified by lower operating costs and higher productivity over time.
5. Training and Support: Ensure the supplier provides adequate training for your operators and ongoing technical support. This is crucial for maximizing the machine’s capabilities and minimizing downtime.
6. Space and Installation: Consider the physical space available for installation and the machine’s power requirements. Ensure compatibility with your facility’s infrastructure.
7. Safety and Compliance: Check that the machine meets safety standards and regulatory requirements in your industry or region. Safety features should be robust to protect operators and ensure compliance.
8. Future Expansion: Anticipate future needs and assess whether the machine can be upgraded or expanded to accommodate growing production demands or new technological advancements.
By thoroughly evaluating these factors, you can make a well-informed procurement decision that aligns with your manufacturing goals and operational requirements.
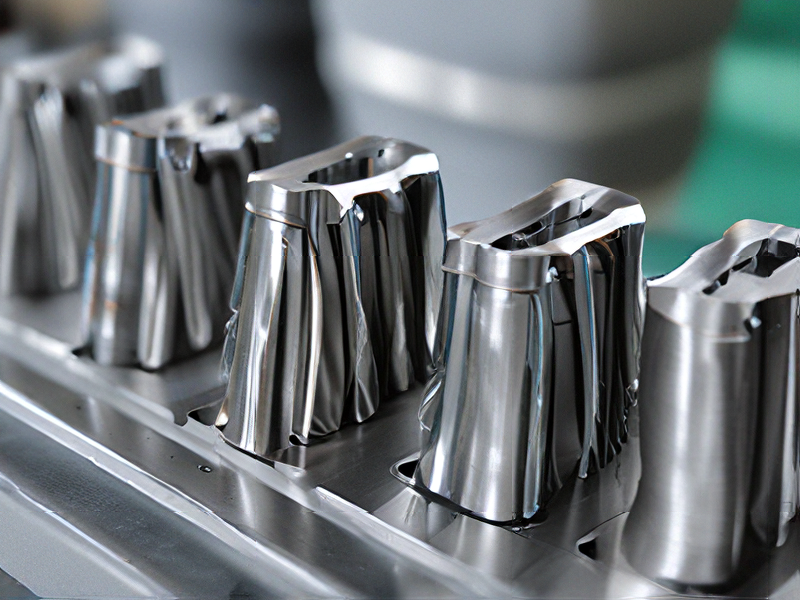
FAQs on Sourcing and Manufacturing from wire edm machine in China
Certainly! Here are some frequently asked questions (FAQs) regarding sourcing and manufacturing from wire EDM machines in China:
1. What is wire EDM (Electrical Discharge Machining)?
Wire EDM is a manufacturing process that uses electrical discharges to shape materials, typically metals, by cutting through them with a thin electrode wire.
2. Why source wire EDM machines from China?
China is known for its advanced manufacturing capabilities and cost-effective production. Many companies choose China for wire EDM machines due to competitive pricing and a wide range of machine options.
3. How do I select a reliable supplier in China?
Look for suppliers with a proven track record in manufacturing wire EDM machines. Verify their certifications, such as ISO standards, and check client testimonials or reviews for reliability.
4. What are the typical lead times for wire EDM machines from China?
Lead times can vary depending on the supplier and specific machine requirements. Generally, they range from a few weeks to a couple of months, including manufacturing and shipping.
5. Are there quality concerns with wire EDM machines from China?
Quality can vary between suppliers, so it’s crucial to conduct thorough due diligence. Request samples or visit the manufacturer if possible. Ensure they adhere to international quality standards.
6. What are the payment terms usually accepted by Chinese suppliers?
Common payment terms include T/T (Telegraphic Transfer), L/C (Letter of Credit), and occasionally, Alibaba’s Trade Assurance. Negotiate terms that ensure security and transparency for both parties.
7. Do Chinese suppliers provide after-sales support for wire EDM machines?
Many reputable suppliers offer comprehensive after-sales support, including technical assistance, spare parts availability, and sometimes on-site maintenance services.
8. How can I manage quality control when manufacturing wire EDM machines in China?
Implement stringent quality control processes and inspections throughout production. Consider hiring a third-party inspection service to ensure compliance with your specifications.
Navigating sourcing and manufacturing from China for wire EDM machines involves careful planning, clear communication, and diligent supplier evaluation to ensure successful outcomes.
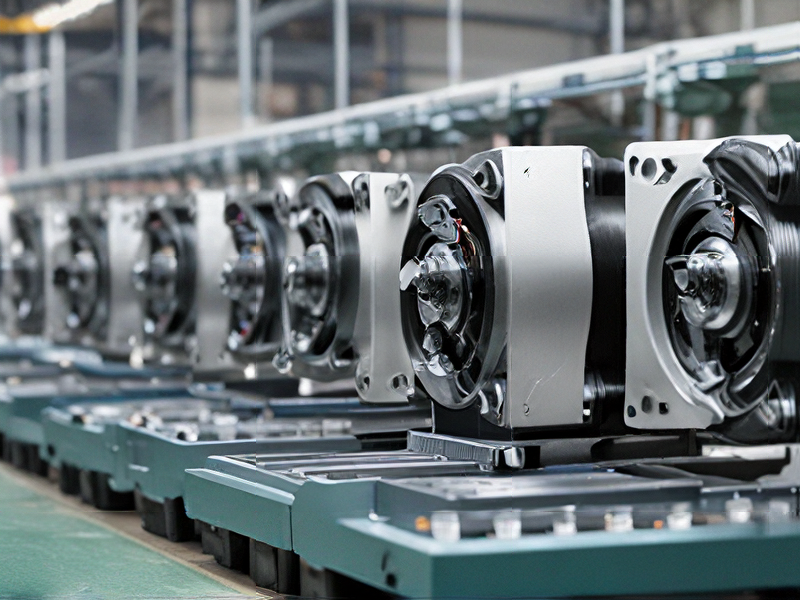